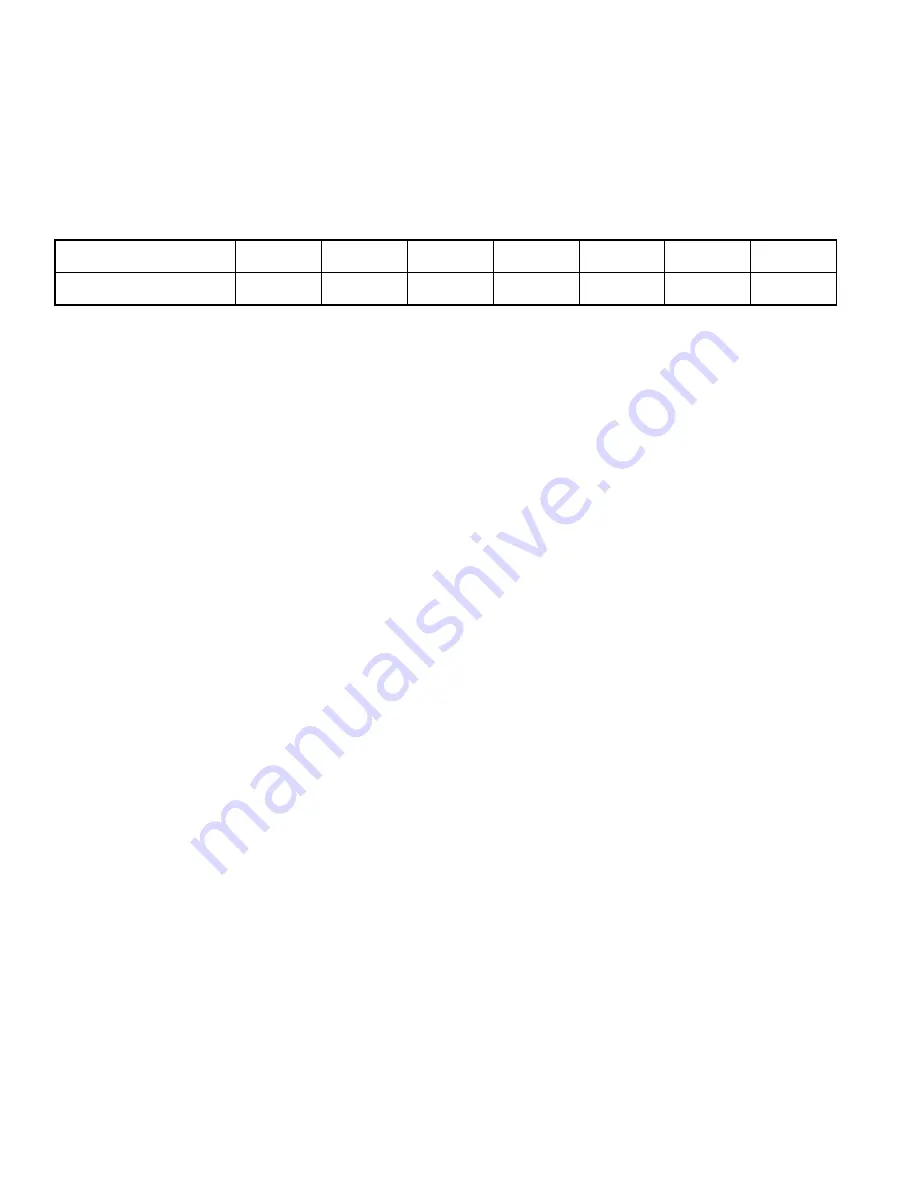
10
Stop (Cleaning) Purge: Upon completion of process pumping operation, close the inlet process isolation valve and start supplying
the purge gas to the pump while the pump is continuously operating for 20 to 30 mintes to remove residual process gas from the
pump internals. Motor should be stopped upon completion of the Stop (Cleaning) Purge while the process isolation valve remain
closed.
NOTES:
•
Start/Stop (Cleaning) Purges should last for 20 to 30 minutes with the process isolation valve closed, prior to the start
of the process operation and immediately after the completion of the process operation.
•
Purge Pressure: 1.5 kg/cm2g (21.3 psig) Max.
•
Flow Rates: slpm (sgpm)
SDV-120
SDV-200
SDV-320
SDV-430
SDV-800
SDV-1500
SDV-2700
Start/Stop (Cleaning) Purge
25 (6.6)
25 (6.6)
40 (10.6)
48 (12.7)
65 (17.2)
160 (42.3)
220 (58.1)
STEAM FLUSHING
The SDV pump should be operated for 10 to 20 minutes upon completion of process batch cycle with the process isolation valve
closed where there’s no Start/Stop (Cleaning) Purge system and sequence in place. This duration of dry operation without process
load is to remove any residual process gas or condensed process vapors from the inside of the pump that may have accumulated
during the process operation. These residual process materials could be a source of pump motor overload when the pump is re-
started. If this residual process material has not been removed by the dry operation after the process operation and the pump is
re-started the residual process material inside of the pump could cause a pump seizure by excessive frictional load to the motor or
damage the screws and/or the casing.
In such case there’s enough amount of the residual process material build-up within the pump, the pump internal should be cleaned
out. Steam Flushing is one way to clean the residual process material build-up from the pump internal. When there is enough
residual process material build-up, please ensure that the pump is not forced to rotate by the motor. Especially for the processes
that have a high potential for build-up and are aggressive in nature, such as, processes with Oligomer, Monomer, Polymer, Resin,
etc; should be cleaned out regularly by Steam Flushing.
1. Steam pressure: Approximately 1 kg/cm2g (14.22 psig)
2. System Isolation: Disconnect all electrical and control powers and place lockout tags on the MCC and/or Control Panel
to ensure no one accidentally starts the pump during the Steam Flushing. The process isolation valve should be closed.
Discharge valve (if applicable) and silencer drain valve should be open.
3. Inject steam for 10 to 20 minutes through the pump’s process inlet (suction) nozzle or one of the nozzles located at the side
of the pump’s process inlet (suction) nozzle. Injection time can be varied based on the types and amount of residual process
material built-up within the pump.
4. Rotate the pump shaft by HAND to check whether the pump rotates without too much frictions or not.
5. If the pump rotates smoothly by hand rotation, stop the steam injection and start the pump motor with process isolation valve
closed.
6. If the pump does not rotate smoothly by hand rotation, repeat steps 3 and 4 until the pump rotates smoothly by hand. Depending
on the severity of the residual process material build-up, it may require repeating steps 3 and 4 several times.
STEAM FLUSHING METHOD (AFTER PUMP OPERATION)
1. Process materials that require Steam flushing: Oligomer, Monomer, Polymer, Resin, etc.
2. Steam pressure: approx. 1 Kg/cm2g (14.22 psig)
3. Flushing Procedure: Close Suction valve, Open discharge valve or Silencer/Separator’s Drain valve
4. Inject Steam for 10 to 20 minutes (the injection time varies with the process material being removed) through pump suction line
or through a plug in suction flange
5. Try to rotate the pump shaft (Pulley or Coupling) by hand to see whether the pump rotates smoothly (during this time, be careful
not to start the motor and observe all lock out/tag out procedures).
6. If the pump rotates smoothly, stop injecting steam.
7. Then, start the motor and check if the pump runs normally.
8. If pump does not turn after performing this procedure, it may be necessary to repeat this procedure 2 to 3 times.
NOTES:
•
PURGE PRESSURE: 0.5 to 1.5 kg/cm2 (7.1 to 21.3 psig)
Содержание KINNEY SDV SDV-120
Страница 28: ...28 NEW SDV 320 EXPLODED VIEW DRAWING NOTES ...