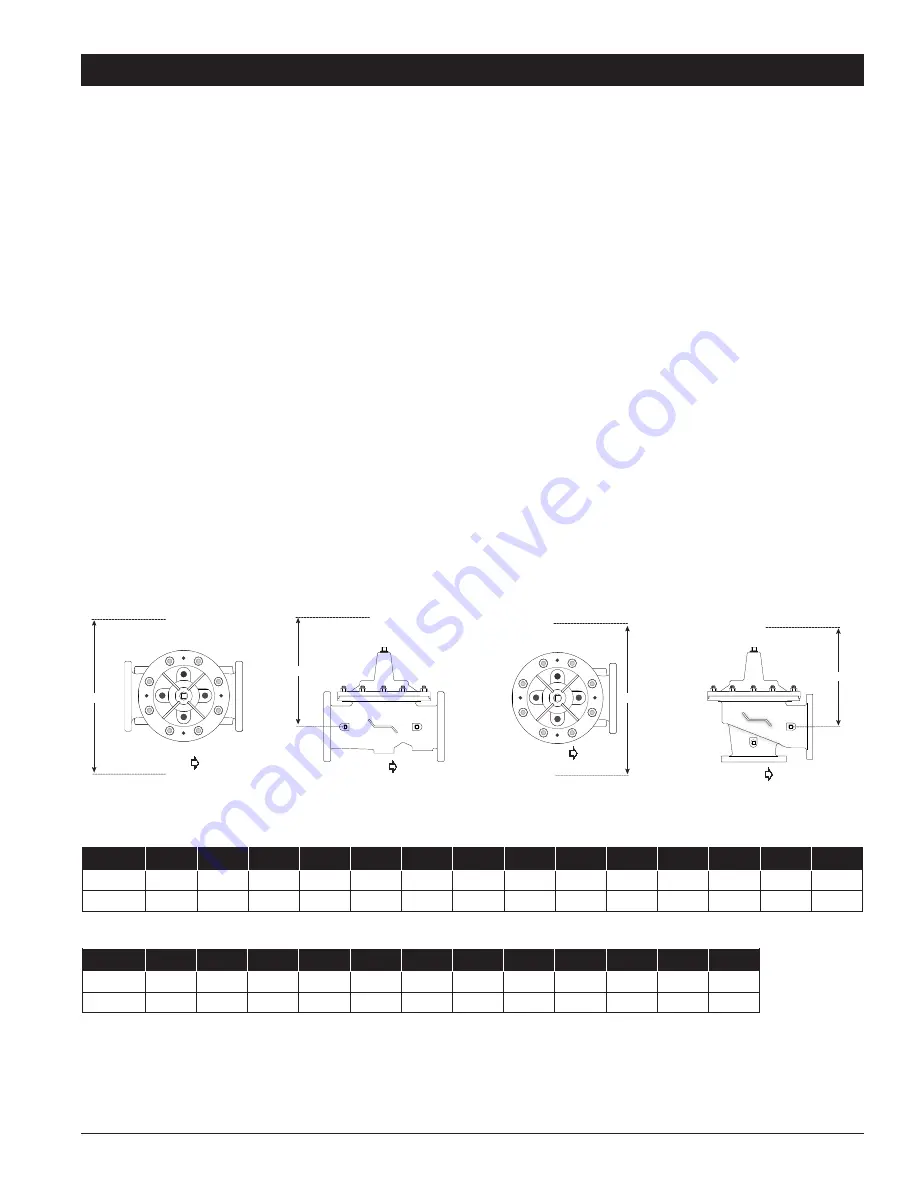
ES-A-ACV-LF984GD 2115
1. Prior to installation, flush line to remove debris.
2. Install valve so the flow arrow matches flow through the line, and gauges to monitor valve inlet and outlet pressures. A Position Indicator
can be installed to provide visual indication of valve position and operation without disassembly.
3. Install isolation valves upstream and downstream of the main valve.
4. Provide adequate clearance for valve servicing and maintenance. Refer to valve servicing dimensions on next page. Avoid installing valves
6" and larger in the vertical position (main valve stem horizontal). Automatic Control Valves (ACVs) are designed for horizontal in-line instal-
lation, with the cover facing up (main valve stem vertical). Slow operation or premature stem and guide wear may occur if valve is not
installed according to factory recommendations. Consult factory for detailed engineering review prior to ordering if valve is to be installed
other than horizontally in-line.
5. If valve is equipped with a pilot control system, extra precautions should be made during installation to protect the piping circuit from dam-
age. Only remove the pilot control system from the valve if necessary. Tubing and fittings should be kept clean and replaced exactly as
removed. Consult appropriate hydraulic schematic to ensure proper re-assembly.
6. Connect solenoid wiring leads to desired switching device, using safe, standard electrical practices.
7. Wire the limit switch contacts to the proper relay connections, using safe, standard electrical practices. Adjust the limit switch collar to the
approximate make/break contact position.
8. After installation, vent entrapped air from valve cover and pilot system by following instructions in the
Commissioning the Pump Control
Valve
section.
9. Field install downstream orifice plate assembly pressure sense lines per schematic.
– To accurately set flow rates, either a differential gauge or a flow meter should be installed.
– Check orifice plate to assure that sense holes are free from obstruction.
18
Globe
Angle
Size (in)
1
1/4
1
1/2
2
21/2
3
4
6
8
10
12
14
16
20
24
A (in)
16
16
20
22
22
24
32
34
38
44
48
52
56
56
B (in)
10
10
12
14
14
16
24
26
28
30
34
40
48
48
Size (in)
1
1/4
1
1/2
2
2
1/2
3
4
6
8
10
12
14
16
C (in)
16
16
20
22
22
24
32
34
38
44
48
52
D (in)
10
10
12
14
14
16
24
26
28
30
34
40
The following tables detail the recommended minimum valve servicing dimensions.
A
B
C
FLOW
FLOW
FLOW
D
FLOW
Valve Servicing Dimensions
Start-up of an automatic control valve requires that proper procedures be followed. Time must be allowed for the valve to react to
adjustments and the system to stabilize. The objective is to bring the valve into service in a controlled manner to protect the system
from damaging over-pressure.
Installation
© 2021 Watts