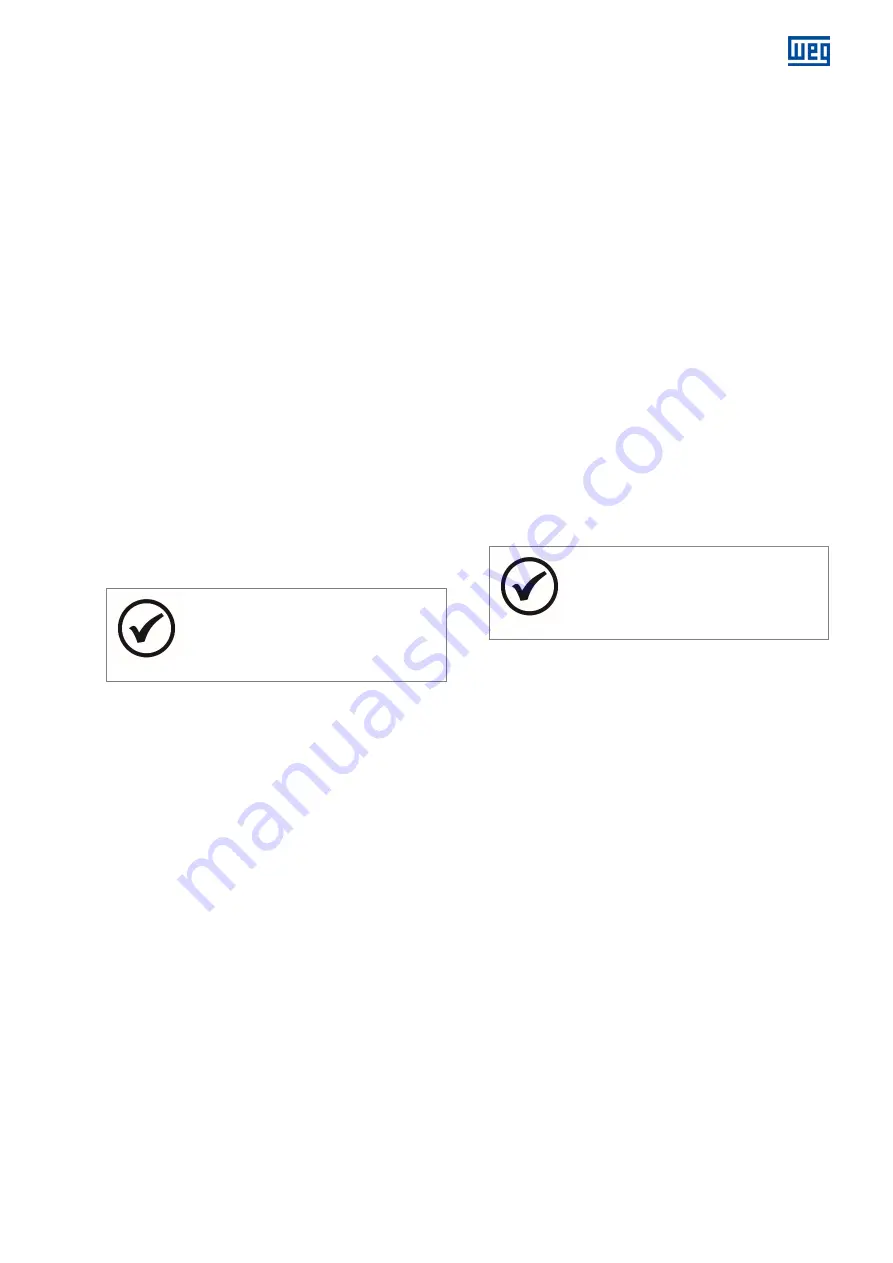
11239449 Installation, operation and maintenance manual – Squirrel cage motor – W Line - Horizontal and vertical l 33
5
STARTING
5.1
DIRECT ON-LINE STARTING
It is the simplest and most economically feasible method;
however, it must only be used when the starting current
does not affect the power grid.
Bear in mind that the starting current of motors may reach
6 to 7 times the rated current value. Therefore, it must be
ensured that this current (Ip) will not affect the supply of
other consumers because of the high voltage drop in the
power grid.
This requirement is met in one of the three situations:
a)
When the power grid is
"strong"
enough and the
motor current is negligible in relation to the grid
capacity.
b)
The motor is always started without load, which
reduces the starting time and, in turn, the duration of
the starting current and the momentary voltage drop,
which is acceptable for the other consumers of the
grid;
c)
When DOL starting is duly authorized by the local
electric utility company.
When the motor starting current is high, the following
detrimental consequences may occur:
a)
The high voltage drop in the power supply system may
cause interference in equipment installed in this
system;
b)
The protection system (cables, contactors) must be
oversized, increasing the installation costs.
NOTE
In some cases, there is an imposition of the
electric utility companies that limits the
voltage drop of the grid.
5.2
DIRECT ONLINE STARTING
FREQUENCY
Since induction motors have a high starting current, the
time spent to accelerate loads with high inertia results in a
quick rise of the motor temperature. If the intervals
between successive starts are too short, the temperature
of the windings will rise quickly, reducing their useful life or
even burning them. The NBR 17094 and IEC60034-1
standards establishes a minimum starting duty to which
the motors must be able to comply:
a)
Two successive starts: the first one with the motor
cold, i.e., with its windings at ambient temperature,
and the second one right afterwards, but only after
the motor has decelerated to a full stop;
b)
One start with the motor hot, i.e., with the windings at
continuous duty temperature.
The first condition simulates the case in which the first
motor start is aborted, for instance, by the trip of the
motor protection, when a second motor start is permitted
right afterwards.
The second condition simulates the case of an accidental
motor shutdown under normal operation, for instance, by
power outage, when the motor restart is allowed right after
the power is reestablished.
NOTE
Special starting conditions must be checked
in the specific motor documentation before
starting the procedure.
5.3
LOCKED ROTOR CURRENT
The motor nameplate indicates the value of I
P
/I
n
, which is
the relation between the starting current and the rated
current of the motor.
5.4
STARTING WITH REDUCED
CURRENT
If direct online starting is not possible, the following
starting systems can be used in order to reduce the motor
starting current.
Star-delta starter;
Series-parallel starter;
Autotransformer starter;
Static starter or soft-starter;
Frequency inverter.