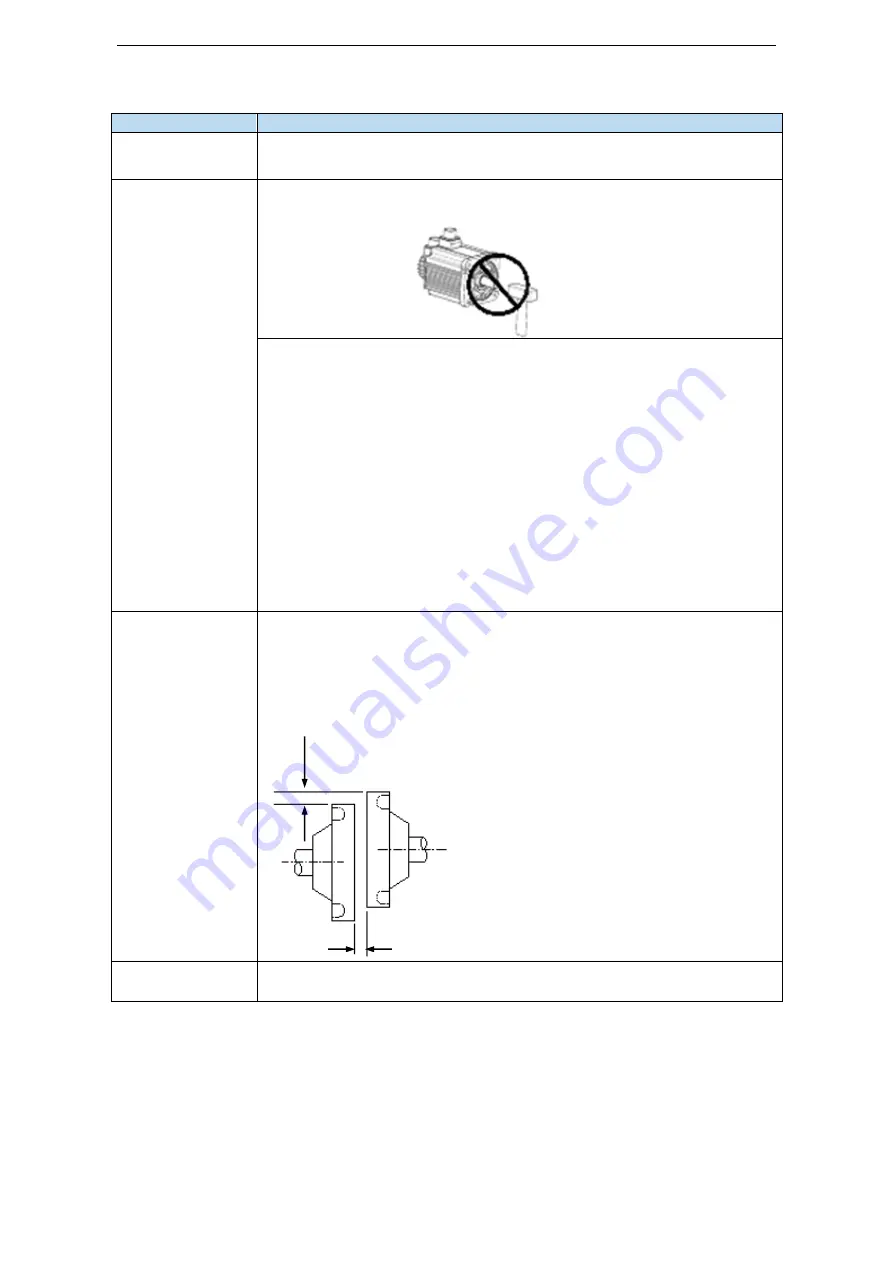
19
2.2.2 Installation cautions
Item
Description
Antirust treatment
◆
Before installation, please wipe the "rust-proof agent" of the extension end
of the servo motor shaft, and then do the relevant rust-proof treatment.
Encoder cautions
◆
It is forbidden to impact the extension end of the shaft during installation,
otherwise the internal encoder will be broken.
◆
When the pulley is installed on the servo motor shaft with keyway, the
screw hole is used at the end of the shaft. In order to install the pulley, the
double-headed nails are inserted into the screw holes of the shaft, the washer is
used on the surface of the coupling end, and the pulley is gradually locked with
the nut.
◆
For the servo motor shaft with keyway, use the screw hole at the end of the
shaft to install. For shaft without keyway, friction coupling or similar methods
are used.
◆
When the pulley is dismantled, the pulley mover is used to prevent the
bearing from being strongly impacted by the load.
◆
To ensure safety, protective covers or similar devices, such as pulleys
installed on shaft, are installed in the rotating area.
Centering
◆
When installing the servo motor, make it conform to the centering accuracy
requirement shown in the picture below. If the centering is inadequate, vibration
will occur, and sometimes the bearing and encoder may be damaged. When
installing the coupling, please do not directly impact the motor shaft, otherwise
the encoder installed on the opposite side of the load shaft will be damaged.
Installation
direction
◆
Servo motor can be installed in horizontal or vertical direction.
The maximum and minimum deviations are
less than 0.03mm (rotated with the coupling)
measured at four locations in a circle.
The maximum and minimum deviations are less than 0.03mm
(rotated with the coupling) measured at four locations in a circle.
Содержание DS5F Series
Страница 1: ...DS5F series servo driver User manual WUXI XINJE ELECTRIC CO LTD Data No SC5 02 20200217 2 3 ...
Страница 2: ......
Страница 41: ...39 3 2 5 Encoder feedback output signal Servo driver differential to collector upper device ...
Страница 124: ...122 2 select jog setting or manual setting to configure the inertia estimation trip 3 Set the auto tuning interface ...
Страница 202: ...200 Appendix 9 Torque speed characteristic curve ...
Страница 203: ...201 ...
Страница 204: ...202 ...