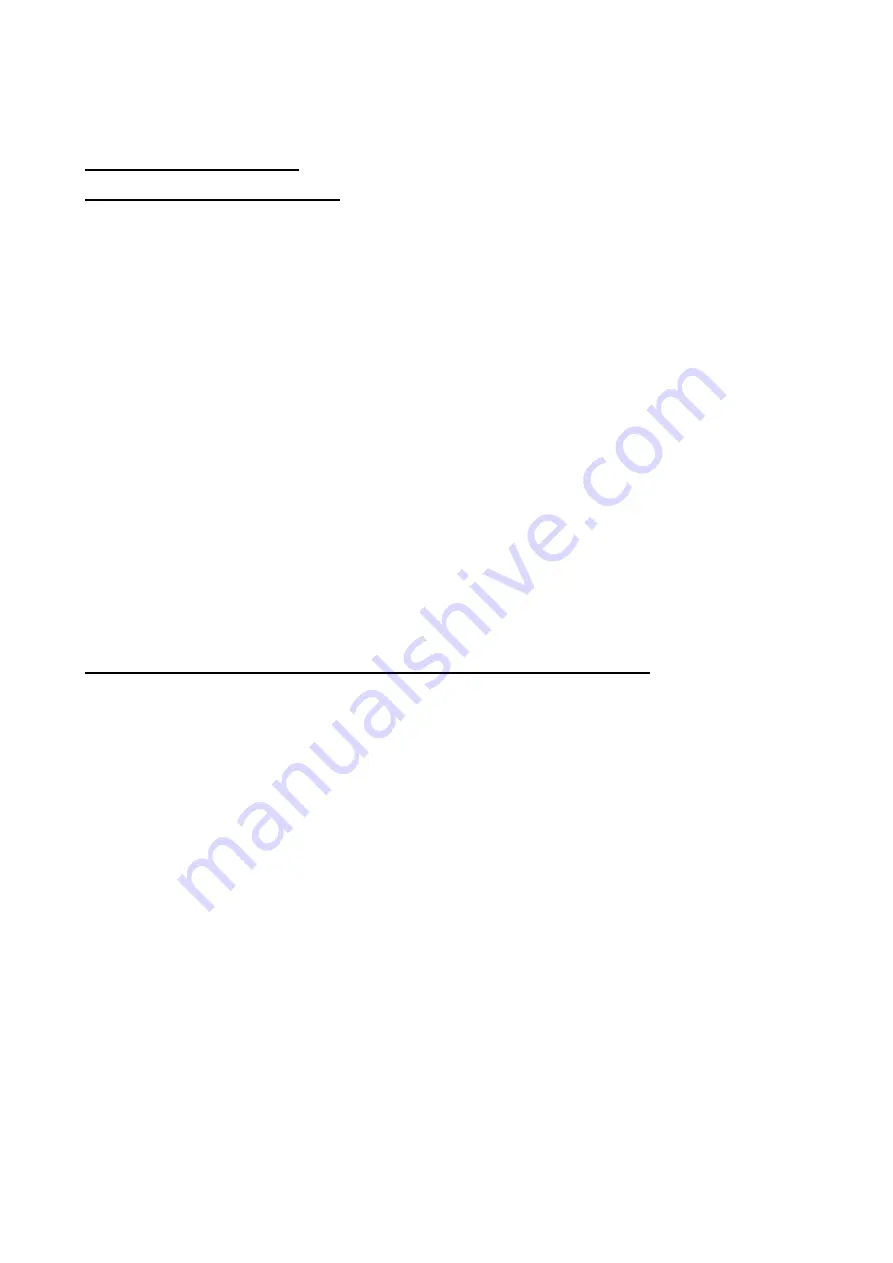
6
WARNING! A poor quality of fuel can markedly negatively affect the boiler output and emission
parameters
4. Boiler description
4.1 Boiler drum construction
The main boiler component is the cast iron sectional boiler drum made of grey cast iron according to
EN 1561.
¾
Central sections – quality 150 (previously
Č
SN 42 2415)
¾
Front and rear sections – quality 200 (previously
Č
SN 42 2420)
The boiler pressure components comply with strength requirements according to:
EN 303-5 Heating boilers – Part 5: Heating boilers for solid fuele, hand and automatically stocked,
nominal heat output of up to 300 kW – Terminology, requirements, testing and marking
The boiler drum consists of cast iron sections by means of forced on boiler insertions and is secured
with anchor bolts. The sections create a combustion chamber and the ash pan space, the water space and
the convection section. The ash pan space is divided from the combustion chamber through a solid water-
cooled grate.
Between the combustion chamber and the convection part of heat exchanger there are installed the
ceramic plates that regulate combustion and influence positively the emission values.
In the flue gases ducts of the heat exchanger convection part there are inserted the turbulators in order
to reduce the flue gases temperature thus to increase the boiler efficiency.
The boiler rear section has in its upper part a smoke adapter and heating water flange (2“), then in lower
part the return water flange (2“) with a sleeve piece for filling and discharging cocks (G 1/2“). To the front
section there are mounted the stoking and ash pan doors; the combustion chamber door is behind them.
The whole boiler drum is insulated by using a health harmless mineral insulation which reduces the heat
interchange losses in surroundings. The steel boiler shell is treated by applying a good quality powder paint.
4.2 Construction of combustion chamber and fuel transport lines
The combustion chamber consists of a longitudinal concave drum made of heat-resisting steel to which
there joins askew from below the piping for fuel supply with a screw conveyer for the combustion chamber.
This conveyer is also connected with pellets reservoir through another height offset (mismatch) screw
conveyer which is equipped with regulators functioning in dependence on discharging the combustion
chamber conveyer. The combustion chamber concave drum which is interconnected with forced air supply is
equipped with a system of slots in the side walls and in the bottom for the purpose of primary air supply.
Thanks to a convenient combustion chamber disposition the combustion chamber functional space
doesn’t get clogged with the combusted material. This after combustion is continually and mechanically
expelled by the fresh fuel supply. The unburnt fuel will not become clinkered neither will it become attached
to combustion chamber walls. The combustion is safe. Thanks to the regulated fuel supply and the screw
conveyer height offset (mismatch)there is excluded the fuel transport lines fire penetration.
The combustion chamber screw conveyer and the fuel reservoir screw conveyer are mutually
interconnected through a flex hose.
Combustion chamber is from above covered by a ceramic arch which directs the flames to the secondary
air inlets. This results in a better combustion with a significant reduction in light ash particles.