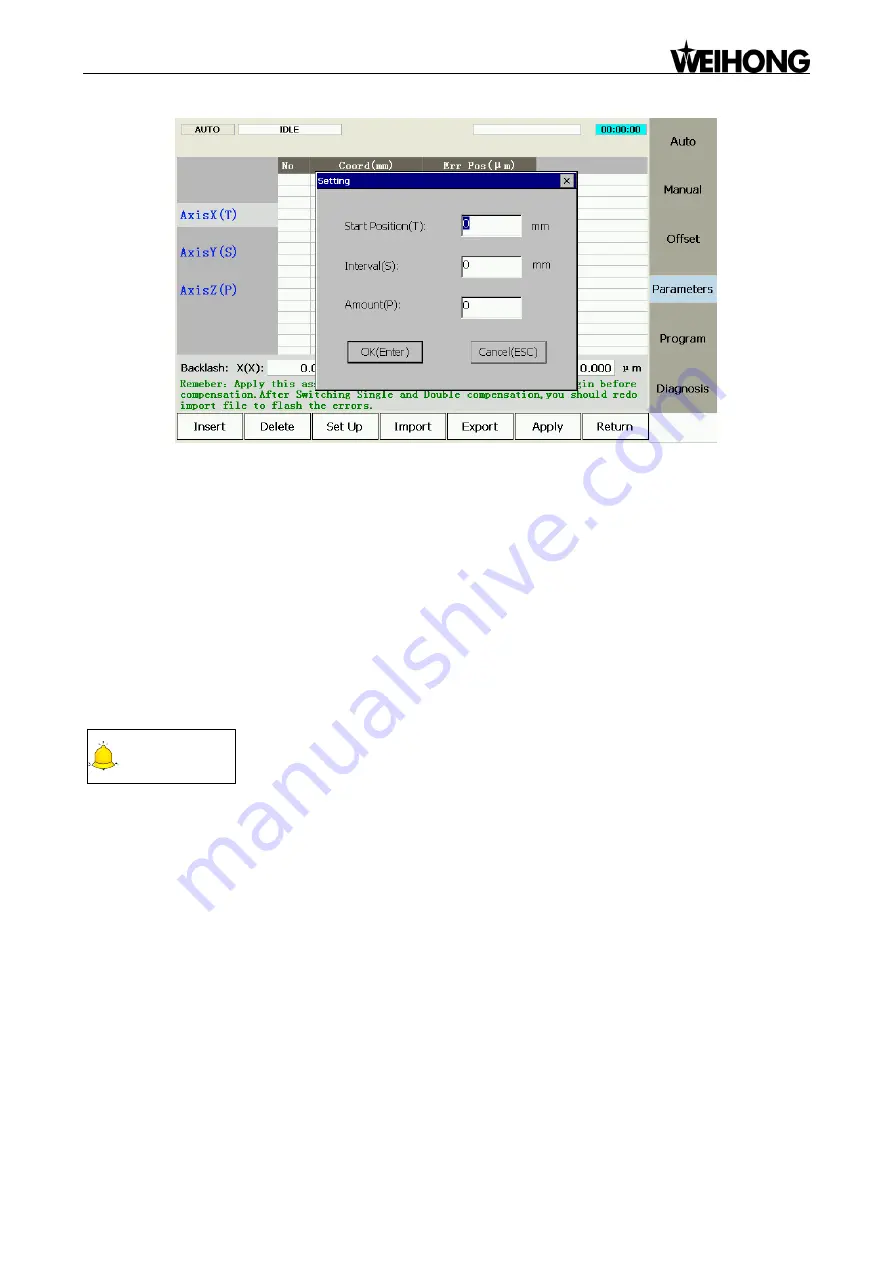
Specialized Concentrated Focused
Operation
「
55
」
Fig. 3-40 Setup Dialog Box
Import & Export
Compensation files can be copied from or to a U disk or other external storage.
Apply
After parameters are set, press Apply before restarting the software. Reboot is needed to validate the
modification of backlash data. If the system is not rebooted, the modified value does not take effect,
while it is the previous backlash data that still works.
Return
To return to the previous page, namely the [Parameter] function section.
CAUTION
1)
The compensation data can be in an ascending or descending order. Positive interval indicates ascending order
while negative interval descending order.
2)
Backlash can only be set in unilateral compensation, and hidden in bilateral compensation.
3)
Remember to press the Apply button after modification of screw error compensation data. Before machining,
homing should be executed, because the system only sends the compensation data of the homed axes to the
driver.
4)
After switchover between unilateral compensation and bilateral compensation, it is necessary to load the
desired file again and apply it. Otherwise, it is the previous compensation mode and data before modification
that still work.
3.11.2 Tool Compensation
In CNC machining, the CNC system actually controls tool center or the related point of tool rest whose
motion track is controlled directly to indirectly realize the profile processing for the actual parts.