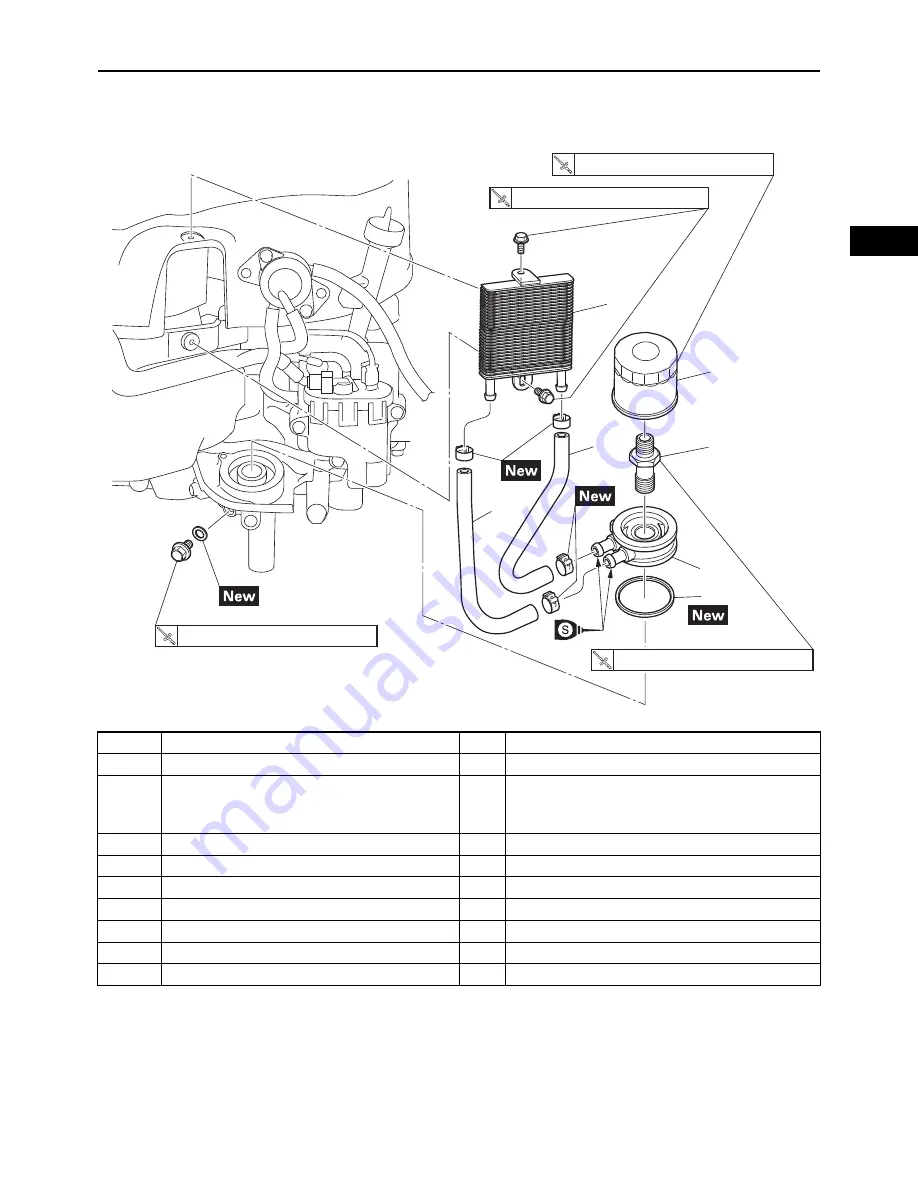
3-5
1
2
3
4
5
6
7
8
9
10
ENGINE
OIL COOLER
OIL COOLER
Order
Job/Parts to remove
Q’ty
Remarks
Removing the oil cooler
Remove the parts in the order listed.
Engine oil
Drain.
Refer to “REPLACING THE ENGINE OIL” on
page 2-6.
1
Oil cooler
1
2
Oil hose 1
1
3
Oil hose 2
1
4
Oil filter
1
5
Adapter union bolt
1
6
Adapter
1
7
Oil seal
1
17 N
・
m (1.7 kgf
・
m, 12 lb
・
ft)
14 N
・
m (1.4 kgf
・
m, 10 lb
・
ft)
9 N
・
m (0.9 kgf
・
m, 6.5 lb
・
ft)
62 N
・
m (6.2 kgf
・
m, 45 lb
・
ft)
1
2
3
4
5
6
7
Содержание MX775
Страница 2: ...7UD F8197 E0_Cover indd 2 2016 12 13 11 23 58 ...
Страница 8: ...MEMO ...
Страница 24: ...SPECIAL TOOLS AND TESTERS 1 12 1 2 3 4 5 6 7 8 9 10 GENERAL INFORMATION MEMO ...
Страница 101: ...4 5 1 2 3 4 5 6 7 8 9 10 FUEL FUEL PUMPS sure fuel pump joint until a distinct click is heard ...
Страница 136: ...5 25 1 2 3 4 5 6 7 8 9 10 ELECTRICAL ELECTRICAL COMPONENTS ELECTRICAL COMPONENTS 1 2 2 3 4 5 6 6 7 8 9 10 11 12 13 14 ...
Страница 170: ...7 12 1 2 3 4 5 6 7 8 9 10 SPECIFICATIONS WIRE ROUTING DIAGRAM WIRE ROUTING DIAGRAM UPPER SIDE VIEW ...
Страница 172: ...7 14 1 2 3 4 5 6 7 8 9 10 SPECIFICATIONS WIRE ROUTING DIAGRAM ...
Страница 174: ...7 16 1 2 3 4 5 6 7 8 9 10 SPECIFICATIONS WIRE ROUTING DIAGRAM LEFT SIDE VIEW ...
Страница 176: ...7 18 1 2 3 4 5 6 7 8 9 10 SPECIFICATIONS WIRE ROUTING DIAGRAM RIGHT SIDE VIEW ...
Страница 180: ...7 22 1 2 3 4 5 6 7 8 9 10 SPECIFICATIONS WIRE ROUTING DIAGRAM REAR SIDE VIEW ...
Страница 183: ...7 25 1 2 3 4 5 6 7 8 9 10 SPECIFICATIONS WIRE ROUTING DIAGRAM MEMO ...
Страница 186: ...MEMO ...
Страница 187: ...7UD F8197 E0_Cover indd 2 2016 12 13 11 23 58 ...
Страница 188: ...SERVICE MANUAL MX775 MX800 MX825 7UD F8197 E0 LIT 19616 02 37 2016 12 1 7UD F8197 E0_Cover indd 1 2016 12 13 11 23 58 ...