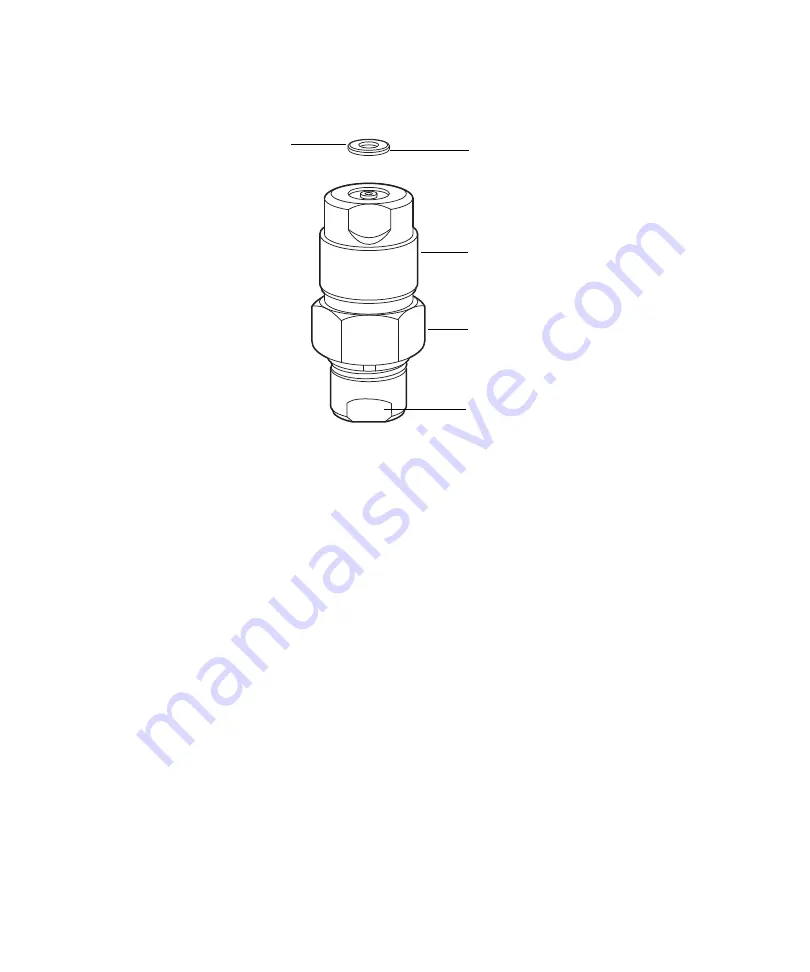
Replacing the primary check valve
September 26, 2013, 715004208 Rev. A
103
6. Ensure the new PEEK washer is inserted into the new check valve so
that its chamfered edge faces away from the check valve.
7. Insert the check valve assembly into the head, and use the 1/2-inch
wrench to tighten the check valve nut 1/8-turn beyond finger-tight.
8. Reattach the low-pressure filter holder to the check valve and
finger-tighten it to the extent possible.
9. Power-on the ISM.
10. Prime the ISM (see
PEEK washer
Check valve
Chamfered edge
facing away from
check valve
1/2-inch Hex nut
5/16-inch, open-end wrench flat