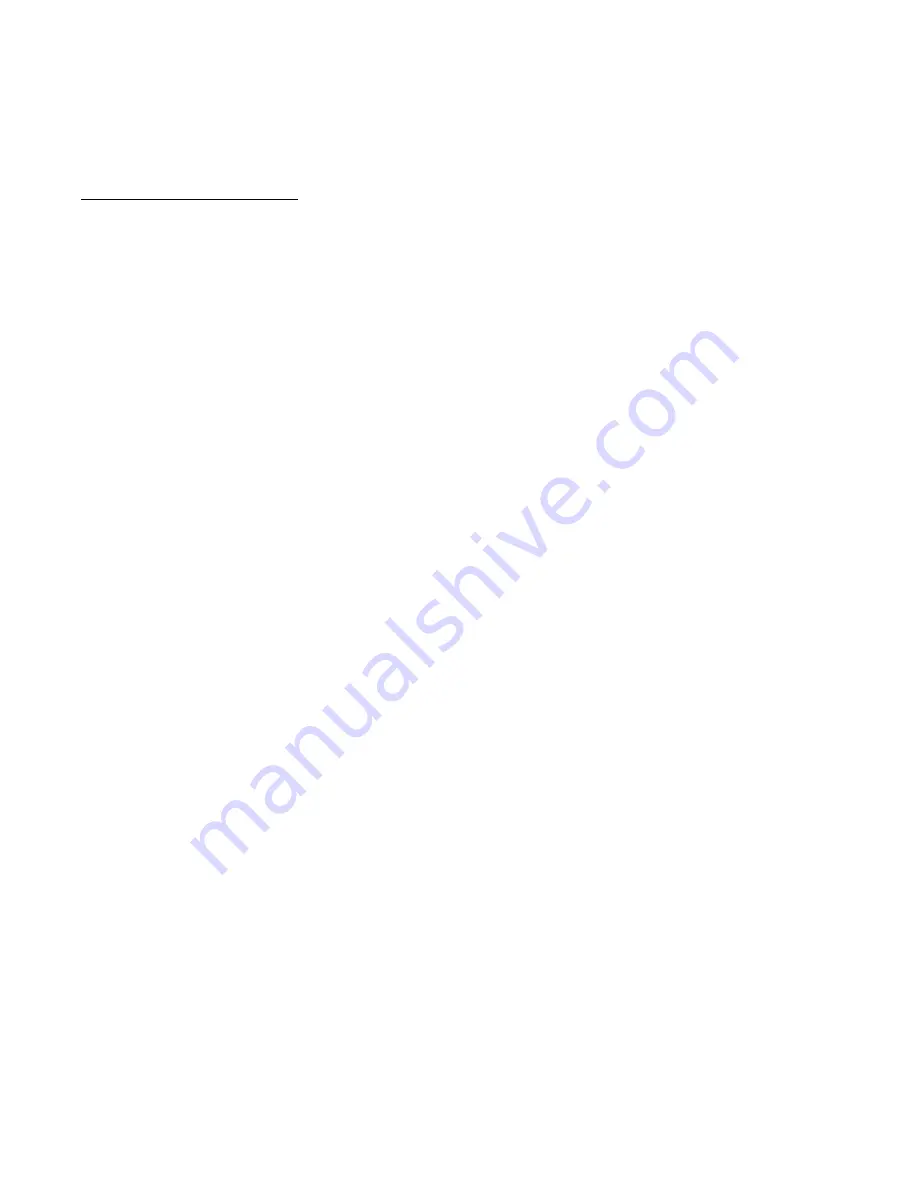
11
•
Flow rates listed are Minimum.
•
FLUSHING PURGE should last for 30 minutes with the pump suction valve closed, after process operation is ended.
•
All PURGE work except for flushing should be done at the same time as the process starts up.
•
Sealing purge at NON-DRIVE END can vary a little according to the type of process and operating condition.
•
The COOLING PURGE amount can vary with the vacuum level.
HANDLING PROCEDURE
ASSEMBLY OF PIPING
LOCATION
1. The pump should be mounted on a base frame with sufficient rigidity and placed on a flat and level surface.
2. If it is to be installed outdoors, please ensure the motor, painting, peripheral equipment, and parts, etc. are suitable for the
outdoor operations.
3. There should be enough space around the pump to allow for safe maintenance work and periodic inspections.
FOUNDATION
1. Foundation for the pump assembly and it’s base frame should be flat, leveled, and have adequate load bearing capacity.
2. Pump and its base frame, peripheral equipment and piping should be installed when the fountation concrete has been cured.
INSTALLATION
1. SDV pumps should always be operated in a horizontal and level position. SDV pumps should never be installed in an upright
(vertical) or angled position, and should be installed on a rigid base frame.
2. Pump assembly with the base frame should be placed on a foundation and should be supported evenly. Metal shims should
be inserted between the base frame and the foundation, if required for leveling. Pump assembly with the base frame should be
leveled to within 0.5 mm (0.02”) in any 1 meter (3.28 ft)
3. Use adequately sized anchorbolts.
4. Upon completion of the setting of the pump assembly on the foundation and anchorbolts, the base frame should be adequately
grouted prior to tightening the anchorbolt nuts. Anchorbolt nuts should be tigtened after the grout is firmly cured. Anchorbolts
should be tightened evenly to ensure the previously set level is not changed.
PIPING WORK
MAIN PIPING
1. Process Piping internals should be clean and free from rust, dust, foreign materials, weld slag’s etc.
2. A 40-mesh strainer supplied along with the SDV pump should be placed at the pump process inlet nozzle. After initial start-up
and continued operation of the SDV pump for several hours, disassemble the process inlet piping from the pump and check
the strainer for cleanliness. If there are any particulates strained such as weld slags etc, clean the mesh strainer and replace to
the pump process inlet nozzle. It is highly recommended to check this strainer regularly for its integrity and cleanness.
3. It is required to install expansion joints on the suction side of the pump as well as the discharge side of the pump. These
expansion joints are to prevent direct application of any excessive load (primary and secondary load) to the pump assembly
from the process piping structures. Process piping must be supported and guided such that the pump assembly is relatively
free from any excessive load imposed from the process piping structures.
4. Where process exhaust silencer is provided, it should be installed on or as near to the pump discharge nozzle as possible.
5. A check valve should be installed as close to the process inlet nozzle as possible, which is used to isolate the pump from the
process during the pump shut down. The pump will turn in reverse direction if check valve is not present at the process inlet
nozzle by the pressure differentials. Where a check valve installation is not permitted for any reason, a process isolation valve,
such as a gate valve, should be installed. However, operational procedures must include a pump shut down procedure that
includes closure of this process isolation valve prior to pump shut down. It is highly recommended to install a process inlet
isolation valve whether a process inlet check valve is installed or not.
6. Where the process gas contains high condensable vapors, a condensate recovery tank should be installed. The tank should
be designed to collect the condensates and disposed or drained, as it required.
COOLING WATER PIPING — SDV pumps are equipped with an integrated cooling liquid jackets. A cooling medium, typically
water, must be supplied to the cooling liquid supply nozzle located at the FEC (Front End Plate) which will be circulated to the pump
Casing and discharged from the discharge nozzle located on the Casing. Where water-jacketed discharge silencer or after cooler
is supplied with the pump, the silencer or after cooler should also receive the cooling liquid as well. A single loop cooling liquid
Содержание KINNEY SDV SDV-120
Страница 28: ...28 NEW SDV 320 EXPLODED VIEW DRAWING NOTES ...