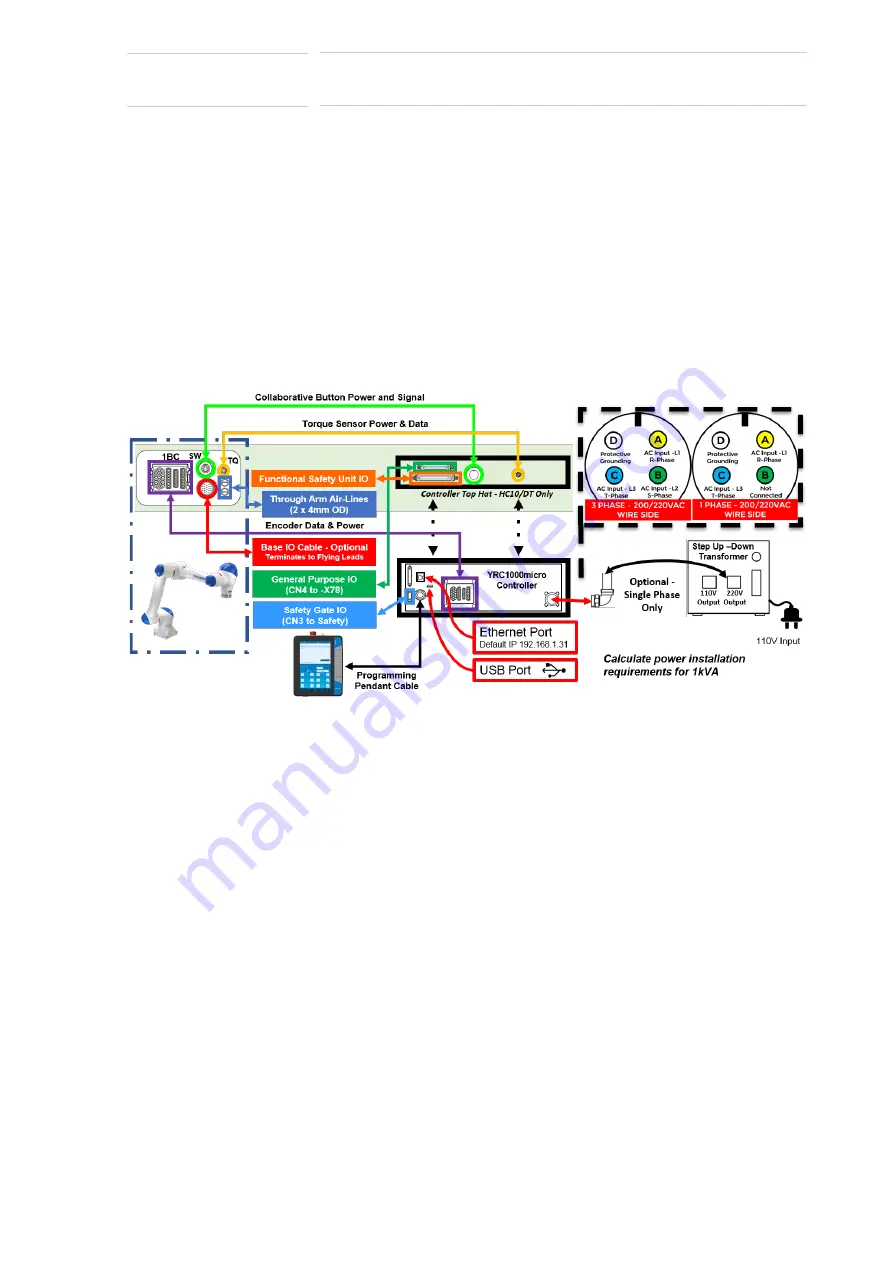
2-4
188791-1
188791-1
2
Setup HC10DT Smart Series Robot
2.4 Wiring Robot
Smart Series HC10DT
Collaborative Robot
2.4 Wiring Robot
2.4.1 Reference Material
Refer to the following manuals for detailed wiring instructions:
–
READ FIRST!! YRC1000micro GPIO and Direct IN Connections
–
Section 1.5.2 Connecting to the YRC1000micro of the YRC1000/
YRC1000micro INSTRUCTIONS FOR Smart Pendant
–
Chapter 2 Connections of the YRC1000micro SUPPLEMENTARY
–
Chapter 4 Wiring of the MOTOMAN-HC10DT INSTRUCTIONS
2.4.2 Basic Wiring Overview
Fig. 2
-
4: Basic Wiring