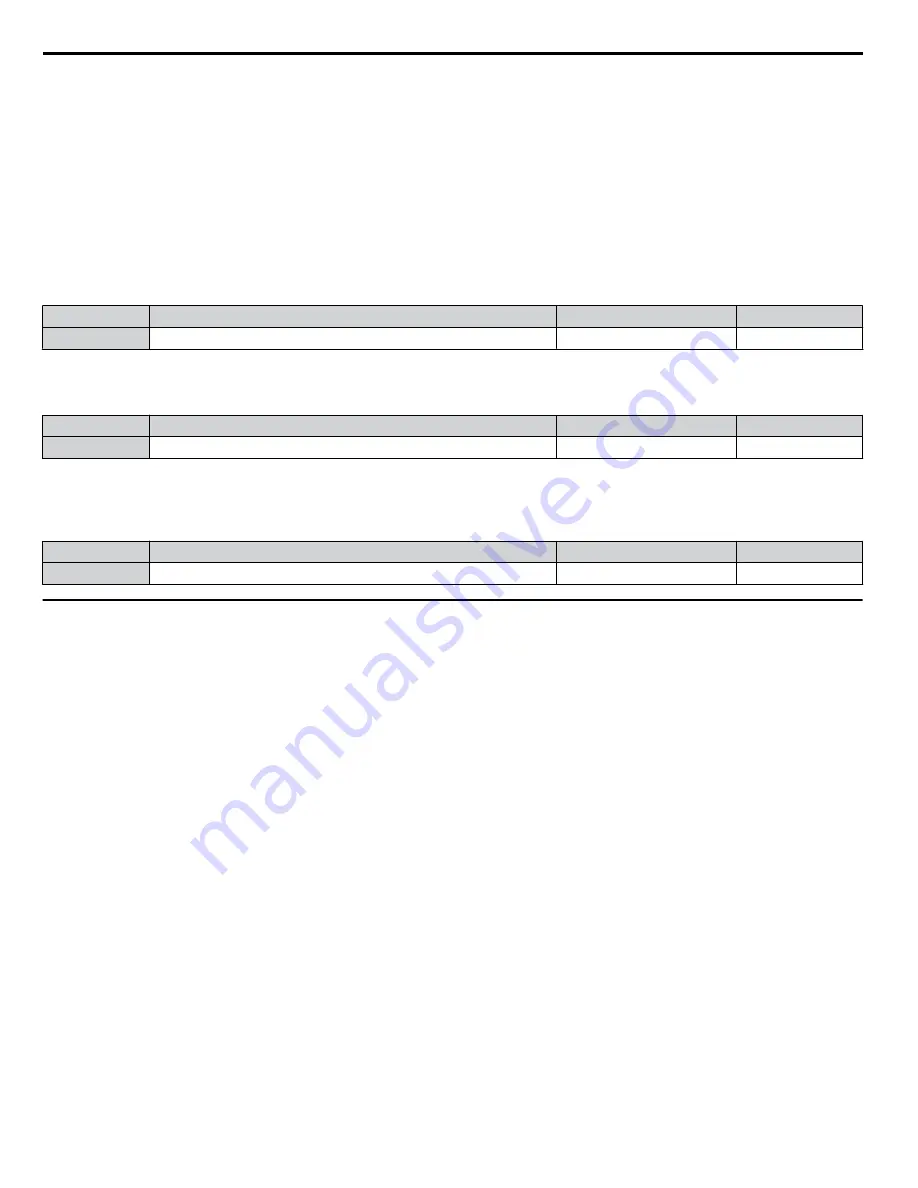
Setting 6: Continue Running if the Speed Is Less than L6-09 (Alarm)
Detection when the speed is below L6-09 (unsigned). Operation continues and triggers a UL5 alarm after detection.
Setting 7: Stop when Motor Speed Is Less than L6-09 (Signed)
Detection when the speed is below L6-09 (signed). Operation stops and triggers a UL5 fault after detection.
Setting 8: Stop when Motor Speed Is Less than L6-09
Detection when the speed is below L6-09 (unsigned). Operation stops and triggers a UL5 fault after detection.
n
L6-09: Mechanical Weakening Detection Speed Level
Sets the speed level for Mechanical Weakening Detection as a percentage of the maximum frequency. If L6-08 is set for
unsigned speed detection (L6-08 = 2, 4, 6, 8), the absolute value of L6-09 is used (negative settings are treated as positive
values).
No.
Name
Setting Range
Default
L6-09
Mechanical Weakening Detection Speed Level
-110.0 to 110.0%
110%
n
L6-10: Mechanical Weakening Detection Time
Sets the time permitted for the situation selected in parameter L6-08 to arise before detecting mechanical weakening.
No.
Name
Setting Range
Default
L6-10
Mechanical Weakening Detection Time
0.0 to 10.0 s
0.1 s
n
L6-11: Mechanical Weakening Detection Start Time
Sets the cumulative drive operation time at which Mechanical Weakening Detection is activated. The function activates when
U4-01 reaches the L6-11 value.
No.
Name
Setting Range
Default
L6-11
Mechanical Weakening Detection Start Time
0 to 65535 h
0 h
u
L7: Torque Limit
The torque limit function limits the torque in each of the four quadrants individually to protect machinery in OLV, CLV,
AOLV/PM, and CLV/PM control modes. Set the limit through parameters, analog inputs, or by switching a digital output
programmed for “During torque limit” (H2-01, H2-02, H2-03 = 30) when the drive is operating at the torque limit.
n
Setting Torque Limits
Parameters L7-01 to L7-04 define the torque limits for each of the four operation quadrants. it is also possible to use Analog
inputs to define a general limit for all operation conditions (H3-02, H3-06, H3-10 = 15) or to set separate limits for each
operation condition (H3-02, H3-06, H3-10 = 10, 11, or 12).
shows limit setting is applied in each quadrant.
If two limit values are defined for the same operation conditions, the drive will use the lower value.
Note:
The maximum output torque is ultimately limited by the drive output current (max. 150% of drive rated current in HD, 120% in ND). Output
torque will not exceed the drive rated current limit even if the torque limits are set to higher values.
Example: If parameter L7-01 = 130%, L7-02 to L7-04 = 200%, and an analog input sets a general torque limit of 150% (H3-02,
H3-06, H3-10 = 15), then the torque limit will be 130% in quadrant 1, but 150% in the other quadrants.
5.8 L: Protection Functions
326
YASKAWA ELECTRIC SIEP C710636 04D U1000 Industrial MATRIX Drive Technical Manual
Содержание U1000 iQpump Drive
Страница 705: ......