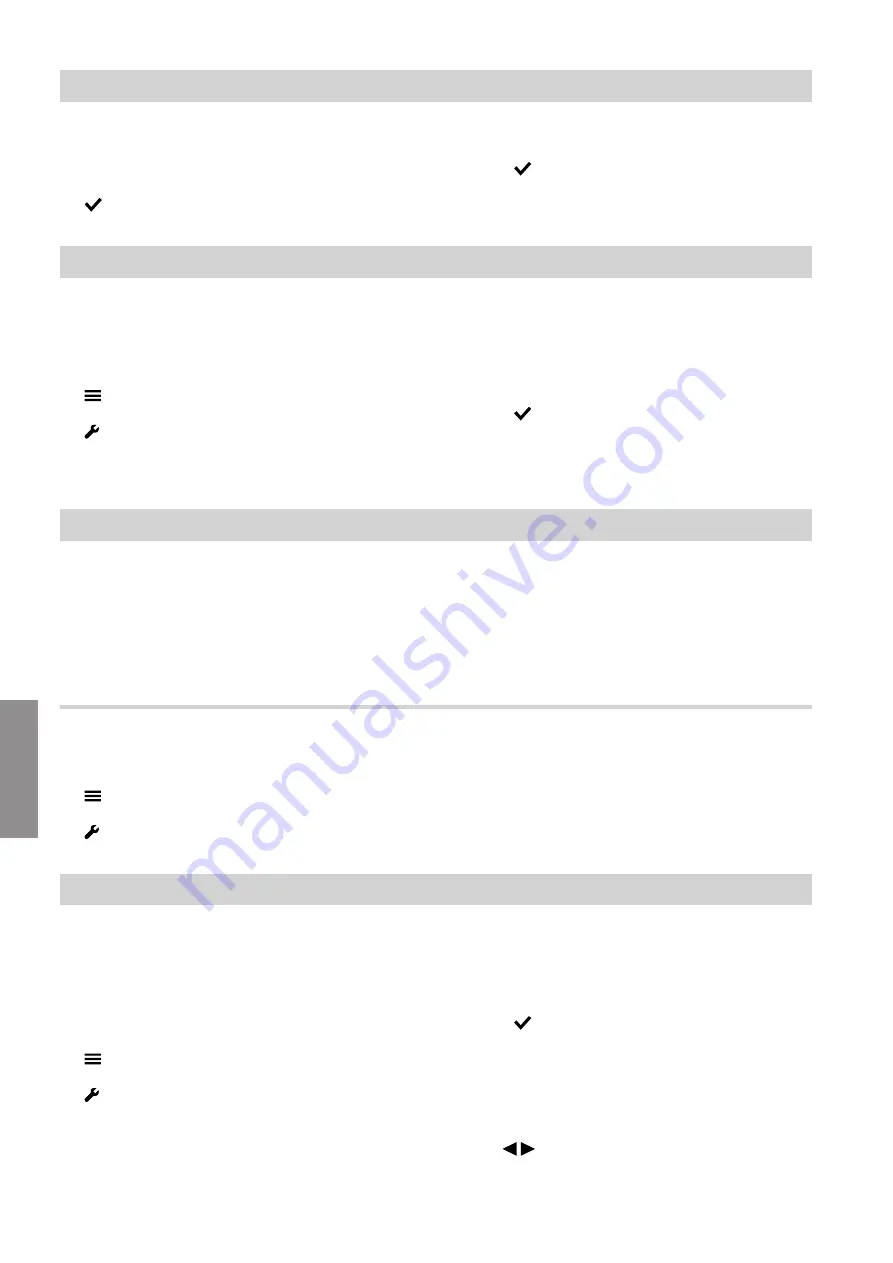
62
5. "Service menu"
6.
Enter current password.
7.
to confirm
8.
Enter new password.
9.
Press
twice to confirm
Resetting all passwords to the factory setting
Tap the following buttons:
1.
Request the master password from the Viessmann
Group Technical Service.
2.
3.
"Service"
4.
Enter password "viservice".
5. "Change passwords"
6. "Reset all passwords"
7.
Enter master password.
8.
Press
twice to confirm
Diagnosis
Checking operating data
Operating data can be called up in different areas: See
"Diagnosis"
in the Service menu overview.
Operating data on heating circuits with mixer can only
be called up if such components are installed in the
system.
Note
If a called up sensor is faulty,
"- - -"
appears on the
display.
Calling up operating data
Tap the following buttons:
1.
2.
"Service"
3.
Enter password "viservice".
4. "Diagnosis"
5.
Select the required group, e.g.
"General"
.
Checking outputs (actuator and sensor test)
Note
When the actuator and sensor test is started, all actua-
tors are initially disabled or valves moved to their cen-
tral position.
Tap the following buttons:
1.
2.
"Service"
3.
Enter password "viservice".
4. "Actuator and sensor test"
5.
Press
twice to acknowledge the security prompt
Note
If an actuator function is not possible due to the
running process, the function is interrupted. A mes-
sage appears.
6.
Use to select the required group: See the fol-
lowing table.
Diagnosis and service checks
Changing the service password
(cont.)
5839343
Diagnosis
Содержание E00T
Страница 8: ...8 14 Keyword index 95 Index Index cont 5839343 ...
Страница 97: ...97 5839343 ...
Страница 98: ...98 5839343 ...
Страница 99: ...99 5839343 ...