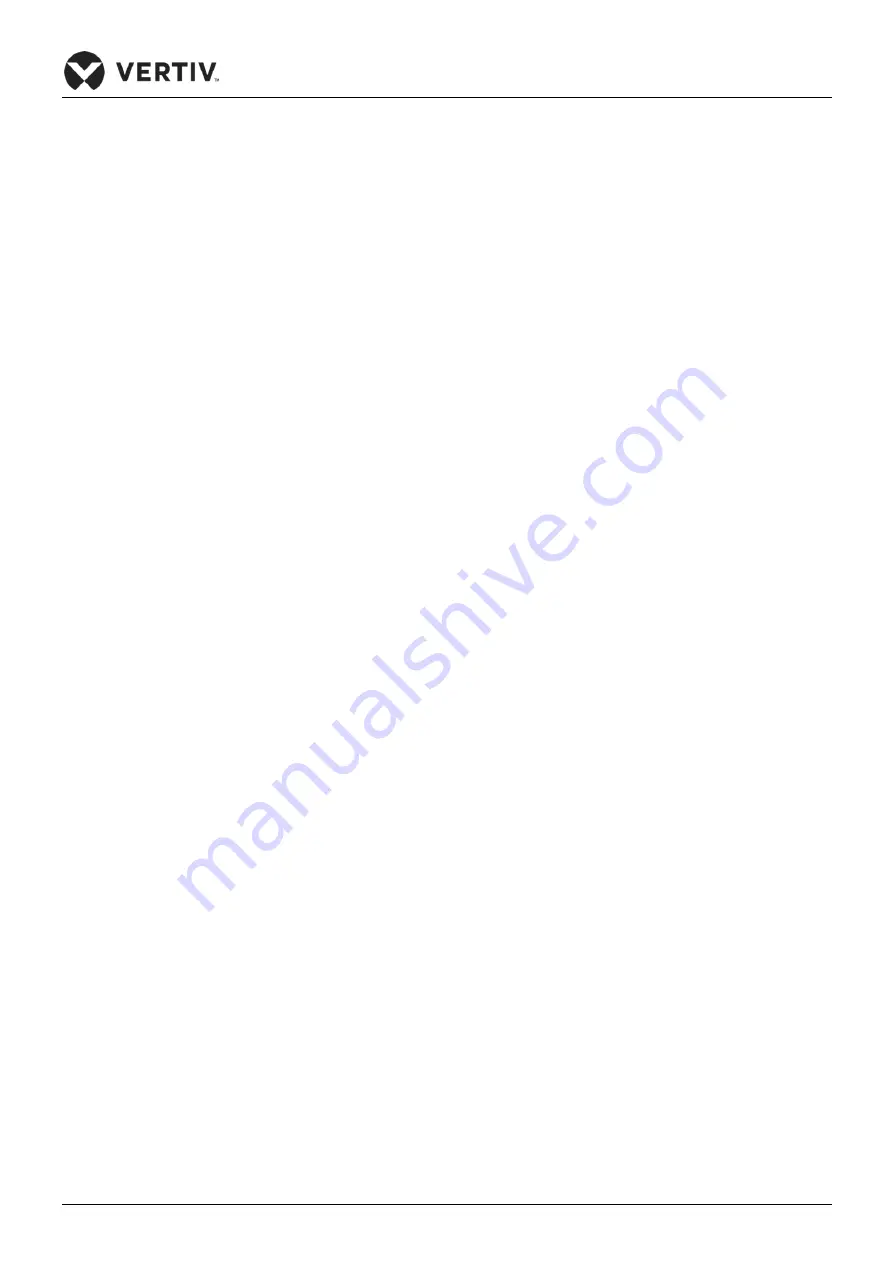
Installation
Vertiv | Liebert CRD10 | User Manual
22
2.6
Installation Preparation (Site Preparation)
The CRD10 models of air conditioners are streamlined for maintaining a favorable environment for data
centers, computer rooms, and similar systems. Strict adherence to the installation procedures is mandatory
to ascertain proper installation of the air conditioner.
2.6.1
Equipment Room Requirement
The equipment room must be prepared to ensure smooth operation and obtain accurate results. The
equipment room must meet the standards for appropriate ventilation and heating. The design specifications
for the air conditioners must be ideal and should be-in-line with energy-efficient design standards. Following
are the requirements for maintaining a favorable room environment prior to installation:
1.
The equipment room should be well insulated and have a sealed damp-proof layer.
2.
The outdoor air entering in should be kept at a minimum. The outside air will add the loads of heating,
cooling, humidifying, and dehumidifying of the system. It is recommended that the inhalation of outside
air be kept below 5% of the total indoor airflow.
3.
All the doors and windows should be properly sealed to minimize the leakage. The seams should be as
narrow as possible.
NOTES:
• Vertiv recommends defining the site p
reparation as per the requirements. However, if these
requirements are not met, the site must be rectified to meet the specified requirements and
conditions.
• If the recommended rectifications
or modifications are not implemented, then Vertiv does not
guarantee the accuracy and precision of the temperature and humidity provided by the Liebert CRD10
models.
• An important
aspect to be considered is that the indoor unit must not be used for the outdoor
environment.
2.6.2
Installation Space Requirements
The Liebert CRD10 models are advanced precision air cooling units and therefore, air conditioners must be
installed, preferably in a row of cabinets with high heat density and in a hot aisle and cold aisle arrangement.
Allocate space to make it accessible to qualified service staff for repair, maintenance and service.
A minimum space of 600mm[23.6in.] must be assigned for maintenance at the front of the system and at
the rear of the system. The allocated space is to facilitate regular maintenance tasks such as removing filters
for cleaning, fans or compressor. Figure 2-6 shows the space allocation for servicing and maintenance.