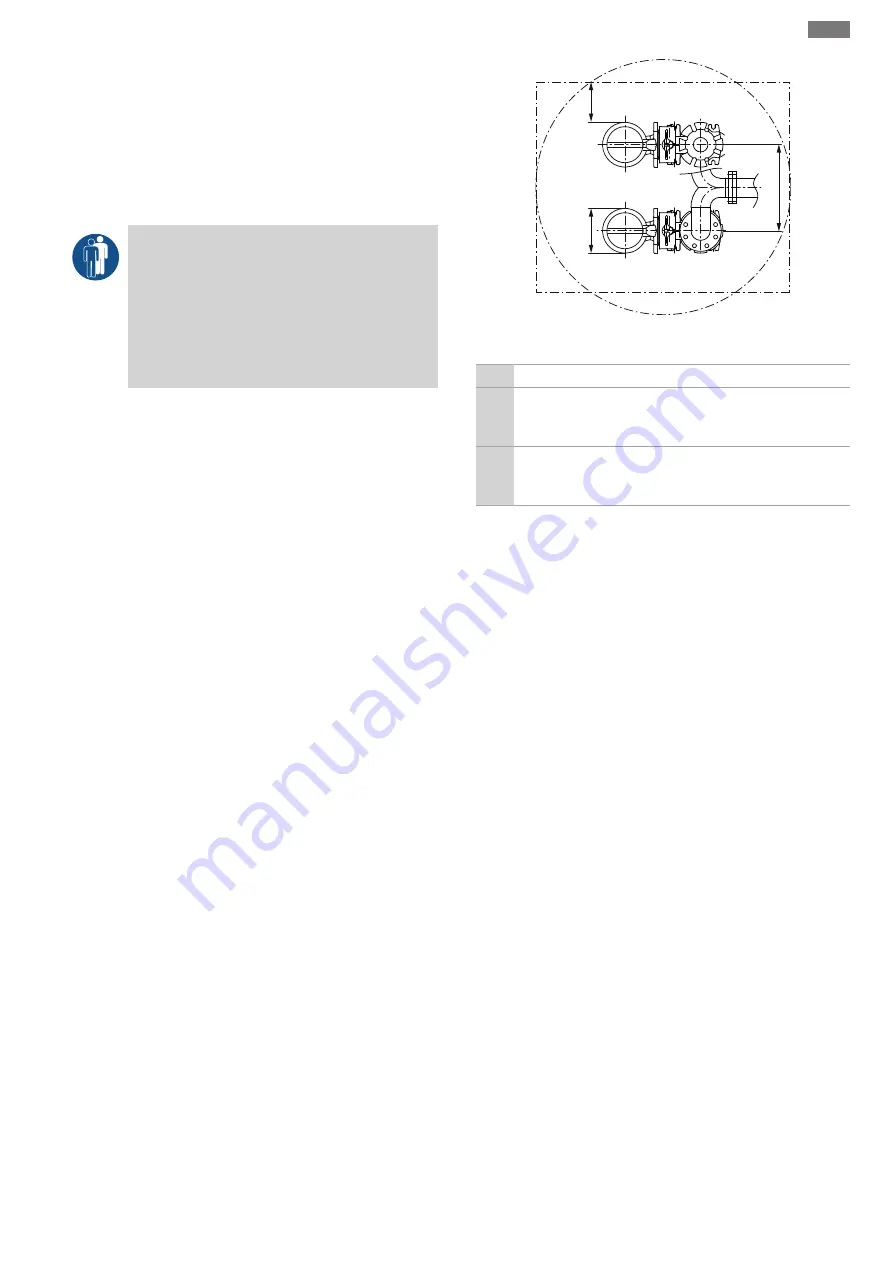
en
Installation and operating instructions • Wilo-Rexa FIT-S • Ed.01/2022-03
11
•
Structural components and foundations must be of sufficient
stability in order to allow the device to be fixed in a secure and
functional manner. The operator is responsible for the provision
and suitability of the structural component/foundation!
•
Check that the available consulting documents (installation
plans, installation location, inflow conditions) are complete and
accurate.
6.4
Installation
DANGER
Risk of fatal injury due to dangerous lone
working practices!
Work in chambers and narrow rooms as well as work
involving risk of falling are dangerous work. Such
work may not be carried out autonomously!
• Only carry out work with another person!
•
Wear protective equipment! Observe the work regulations.
–
Protective gloves: 4X42C (uvex C500 wet)
–
Safety shoes: Protection class S1 (uvex 1 sport S1)
–
Safety helmet: EN 397 Conforms to standards, protection
against lateral deformation (uvex pheos)
(When using lifting equipment)
•
Prepare the installation site:
–
Clean, free of coarse solids
–
Dry
–
Frost-free
–
Disinfected
•
Toxic or asphyxiating gases may build up during work:
–
Observe protective measures in accordance with work regu-
lations (gas measurement, carry a gas detector with you).
–
Ensure adequate ventilation.
–
If toxic or asphyxiating gases accumulate, leave the work-
place immediately!
•
Always carry the pump by the handle!
•
Install lifting equipment: even surface, clean, firm base. Ware-
house and installation location must be easily accessible.
•
Attach chain or wire rope to handle/attachment point with a
shackle. Only use lifting gear that has been technically ap-
proved.
•
All connection cables must be laid properly. The connection
cables must not pose any risk (i.e. tripping, damage during op-
eration). Check whether the cable cross-section and the cable
length are sufficient for the selected installation type.
•
Installation of switchgear: Observe information in the manufac-
turer’s instructions (IP class, overflow-proof, potentially explos-
ive atmospheres)!
•
Avoid air intake into the fluid. Use baffles or deflector plates at
the inlet. Install the ventilation systems!
•
Do not allow the pump to run dry! Avoid air pockets. Do not go
below the minimum water level. Installation of dry-running pro-
tection is recommended!
6.4.1
Indications for double pump operation
If several pumps are used in an operating space, minimum dis-
tances between the pumps and the wall must be complied with.
Here there is a difference in the distances depending on the type
of system: Alternating operation or parallel operation.
d
A
2
A
1
Fig. 3:
Minimum distances
d
Diameter hydraulics housing
A
1
Minimum distance from the wall:
- alternating operation: min. 0.3 × d
- parallel operation: min. 1 × d
A
2
Distance to pressure pipes
- alternating operation: min. 1.5 × d
- parallel operation: min. 2 × d
6.4.2
Maintenance tasks
After a storage period of more than 12 months, carry out the fol-
lowing maintenance tasks before installation:
•
Check the oil in the sealing chamber and replace it if necessary.
See section “Oil change in sealing chamber [
19]”.
6.4.3
Stationary wet well installation
The pump is installed in a pump chamber or basin. A suspension
unit is installed to connect the pump to the pressure pipe. The on-
site pressure pipe is connected to the suspension unit. The pump is
connected to the suspension unit via a coupling connection.
The pressure pipe must meet the following requirements:
•
The connected pressure pipe is self-supporting. The pressure
pipe must
not
be supported by the suspension unit!
•
The pressure pipe must not be smaller than the pump’s dis-
charge connection.
•
All prescribed valves (gate valves, backflow preventers …) are
present.
•
Pressure pipe laid frost-proof.
•
Ventilation systems (e.g. air vent valves) installed. Air pockets in
the pump and in the pressure pipe can lead to delivery prob-
lems.