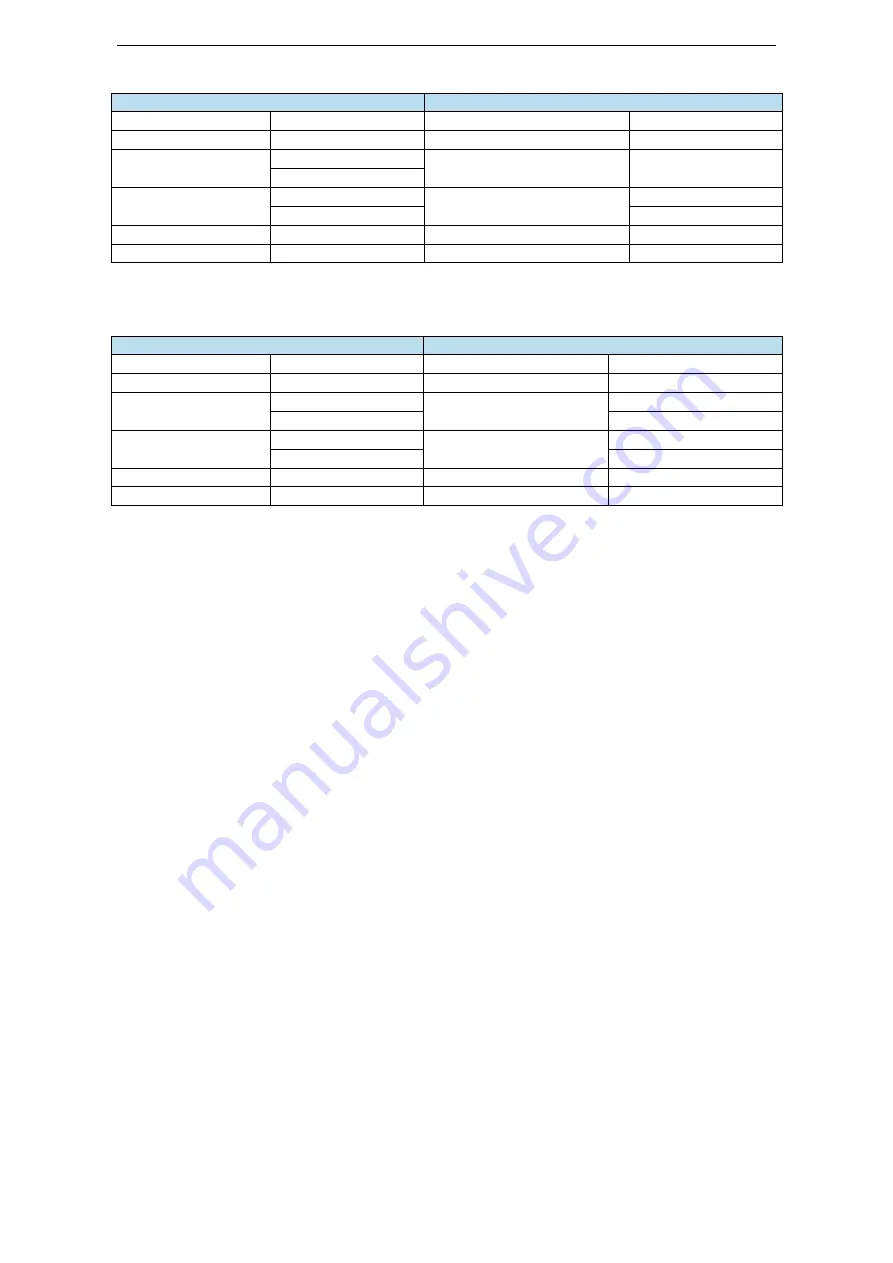
166
RTU mode:
Inquiry information format
Response message format
Address
01H
Address
01H
Function code
03H
Function code
03H
register address
10H
Byte quantity
02H
05H
register quantity
00H
Data content
01H
01H
34H
CRC CHECK Low
90H
CRC CHECK Low
B8H
CRC CHECK High
CBH
CRC CHECK High
03H
Function code06H: write the data in the register
For example: write 300 rpm to the address of P3-18 register of inching speed.
RTU mode:
Inquiry information format
Response message format
Address
01H
Address
01H
Function code
06H
Function code
06H
register address
03H
register address
03H
12H
12H
Data content
01H
Data content
01H
2CH
2CH
CRC CHECK Low
29H
CRC CHECK Low
29H
CRC CHECK High
C6H
CRC CHECK High
C6H
4. Parity code
RTU mode: double byte hexadecimal number.
The CRC field is a two-byte, 16-bit binary value. It is calculated by the sender and added to the
message; when it is added, it is first the low byte and then the high byte, so the high byte of CRC is the
last byte of the sent message. The receiving device recalculates the CRC of the received message and
compares it with the value in the received CRC field. If the two values are different, there is an error in
the received message, discards the message frame, makes no response, and continues to receive the
data of the next frame. Refer to the description of Modbus protocol for CRC verification calculation
method.
8.4 Communication example
8.4.1 Communication with Xinje PLC
Xinje PLC communicates with Xinje two drivers through 485, reads the speed of motor and writes
the torque limit of motor.
1. Hardware wiring: if the customer uses AB terminal of Xinje PLC for 485 communication, just
connect the 14 and 15 pins of the driver to AB terminal of PLC.
2. Parameter setting: the communication parameters of the driver and PLC are set in the same way,
such as baud rate, parity, data bit, slave station, etc. the communication protocols of the Xinje PLC and
servo are standard Modbus RTU, namely 19200bps, 1-8-1-even parity.
The setting parameters are as follows:
P7-00 Station No. 1, 2
P7-01.0 ~ 1 baud rate 06
P7-01.2 stop bit 2
P7-01.3 check bit 2
Note: if the communication parameter settings of the upper computer and the lower computer are
inconsistent, the communication will fail.
3. Software program: the register in which the station number, communication address and
contents are marked when writing instructions.
(1) Station number: the value set for servo driver P7-00. K1 indicates that P7-00 is set to 1; K2
indicates that P7-00 is set to 2.
Содержание DS5F Series
Страница 1: ...DS5F series servo driver User manual WUXI XINJE ELECTRIC CO LTD Data No SC5 02 20200217 2 3 ...
Страница 2: ......
Страница 41: ...39 3 2 5 Encoder feedback output signal Servo driver differential to collector upper device ...
Страница 124: ...122 2 select jog setting or manual setting to configure the inertia estimation trip 3 Set the auto tuning interface ...
Страница 202: ...200 Appendix 9 Torque speed characteristic curve ...
Страница 203: ...201 ...
Страница 204: ...202 ...