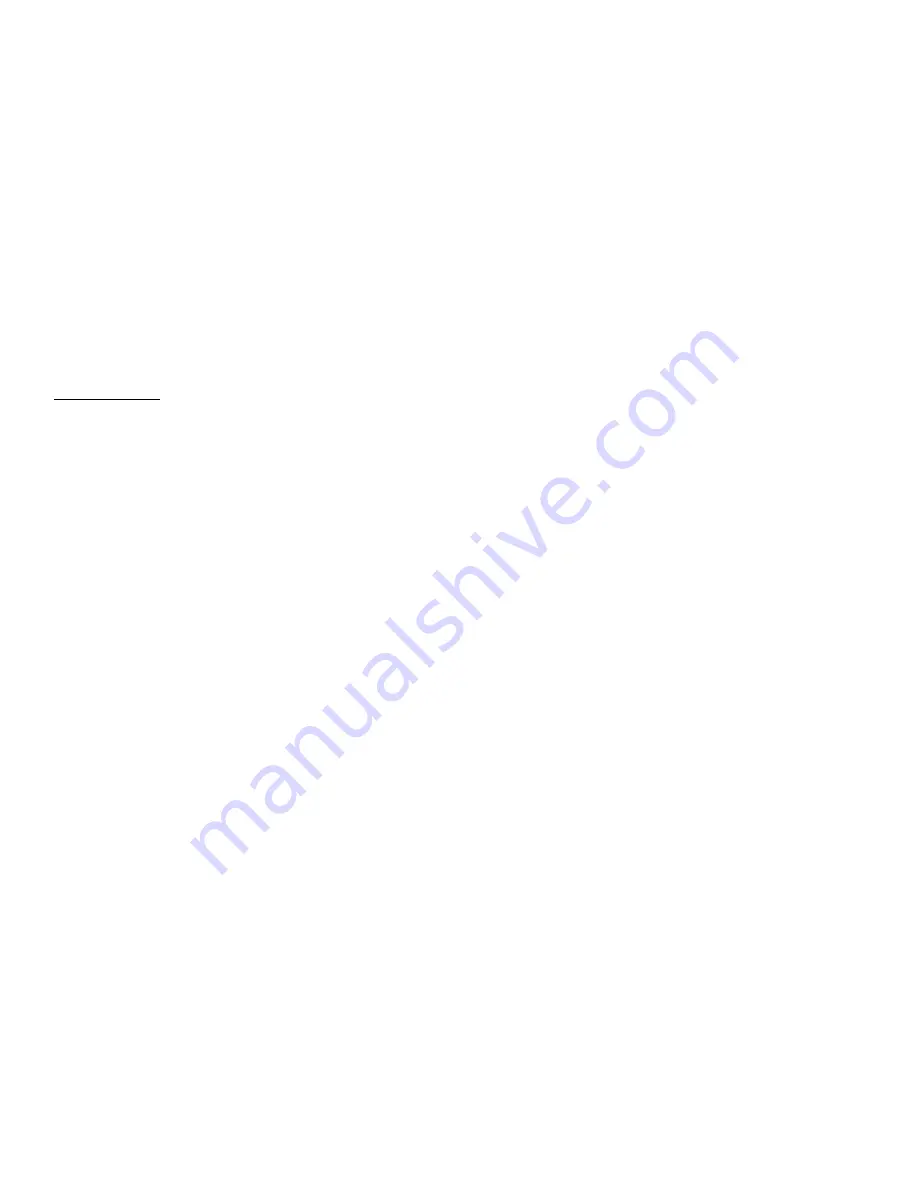
12
supply line can by employed by installing piping between the cooling liquid discharge nozzle at the pump Casing to the cooling
liquid supply connection nozzle on the silencer or the after cooler. Cooling medium supply piping should include the instruments
listed below:
*
If a Water Jacket type Silencer or After Cooler is installed, this Silencer / After Cooler also requires Cooling water piping.
COOLING LIQUID SUPPLY LINE
•
Manual isolation valve
•
Strainer
•
Pressure gauge with an isolation valve
•
Liquid flow meter
•
Liquid flow switch (Or, combined cooling liquid flow meter/switch)
•
On/Off solenoid valve
•
Flow regulating valve
•
Temperature gauge
COOLING LIQUID DISCHARGE LINE
•
Temperature gauge
•
Temperature switch (Optional)
OPERATION
PREPARATION FOR OPERATION
1. Ensure the pump internal and process piping are thoroughly cleaned and free from weld slags, metal chips, particulates, rusts,
dusts etc.
2. Ensure all the process piping connections and utility piping connections are properly installed/tightened and supported.
3. Ensure the lubrication oil at the DE oil reservoir of the pump is filled up to the top level of RED Mark or OL Mark while the pump
is NOT in operation.
4. Adjust and set the cooling liquid flow rate listed on the “SDV Technical Data” table.
5. Ensure the electrical power connection to the motor or electrical/control panel is completed and is ready to supply power to
the motor.
NOTE: Remember that the right oil level is crucial for the pump performance. If the pump were operated with low oil level, the
gears and bearings would seize by lack of lubrications. If the oil is overfilled, the oil temperature gets elevated and would cause
high gear noise and may affect integrity of the other parts within the DE (Drive End) Casing.
OPERATION
1. Ensure the direction of the pump rotation is correct; CW (Clockwise) direction, looking from the motor. A pump rotational
direction check can be done by jogging the pump a brief moment while checking the rotational direction of the motor fan. If
the motor rotates CCW (Counter-Clockwise), correct the power cable connections and check the rotational direction again
to ensure the pump rotates in correct CW direction. Pump rotational direction check should be done with the process inlet
isolation valve open.
2. With the process inlet isolation valve open, operate the pump for 20 to 30 minutes. At this stage, all pump operating parameters
should be checked for any abnormality; such as excessive vibration, high oil/grease temperatures, high cooling liquid discharge
temperature, high process discharge temperature noise, over current draw etc. In case of observation of any abnormality, stop
the pump and investigate for the cause of the abnormality. Typical causes of abnormalities come from improper lubrication
and/or improper installation of the pump.
3. Upon completion of the above step, operate the pump for 2 to 3 hours under normal process load condition and check the
pump operating parameters again.
4. If an abnormality is found during the initial operation with normal process load, shutdown the pump immediately and ensure
the problem is corrected prior to re-startup of the pump.
5. Pump operating conditions should be within the limits shown on the “Specifications Table” on page 6:
• Max. Process Inlet Temperature
• Process Discharge Temperature
• Oil Temperature
• Grease Temperature
6. Cooling Medium Differential Temperature is determined by subtracting the Supply temperature from the Discharge temperature.
For water, differential temperature must be within 12.6°F.
7. Observe other operating conditions as well, such as: noise, vibration, and motor current draws (amps)
Содержание KINNEY SDV SDV-120
Страница 28: ...28 NEW SDV 320 EXPLODED VIEW DRAWING NOTES ...