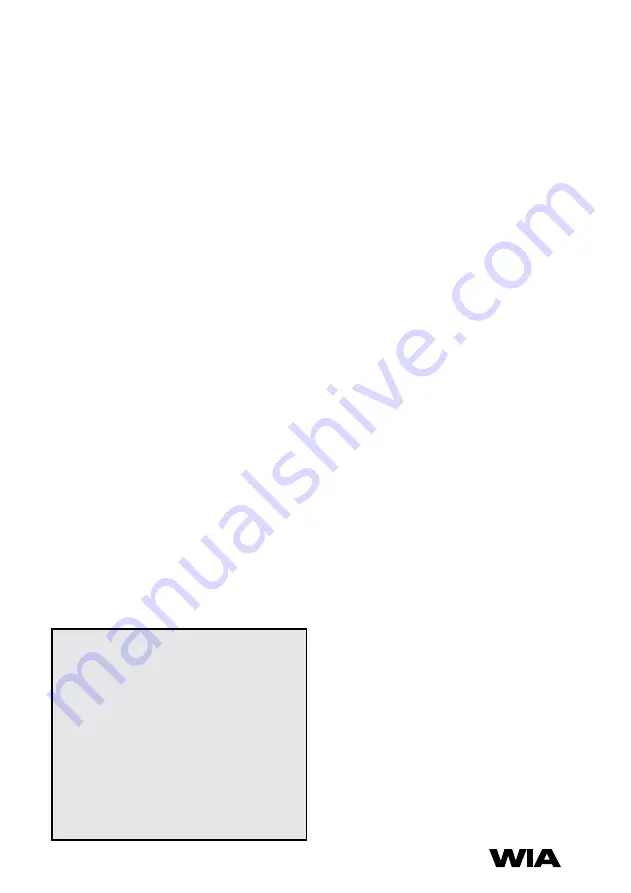
11
10
5 INSTALLATION
Remote Wirefeeder
The remote wirefeeder is connected to the
Weldmatic power source via the composite
cable interconnecting lead. Check all
connections are firmly made to ensure good
electrical contact, and to prevent gas leaks.
Fitting The Gun and Cable Assembly
The supplied welding gun/cable assembly
is equipped with a ‘Euro’ wirefeeder
connector which incorporates all required
connection points for welding current,
shielding gas and gun switch control.
To attach the gun/cable assembly to
the wirefeeder mechanism, engage the
mating parts of the male and female Euro
connectors, then rotate the locking ring
clockwise to firmly secure the connection.
Fitting the Consumable Wire
Place the spool of welding wire onto the
spool holder. The location pin should mate
with a hole provided on the wire spool body.
Secure the spool with plastic nut. Check
the adjustment of the spool brake, which
should be set to prevent over run of the wire
spool at the end of a weld, without unduly
loading the wirefeed motor. The braking can
be adjusted by using an allen key to adjust
Hex head bolt inside the hub.
The quality of the consumable wire
greatly affects how reliably a gas
metal arc welder will operate. For
best results when welding mild
steel, we recommend quality WIA
AUSTMIG ES6. Dirty, rusty or kinked
wire will not feed smoothly through
the gun cable and will cause erratic
welding. Deposits from the wire will
clog the gun cable liner requiring it
to be replaced prematurely.
Feeding the Consumable Wire
At the wirefeeder, release the compression
screw and rotate the top roller arms to
the open position. The end of the welding
wire can now be passed through the inlet
guide, over the first lower roller, through
the intermediate guide, over the second
lower roller and into the output wire guide
tube. Check that the drive roll grooves are
correct for the wire in use. The appropriate
size is stamped on the visible side of the
installed rollers. Check also that the correct
size contact tip is fitted at the gun end.
Feed roller and tip details are shown in
Section 10 of this manual.
Return the top roller arms to the closed
position and adjust the compression screw
to provide sufficient clamping of the drive
rollers to achieve constant wirefeed. Do not
over tighten.
With the equipment energised, operate
the gun switch to feed wire through the
gun cable.
Содержание W67-1
Страница 1: ...Wirefeeder WELDING COM AU OPERATORS MANUAL W67 1 From serial numbers W67A...
Страница 15: ...15 Fig 3 Wirefeeder Assemble and Parts List 11 1 ASSEMBLY AND PARTS LIST W67 WIREFEEDER...
Страница 26: ...26 Wirefeeder W67 Operator Manual Model No W67 40 NOTES...
Страница 27: ...27 NOTES...