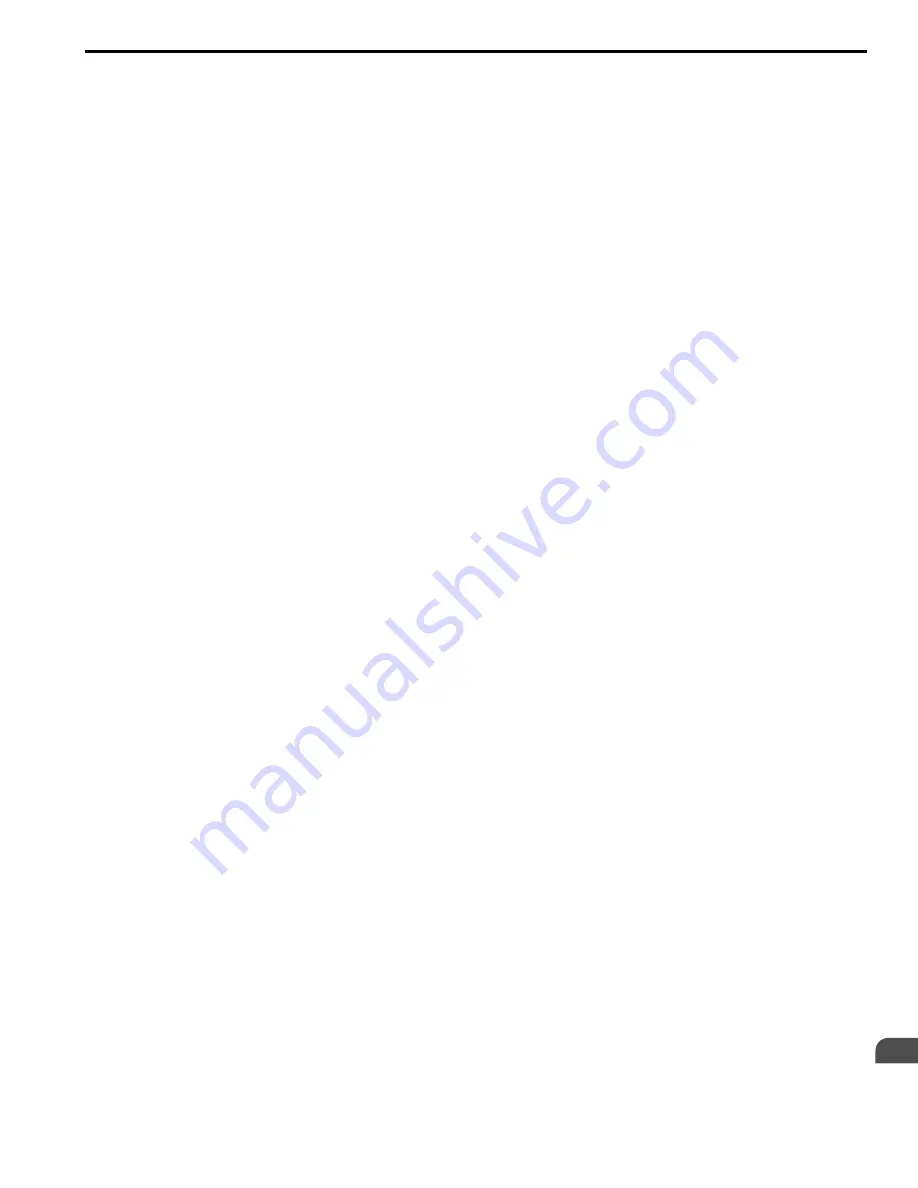
YASKAWA
TOEPYAIGA8001B GA800 Drive Maintenance & Troubleshooting
497
Note:
•
If you cannot operate the motor with the conditions in step 2 for the first test run and if the values set in
E2-02
and
E2-03
are much different
than data in the official test report for the motor and the data listed in
Defaults by Drive Model and Duty Rating ND/HD on page 282
, these
problems can occur:
–
Motor vibrations or hunting
–
Not sufficient torque
–
Overcurrent
In elevator applications, there is a risk of the cage falling and causing personal injury.
Do one of these precautions to decrease the risk:
–
After doing Stationary Auto-Tuning, operate the drive as specified by the conditions and procedure above.
–
Set
T1-12 = 0 [Test Mode Selection = No]
.
–
Do Rotational Auto-Tuning.
•
If you initialize the drive after completing Step 1, do the procedure beginning from Step 1 again.
•
For general-purpose motors, the target value for
E2-02
is 1 Hz to 3 Hz, and the target rated current for
E2-03
is 30% to 65%. Larger
capacity motors have a lower rated slip, and a smaller ratio for the no-load current rated current. Refer to
Defaults by Drive Model and Duty
■
Precautions before Stationary Auto-Tuning for Line-to-Line Resistance and Stator
Resistance Auto-Tuning
In V/f control, when the motor cable is 50 meters (164 feet) or longer, do Stationary Auto-Tuning for Line-to-Line
Resistance.
WARNING!
Electrical Shock Hazard. During Auto-Tuning, the motor will receive high voltage when the motor is stopped. Do not
touch the motor until Auto-Tuning is complete. If you touch a motor that is energized, it can cause serious injury or death.
■
Precautions before Inertia Tuning and ASR Tuning
Before Inertia Tuning or ASR Tuning, check these items:
WARNING!
Electrical Shock Hazard. During Auto-Tuning, the motor will receive high voltage when the motor is stopped. Do not
touch the motor until Auto-Tuning is complete. If you touch a motor that is energized, it can cause serious injury or death.
•
Do rotational motor parameter tuning or look at the motor test report or nameplate to enter the values manually.
•
Make sure that the motor magnetic brake is released.
•
Connect the motor and load.
•
Make sure that external force from the machine will not cause the motor to rotate.
•
Make sure that the machine does not prevent reverse rotation. You cannot do Inertia Tuning or ASR Tuning with
machines that prevent reverse rotation.
•
When the motor can rotate during Auto-Tuning, check for safety issues near the drive, motor, and machine.
Note:
If there are gears between the machine and motor shaft, Inertia Tuning or ASR Tuning are possibly not applicable.
■
Precautions before Using Deceleration Rate Tuning and KEB Tuning
Before Deceleration Rate Tuning or KEB Tuning, check these items:
Note:
•
Do not do Deceleration Rate Tuning if you use a braking resistor unit or a regenerative converter.
•
Do Deceleration Rate Tuning and KEB Tuning with the load attached to the motor.
•
Do not do Deceleration Rate Tuning or KEB Tuning for these applications:
In Deceleration Rate Tuning and KEB Tuning, the drive will automatically rotate the motor forward and accelerate and decelerate the motor
again and again.
–
On a machine that does not let the motor rotate forward
–
In applications with a small range of operation (trolleys and other such applications that can only move linearly)
–
Applications where sudden acceleration and sudden deceleration are not applicable.
•
To do KEB Tuning with the external main circuit capacitors connected to the drive, set
L3-26 [Additional DC Bus Capacitors]
then do KEB
Tuning.
•
Do not do KEB Tuning or Deceleration Rate Tuning if the drive is set to use
H1-xx = 16 [MFDI Function Select = Motor 2 Selection]
.
Failure to obey can cause an
ov [Overvoltage]
fault.
Содержание GA800 Series
Страница 2: ...This Page Intentionally Blank 2 YASKAWA TOEPYAIGA8001B GA800 Drive Maintenance Troubleshooting...
Страница 18: ...i 2 Using the Product Safely 18 YASKAWA TOEPYAIGA8001B GA800 Drive Maintenance Troubleshooting...
Страница 72: ...1 7 Storage Guidelines 72 YASKAWA TOEPYAIGA8001B GA800 Drive Maintenance Troubleshooting...
Страница 336: ...4 10 Installation Methods 336 YASKAWA TOEPYAIGA8001B GA800 Drive Maintenance Troubleshooting...
Страница 430: ...5 18 Motor Application Precautions 430 YASKAWA TOEPYAIGA8001B GA800 Drive Maintenance Troubleshooting...
Страница 565: ...YASKAWA TOEPYAIGA8001B GA800 Drive Maintenance Troubleshooting 565...