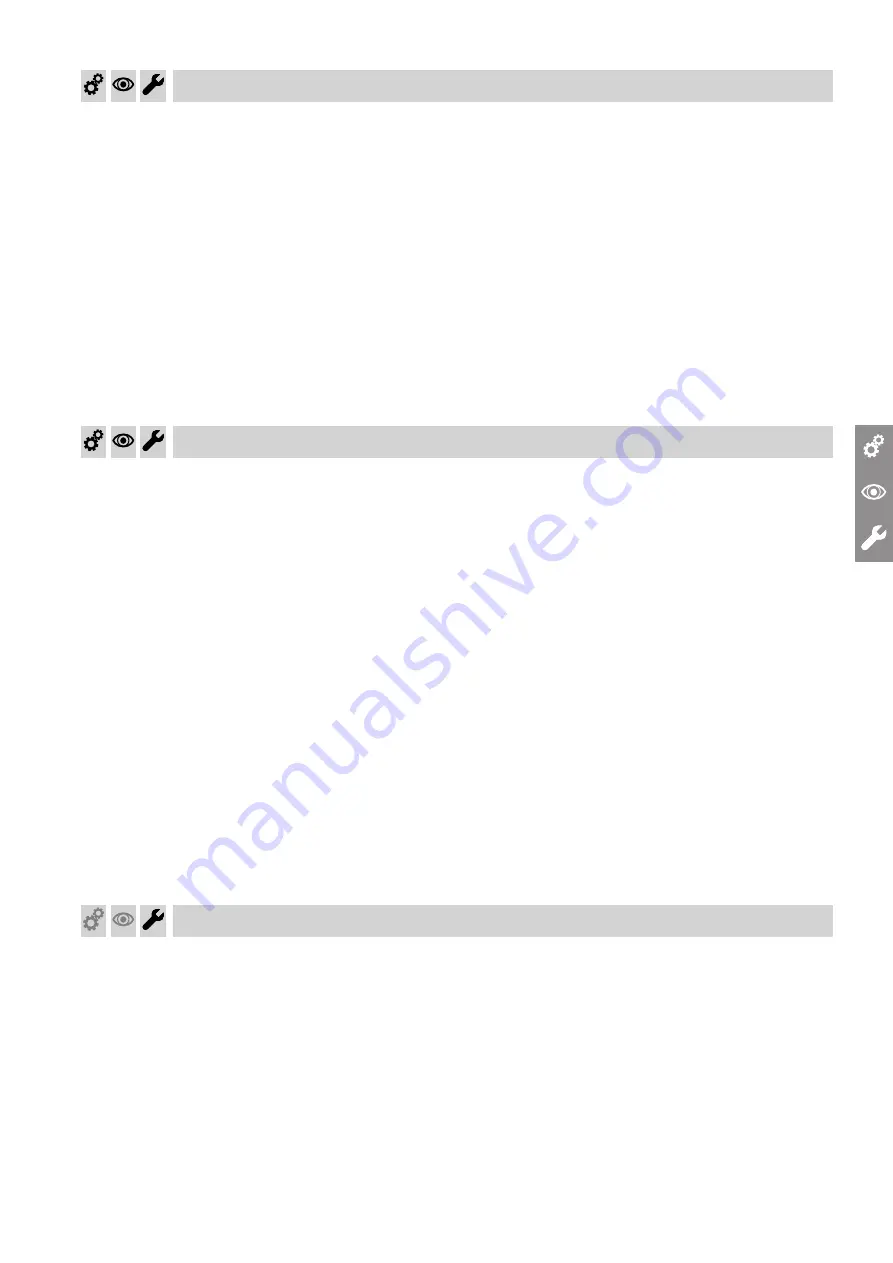
71
4.
Check the system pressure at the pressure gauge.
Top up with water if required.
Minimum system pressure: 0.8 bar (80 kPa)
Permiss. operating pressure: 3 bar (0.3 MPa)
5.
!
Please note
Leaking hydraulic connections lead to appli-
ance damage.
■
Check the internal and on-site hydraulic
connections for leaks.
■
In the event of leaks, switch OFF the appli-
ance immediately. Drain off liquid via the
drain valve. Check the seating of seal
rings.
Always
replace displaced seal
rings.
6.
Close drain & fill valve.
7.
Connect on-site hose to manual air vent valve
B
and open the valve.
8.
Close manual air vent valve
B
after venting has
been completed.
9.
Check the system pressure. Top up with water if
required.
Checking the expansion vessel and heating circuit pressure
Carry out this test on a cold system.
Note
Only use anti-corrosion agents that have been
approved for heat pumps with DHW heating via single-
walled heat exchangers (DHW cylinders).
1.
If an on-site shut-off valve is installed, close it.
Otherwise drain the heating system on the heating
water side until the pressure gauge indicates "0".
2.
If the pre-charge pressure of the expansion vessel
is lower than the static system pressure, top up
with sufficient nitrogen to raise the pre-charge
pressure of the expansion vessel by 0.1 to 0.2 bar
(10 to 20 kPa) higher than the static system pres-
sure.
Example:
Static head (distance between the heat source and
the highest heating surface) 10 m
Equivalent to a static pressure of 1 bar (0.1 MPa).
3.
Top up with water until the filling pressure exceeds
the pre-charge pressure of the expansion vessel.
On a cold system, the charge pressure must be
approx. 0.2 bar (20 kPa) higher than the static
pressure.
4.
During commissioning, mark this value on the
pressure gauge as minimum charge pressure.
Cleaning the interior
!
Please note
Deposits from cleaning agents or chemicals in
the interior can cause appliance damage.
Only clean the interior with clean water; maxi-
mum temperature 50 °C.
Commissioning, inspection, maintenance
Filling and venting on the secondary side
(cont.)
5692878
Содержание Vitocal 350-A AWHI 351.A14
Страница 22: ...22 Fig 13 Installation sequence Type AWHI 351 A only Fitting the supplied floor mat 5692878 Installation ...
Страница 26: ...26 3x 8 9 3x 3x 3x Fig 17 Installation sequence Fitting the outer panels cont 5692878 Installation ...
Страница 27: ...27 10 3x 3x 2x 11 Fig 18 Installation sequence Fitting the outer panels cont 5692878 Installation ...
Страница 30: ...30 Type AWHI 351 A 1 Fig 22 Installation sequence Siting the heat pump cont 5692878 Installation ...
Страница 66: ...66 Fitting the front panel 1 2 Fig 64 Installation sequence Closing the heat pump cont 5692878 Installation ...
Страница 82: ...82 Troubleshooting Repairs cont 5692878 Maintenance ...
Страница 101: ...101 Parts list type AWHI 351 A Heat pump module cont 5692878 Components ...
Страница 104: ...104 Parts list type AWHI 351 A Base frame cont 5692878 Components ...
Страница 110: ...110 Silencer hood 0001 0002 0001 Fig 86 Parts list type AWHO 351 A Casing cont 5692878 Components ...
Страница 114: ...114 0007 0007 0003 0005 0003 0002 0001 0006 0005 0008 Fig 88 Parts list type AWHO 351 A Air module 5692878 Components ...
Страница 125: ...125 Parts list type AWHO 351 A Heat pump module cont 5692878 Components ...