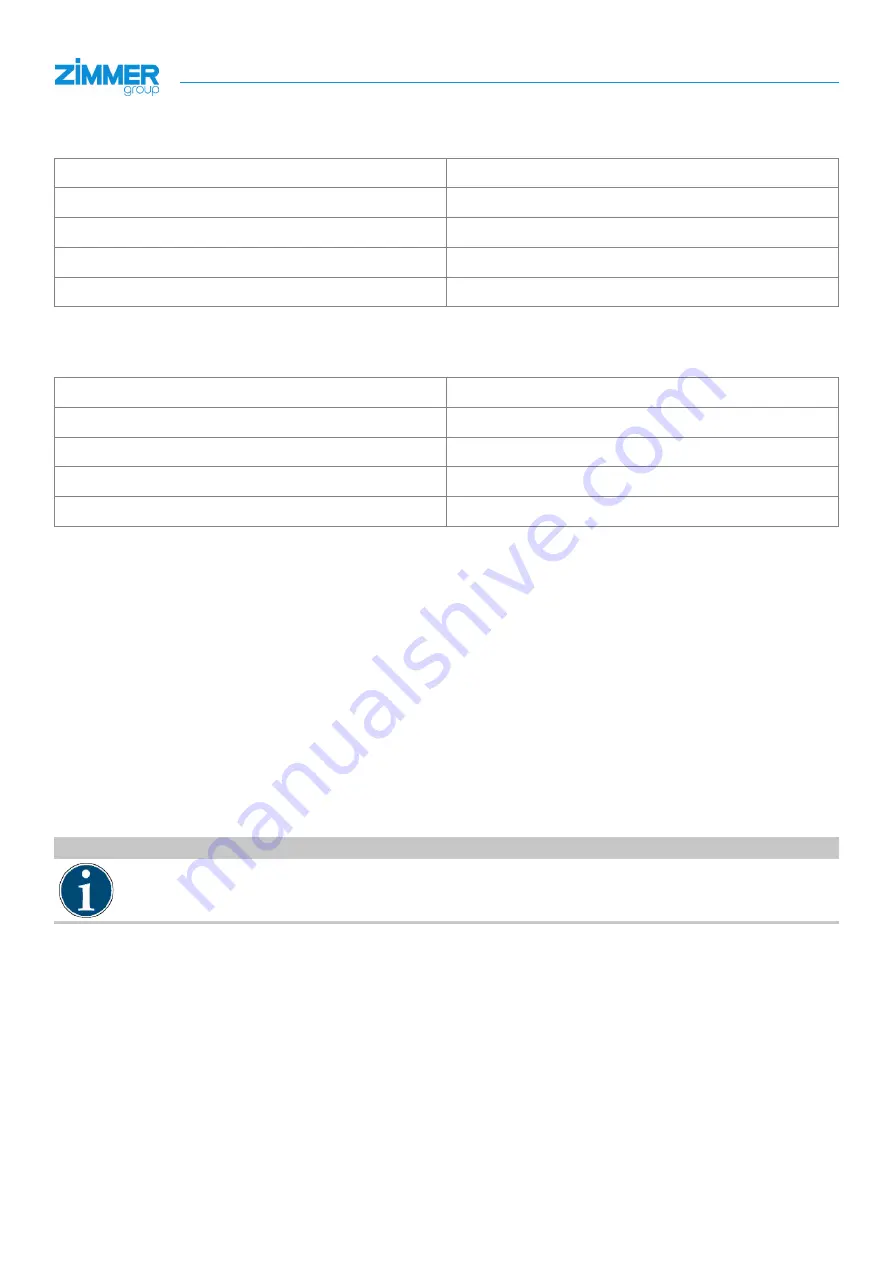
Zimmer GmbH
•
Im Salmenkopf 5
•
77866 Rheinau, Germany
•
+49 7844 9138 0
•
+49 7844 9138 80
•
www.zimmer-group.com
28
INSTALLATION AND OPERATING INSTRUCTIONS:
2-jaw parallel gripper, electric, GEP2000IL-03 series
EN / 2021-03-04
DDOC01219 / 0
8.4 Minimum travel path
The gripper requires a certain "minimum travel path" to move to the desired position.
Design size
Minimum travel path
GEP2006IL-03
1.0 mm per gripper jaw
GEP2010IL-03
1.0 mm per gripper jaw
GEP2013IL-03
1.0 mm per gripper jaw
GEP2016IL-03
1.0 mm per gripper jaw
8.5 Minimum startup path
The gripper requires a certain "minimum startup path" to reach the desired gripping force.
Design size
Minimum travel path
GEP2006IL-03
0.5 mm per gripper jaw
GEP2010IL-03
0.5 mm per gripper jaw
GEP2013IL-03
0.5 mm per gripper jaw
GEP2016IL-03
0.5 mm per gripper jaw
8.6 "Easy Startup"
From switching on the gripper to the initial movement.
►
Connect the gripper according to its assignment diagram.
Ö
The gripper reports the "StatusWord," "Diagnosis" and "ActualPosition" process data immediately after the internal
controller is booted up.
Ö
Once the "PLCActive" bit is registered in the "StatusWord," the communication process can start. To move the gripper,
the process parameters must first be transmitted.
►
Transmit the following process parameters:
• "DeviceMode"
•
"GripForce" for "DeviceMode" 103 or "DriveVelocity" for "DeviceMode" 50
• "BasePosition"
• "WorkPosition"
Ö
A "handshake" is required to transmit the process parameters to the gripper.
INFORMATION
For information about the "Handshake," refer to the "Handshake" data transfer method section.