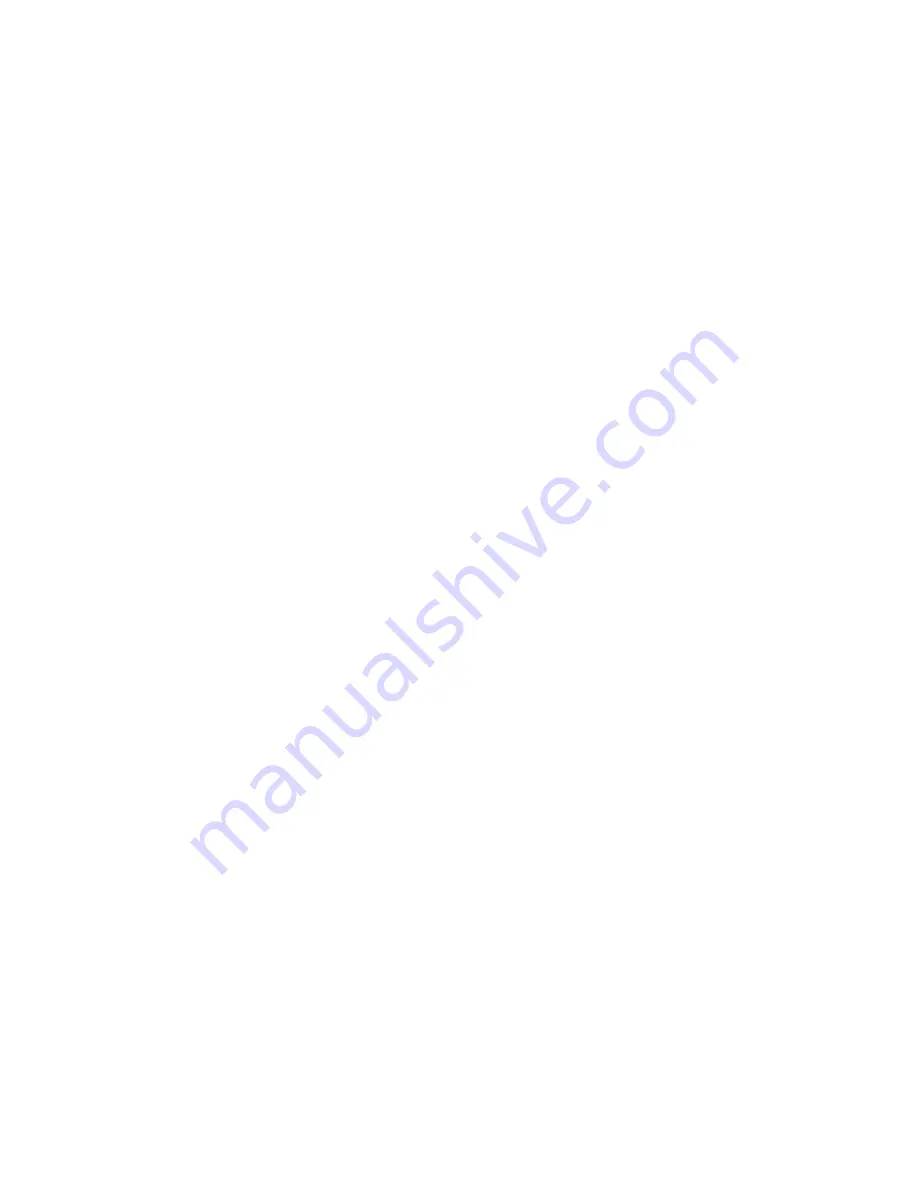
29
Feed Roller Replacement
Worn rollers can affect machine accuracy and feeding of material. Top rollers on all TRC 1000
series cutters can be resurfaced several times by contacting TRC Industries. Bottom rollers
cannot be resurfaced, because their diameter and the precise movement of the stepper
motors create accurate material lengths. On older machines (Pre-2000 or so) removal of the
side plate is required to access and replace the top roller. Newer cutters benefit from a larger
hole in the side plate, allowing the rollers to be removed after the spring arm has been
removed. For removal of the top roller alone on these newer machines, see the next section,
titled “Top Roller Replacement”.
For all older machines, follow the steps below. To determine if
new rollers are needed, rollers can be inspected by shining a flashlight through the outfeed
side and looking through the infeed side at the gap between the two rollers. If large gaps from
wear appear, it is probably time for new or resurfaced rollers.
•
Disconnect power and air. Allow hot surfaces to cool to prevent contact with hot
surfaces.
•
Remove pulley guard and guard plates
•
Loosen motor bolts
•
With the motor bolts loosened, pull the motor gently towards the outfeed side of the
machine. The drive belt should be loose enough now to remove it.
•
Each aluminum pulley will have two set screws that affix it to its shaft. Loosen these with
an Allen wrench and remove the pulley from the drive roller shaft
•
Remove each of the spring arm blocks (HC-3 or CC-3).
•
Loosen spring arm bolt and remove spring arm from motor side (AM-1R)
•
Remove all screws securing side plate to center plates. There are between 12 and 14
depending on the model of cutter.
•
Separate side plate from the cutter chassis, being careful not to pull the cable from the
motor to the DB-15 connector at the infeed side of the machine. Do not pull out any of
the wires.
•
With the motor side plate of the machine off, now is a good time to test the top and
bottom roller bearings. Spin the roller and rotate the bearings, listening for abnormal or
rough sounding bearings. Spinning the bearings by hand, feel for rough patches or
spots. Bearings should be smooth and roll without catching.
•
Both rollers can be removed by pulling them out of the bearings that are holding them
in place on the opposite side plate. Replace desired rollers. Make sure the new drive
roller is replaced with the long end of the shaft s
ticking out the motor side, or you’ll have
to repeat the process to get the shaft stuck out the correct end.
•
Re-assemble in reverse. Barely tighten all bolts to allow for proper plate alignment, and
then hand tighten all side plate bolts. Check for free roller operation after tightening the
side plate bolts.
•
After the machine is back together, the spring arms bolts should both be loosened.
Using one hand, press down on the top roller gently so the top and bottom roller make
good contact. Tighten the spring arm bolts with the other hand. This will make sure the
two rollers are parallel to each other. This can be verified by shining a flashlight through
the outfeed side and looking through the infeed side at the gap between the two
rollers. There should be very little gap, and if any, it should be even across the roller.
Содержание 1000 4.5 Hot cutter
Страница 1: ...Service Manual for 1000 Series Strip cutters Rev 1 1 6 6 22 ...
Страница 53: ......
Страница 54: ......
Страница 55: ......
Страница 56: ......
Страница 57: ......
Страница 58: ......
Страница 59: ......
Страница 66: ...Drive Transistor Test ...