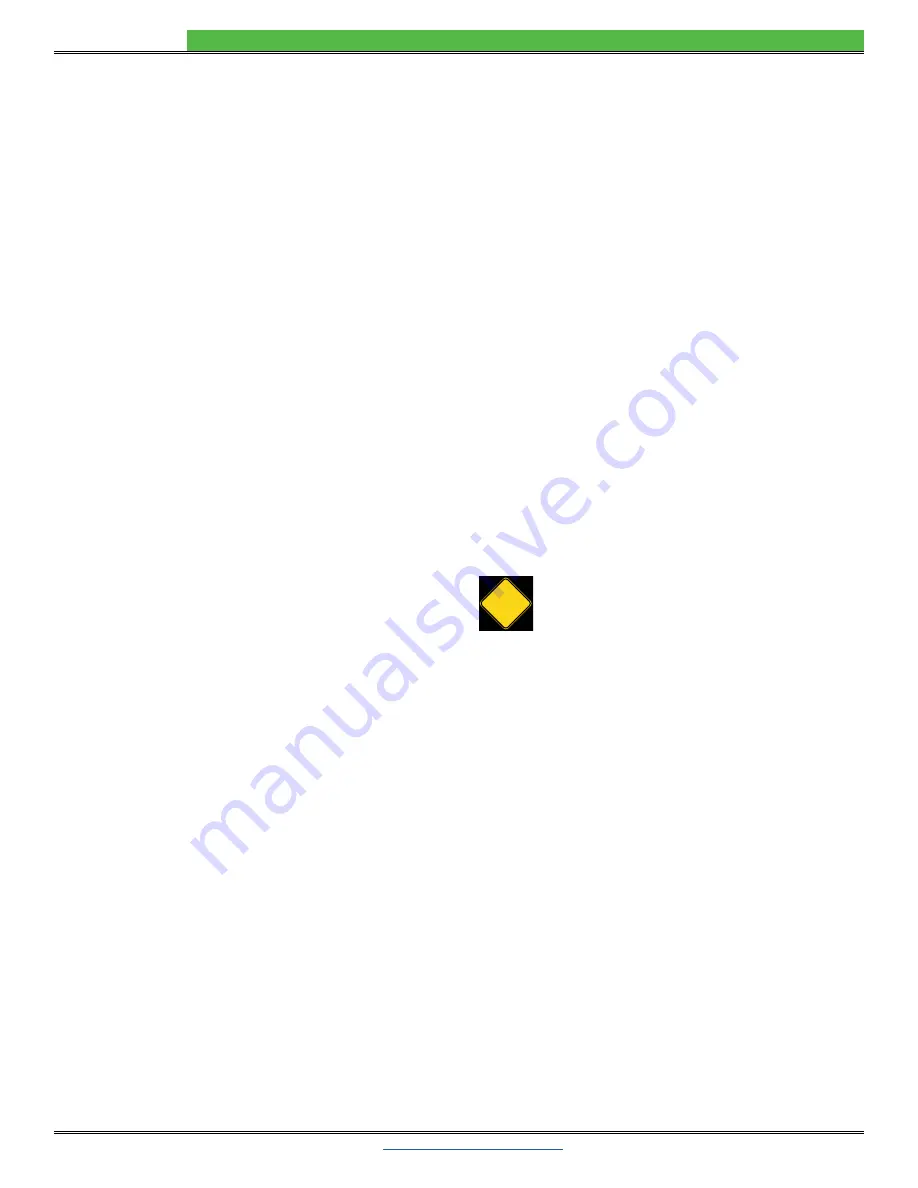
© 2018
9
LDTC0520 / LDTC1020 LASER DIODE AND TEMPERATURE CONTROLLER
The controller measures the load temperature by driving a
current through the temperature sensor and measuring the
voltage drop across it. Similarly to the laser driver, you do
not directly adjust the setpoint on the temperature controller;
rather, you adjust a voltage signal that represents the sensor
voltage at the desired temperature setpoint. The controller
continuously compares the setpoint voltage and the actual
sensor voltage. If there is a difference between the two
signals the controller adjusts the output current—thereby
driving the TEC or heater to change temperature—until the
difference is zero.
Once the actual sensor voltage equals the setpoint voltage,
the controller makes minor adjustments to the output current
in order to keep the difference at zero.
The controller includes features that help protect the load
from damage, and also make it more versatile in a wide
array of applications.
• Independent heating and cooling current limits to protect
from thermal runaway situations.
• The temperature setpoint can be adjusted with the
onboard trimpot or by an external voltage signal.
•
Control loop: the controller employs a smart Proportional‑
Integrating control loop to adjust the drive current. The
proportional term is user‑adjustable, and when properly
configured will quickly settle the load to temperature with
minimal overshoot and ringing.
OPERATING INSTRUCTIONS
TEMPERATURE CONTROLLER
These instructions are written for the most common
application of the LDTCxx20 Controllers: driving a laser
diode, and controlling a Peltier‑type thermoelectric cooler
with a 10 kΩ thermistor sensor. We recommend you read and
completely understand these instructions before proceeding
with wiring the controller. Information for other configurations
is also included in the technical support section on
Wavelength recommends configuring the temperature
controller before configuring the laser diode driver.
Additionally, we recommend using test loads to simulate
the thermistor, TEC or heater, laser diode, and photodiode.
Schematics for test loads are presented in
and
These instructions detail the steps necessary to configure
the current limits for the temperature controller using a test
load. Once that is done, the controller is reconfigured with
the thermal load and sensor for your application. Then the
laser driver is configured with a test load. Finally, the laser
diode is connected and the LDTCxx20 is ready to enter
regular service.
!
Make certain the output leads are not
shorted. If the Laser Output or Temperature
Controller Output leads are shorted during
setup, current will flow and the LDTC may be
damaged.
The configuration sequence is as follows:
• Connect the power supplies and test loads
• Set the current limit
• Replace the test loads with your temperature sensor
and TEC
•
Configure for external or local (internal) control
• Adjust the temperature setpoint and monitor the
controller