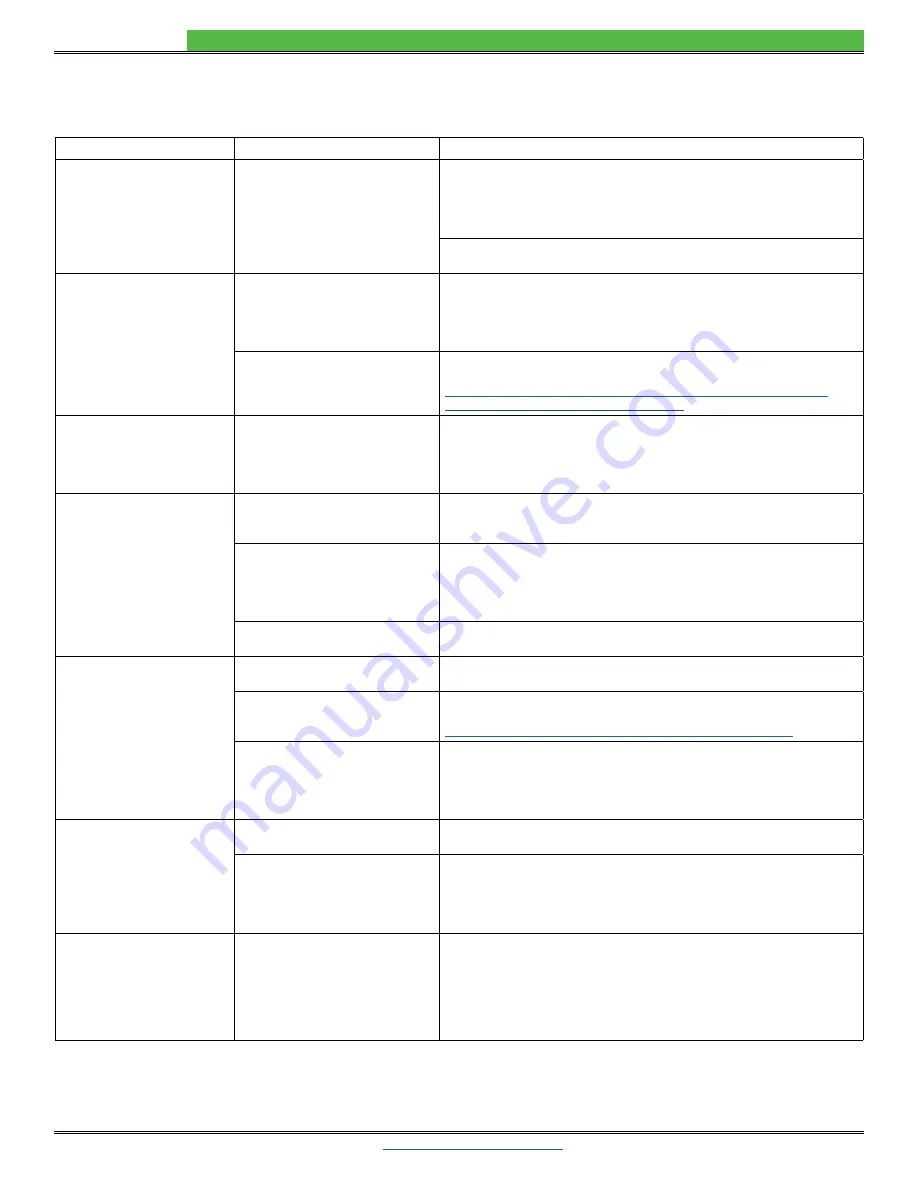
© 2018
23
LDTC0520 / LDTC1020 LASER DIODE AND TEMPERATURE CONTROLLER
TROUBLESHOOTING
TEMPERATURE CONTROLLER
PROBLEM
POTENTIAL CAUSES
SOLUTIONS
Temperature is decreasing
when it should be increasing
–OR–
Temperature is increasing
when it should be decreasing
The TEC may be connected
backwards to the LDTC
The convention is that the
red
wire on the TEC module connects to TEC+ (pin 6)
and the
black
wire to TEC‑ (pin 5). If your TEC is connected in this manner and
the problem persists, the TEC module itself may be wired in reverse. Switch off
power to the system, reverse the connections to the LDTC, and then try again
to operate the system.
TEC wiring polarity is dependent on temperature sensor type (NTC vs. PTC).
Verify that the polarity is correct for the sensor type you are using (
).
Temperature increases beyond
the setpoint and will not come
down
The heatsink may be inadequately
sized to dissipate the heat from the
load and TEC module, and now
the system is in a condition called
thermal runaway
Increase the size of the heatsink, add a fan to blow air over the heatsink, and/
or reduce the ambient air temperature around the heatsink.
Apply a thin layer of thermal paste or use thermal washers between the load,
the TEC surfaces, and the heatsink.
The TEC is not adequately sized for
the thermal load
The heat being generated by the load may be too great for the TEC to
pump to the heatsink; a larger TEC may be needed. Consult our Notes
TN-TC01: Optimizing Thermoelectric Temperature Control Systems
and
AN‑TC09: Specifying Thermoelectric Coolers
for more information.
The temperature of my heater-
based system increases
without stopping
The current limits might not be
correctly configured
When using a heater the current limit trimpots LIM A and LIM B must be set
according to the temperature sensor type you are using. If the load temperature
increases past the setpoint and continues to increase, one of the current
limit trimpots may have been improperly set. Refer to
and
Set the
Temperature Controller Current Limits (page 11)
for more information.
Temperature does not stabilize
very well at the setpoint
Poor thermal contact between
components of the thermal load
Use thermal paste or washers between the load/TEC and TEC/heatsink
interfaces. Make sure the temperature sensor is in good thermal contact with
the load.
Operating outside of the ideal
region of the temperature sensor
The sensor type and bias current should be selected to maximize sensitivity at
the target temperature. Thermistors provide the best performance, particularly
for applications where a single setpoint temperature must be accurately
maintained. For example, at 25°C a 10 kΩ thermistor has a sensitivity of
43 mV/°C, whereas an RTD sensor has a sensitivity of 4 mV/°C.
Proportional control term is set too
high
Reduce the value of the proportional term. For more information, contact the
factory.
Temperature does not reach
the setpoint
Insufficient current driven to the
TEC or Heater
Increase the current limit ‑ but DO NOT exceed the specifications of the TEC
or heater.
The controller does not have
sufficient compliance voltage to
drive the TEC or heater
Increase the power supply voltage; be certain to verify that the controller is
within the Safe Operating Area; the SOA calculator is found at:
www.teamwavelength.com/support/design-tools/soa-tc-calculator/
The temperature setpoint voltage
is below the minimum signal value
of 0.3 V
If the setpoint voltage falls below 0.3 V, the LDTC defaults to a “safe
temperature” setpoint voltage of 1 V (for a 10 kΩ thermistor at 100 µA bias
current, the default temperature setpoint is 25°C). The safe temperature
setpoint voltage can be changed at the factory if your application requires it. To
reset the safety circuit, the voltage must be greater than 0.4 V.
LDTC does not respond to
external temperature setpoint
input
The TREF switch is improperly
configured
To configure the LDTC to reference the setpoint signal on pin J2‑11, set the
TREF switch to EXT (up).
The EXT T SET signal is below the
minimum signal value of 0.3 V
If the EXT T SET signal falls below 0.3 V, the LDTC defaults to a “safe
temperature” setpoint voltage of 1 V (for a 10 kΩ thermistor at 100 µA bias
current, the default temperature setpoint is 25°C). The safe temperature
setpoint voltage can be changed at the factory if your application requires it.
To reset the safety circuit, the EXT T SET signal must be greater than 0.4 V.
Temperature is slow to
stabilize and is not within the
specifications
Setpoint temperature is set close to
the ambient temperature
Set the temperature at least 10°C above ambient when using a resistive heater.
A resistive heater is unable to precisely maintain temperature near ambient
because once the temperature overshoots the setpoint, the controller turns off
and relies on ambient temperature to cool the load. If setting the temperature
10°C or more above ambient is not possible, then choose a thermoelectric
controller, which can alternately heat and cool the load to maintain a more
precise setpoint temperature.