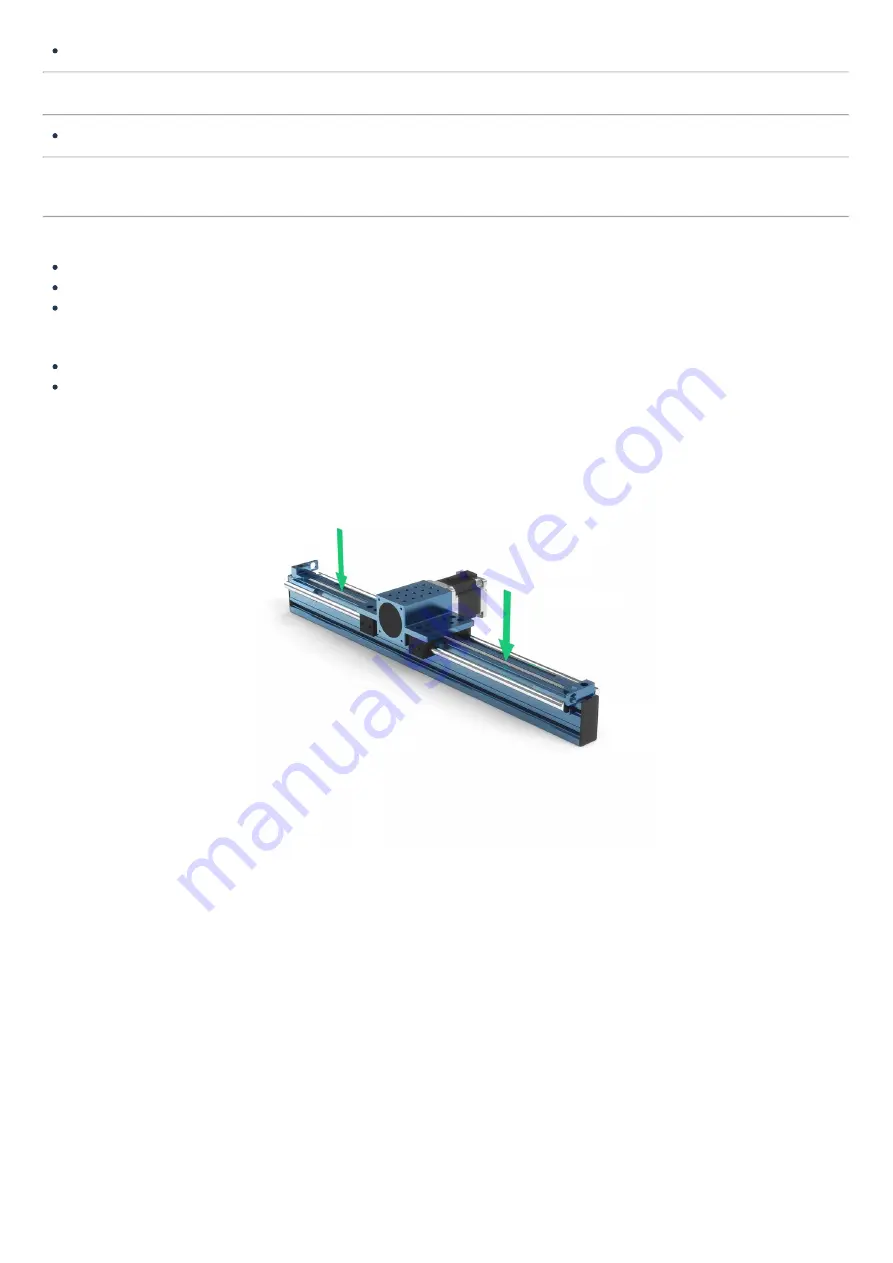
Prior to the initial installation.
The pinion and gear segments are coated with rust preventive oil for shipping and storage and must be properly lubricated upon assembly.
Once every 6 months, or after every 20 km of travel —whichever comes first.
The lubrication interval is application-dependent. You may need to lubricate more frequently depending on the duty cycle, usage, and environment. If the
lubricant appears to be dispersed before this point or has become dry or crusted, the maintenance interval should be reduced.
Before lubrication:
Visually inspect the gear rack segments for any accumulation of foreign matter.
Using a cloth with solvent, remove any contaminants and old lubricant that may still be in place on the gear rack segments.
Cycle the pinion housing along the gear rack segments several times. Wipe with a dry, lint-less cloth and perform the lubrication immediately after.
Lubrication Procedure:
We recommend applying the grease directly on the gear rack segments (as shown below) so that each tooth flank is barely damp with lubricant.
In order to distribute the grease throughout the gear rack segments and on the pinion, it is recommended to run the pinion housing two to five times over
its complete operating stroke.
Figure 7: Green arrows indicate suggested locations for applying grease to the gear rack, MO-LM-020-XXXX.
Enclosed Timing Belt Actuator (MO-LM-026-XXXX, MO-LM-027-XXXX, MO-LM-028-XXXX)