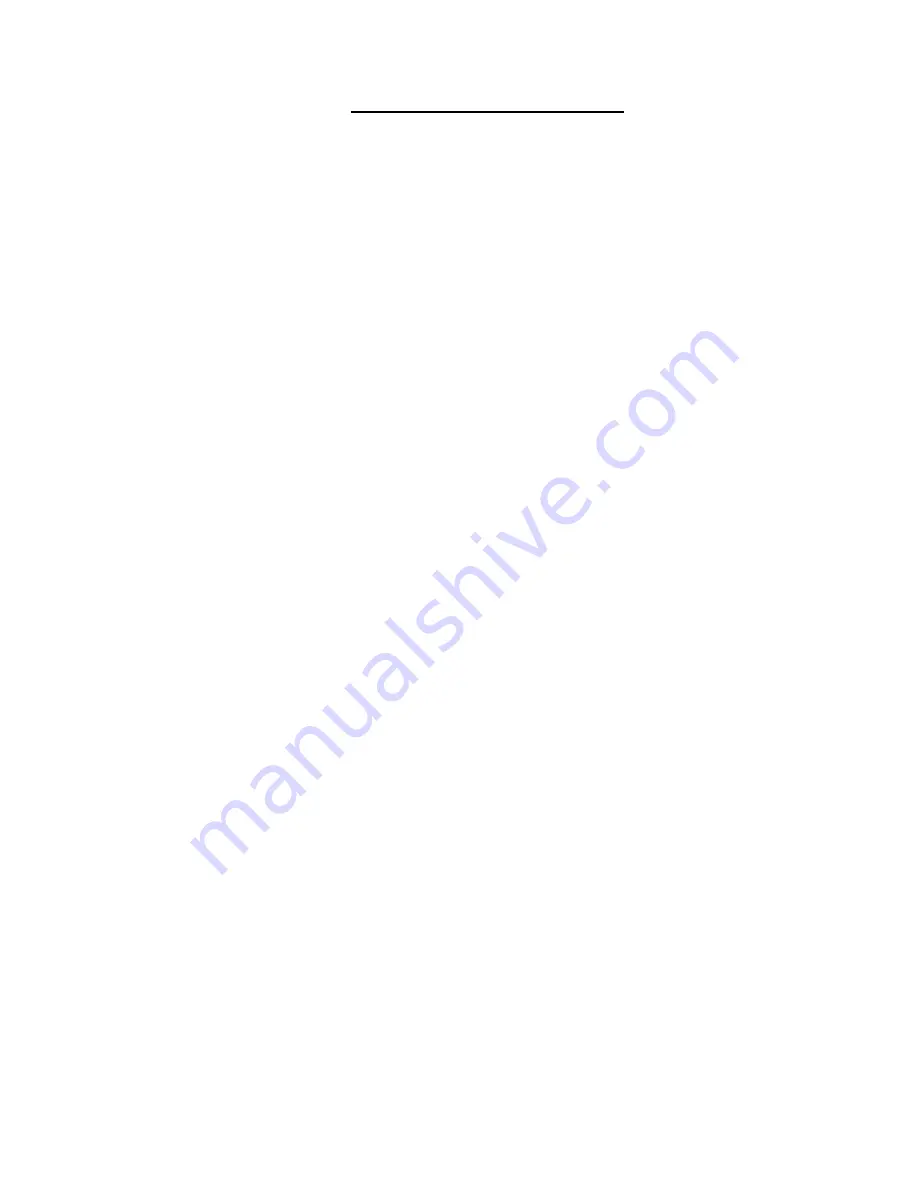
Page 1
MM13050 Rev.B 11/01
ClearCommand MS565-13050
SW
13447.3
Table of Contents
1.0 INTRODUCTION - - - - - - - - - - - - - - - - - - - - - - - - - - - - - - - - - - - - - - - - - 1
1.1 This Manual . . . . . . . . . . . . . . . . . . . . . . . . . . . . . . . . . . . . . . . . . . . . . . . . . . . . . . . . . . . . . . . . . . . . . . . . . . . . . . . . . 1
1.2 ClearCommand System. . . . . . . . . . . . . . . . . . . . . . . . . . . . . . . . . . . . . . . . . . . . . . . . . . . . . . . . . . . . . . . . . . . . . . . . . 2
2.2 Engine Start Interlock . . . . . . . . . . . . . . . . . . . . . . . . . . . . . . . . . . . . . . . . . . . . . . . . . . . . . . . . . . . . . . . . . . . . . . . . . . 4
2.3 Station Transfer. . . . . . . . . . . . . . . . . . . . . . . . . . . . . . . . . . . . . . . . . . . . . . . . . . . . . . . . . . . . . . . . . . . . . . . . . . . . . . . 5
2.5 Synchronization (Multi Screw) . . . . . . . . . . . . . . . . . . . . . . . . . . . . . . . . . . . . . . . . . . . . . . . . . . . . . . . . . . . . . . . . . . . 6
2.6 Control Head Tones . . . . . . . . . . . . . . . . . . . . . . . . . . . . . . . . . . . . . . . . . . . . . . . . . . . . . . . . . . . . . . . . . . . . . . . . . . . 7
2.7 Speed Boost Operation . . . . . . . . . . . . . . . . . . . . . . . . . . . . . . . . . . . . . . . . . . . . . . . . . . . . . . . . . . . . . . . . . . . . . . . . . 8
3.0 REQUIRED PARTS AND TOOLS - - - - - - - - - - - - - - - - - - - - - - - - - - - - - - - - - 9
3.2 Control Head . . . . . . . . . . . . . . . . . . . . . . . . . . . . . . . . . . . . . . . . . . . . . . . . . . . . . . . . . . . . . . . . . . . . . . . . . . . . . . . . . 9
3.3 Electric Cable . . . . . . . . . . . . . . . . . . . . . . . . . . . . . . . . . . . . . . . . . . . . . . . . . . . . . . . . . . . . . . . . . . . . . . . . . . . . . . . 10
3.4 Tools Required For Installation . . . . . . . . . . . . . . . . . . . . . . . . . . . . . . . . . . . . . . . . . . . . . . . . . . . . . . . . . . . . . . . . . 10
3.5 Push-Pull Cable. . . . . . . . . . . . . . . . . . . . . . . . . . . . . . . . . . . . . . . . . . . . . . . . . . . . . . . . . . . . . . . . . . . . . . . . . . . . . . 11
3.6 Wire Harness . . . . . . . . . . . . . . . . . . . . . . . . . . . . . . . . . . . . . . . . . . . . . . . . . . . . . . . . . . . . . . . . . . . . . . . . . . . . . . . 11
4.0 PLAN THE INSTALLATION - - - - - - - - - - - - - - - - - - - - - - - - - - - - - - - - - - - 13
Содержание ClearCommand
Страница 56: ......
Страница 57: ...APPENDIX A 1 ...
Страница 58: ......
Страница 60: ...Appendix A 6 20 01 Page 2 ...
Страница 63: ...Page 5 ...
Страница 64: ...Page 6 ...
Страница 68: ...Page 10 ...
Страница 70: ...Page 12 ...
Страница 72: ...Page 14 ...
Страница 78: ...Page 20 ...
Страница 82: ...Page 24 ...
Страница 85: ...APPENDIX B 1 ...
Страница 86: ......
Страница 97: ...APPENDIX C 1 ...
Страница 98: ......
Страница 99: ...Drawing 11202F 1 ...
Страница 100: ... ...
Страница 101: ...Drawing 11202F 2 ...
Страница 102: ... ...
Страница 103: ...Drawing 11202F 3 Notes Page ...
Страница 104: ... ...