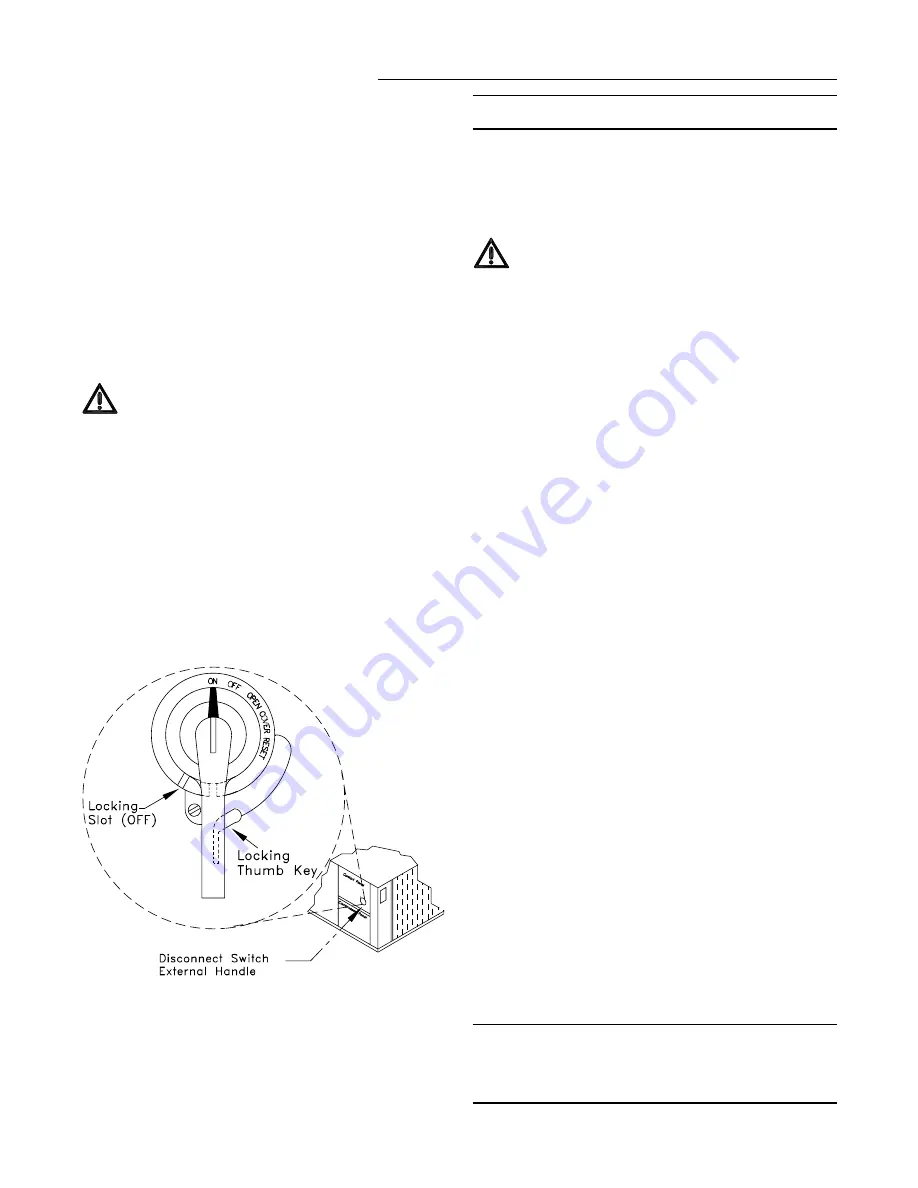
19
Field Installed Electrical Wiring
Disconnect Switch External Handle
(Factory Mounted Option)
Units ordered with the factory mounted disconnect switch
come equipped with an externally mounted handle. This al-
lows the operator to disconnect power from the unit without
having to open the control panel door. The handle location
and its three positions are shown below;
ON
-
Indicates that the disconnect switch is closed,
allowing the main power supply to be applied at the unit.
OFF
-
Indicates that the disconnect switch is open,
interrupting the main power supply at the unit.
OPEN
COVER/RESET
-
Turning the handle to this
position releases the handle from the disconnect switch,
allowing the control panel door to be opened.
WARNING
Hazardous Voltage!
Disconnect all electric power, including remote discon-
nects before servicing. Follow proper lockout/tagout
procedures to ensure the power can not be inadvertently
energized. Failure to disconnect power before servicing
could result in death or serious injury.
Once the door has been opened, it can be closed with the
handle in any one of the three positions outlined above, pro-
vided it matches the disconnect switch position. The handle
can be locked in the "OFF" position. While holding the
handle in the "OFF" position, push the spring loaded thumb
key, attached to the handle, into the base slot. Place the lock
shackle between the handle and the thumb key. This will pre-
vent it from springing out of position.
An overall layout of the field required power wiring is illus-
trated in Figure 8. To insure that the unit's supply power wir-
ing is properly sized and installed, follow the guidelines out-
lined below.
Note: All field installed wiring must conform to NEC
guidelines as well as State and Local codes.
Verify that the power supply available is compatible with the
unit's name plate ratings for all components. The available
power supply must be within 10% of the rated voltage
stamped on the nameplate. Use only copper conductors to
connect the 3-phase power supply to the unit.
CAUTION
Use Copper Conductors Only!
Unit terminals are not designed to accept other types of
conductors. Failure to use copper conductors may re-
sult in equipment damage.
Main Power Wiring
1. Table 6 lists the electrical data. The electrical service must
be protected from over current and short circuit conditions
in accordance with NEC requirements. Protection devices
must be sized according to the electrical data on the
nameplate. Refer to Figure 9 for determining:
a. The appropriate electrical service wire size based on
"Minimum Circuit Ampacity" (MCA),
b. The "Maximum Over current Protection" (MOP)
device.
c. The "Recommended Dual Element fuse size" (RDE).
2. If the unit is not equipped with an optional factory installed
Nonfused disconnect switch, a field supplied disconnect
switch must be installed at or near the unit in accordance
with the National Electrical Code (NEC latest edition). Re-
fer to Figure 9, DSS calculations, for determining correct
size.
Location for the electrical service entrance is shown in Fig-
ure 1. Complete the unit's power wiring connections onto ei-
ther the main terminal block HTB1, or the factory mounted
nonfused disconnect switch inside the unit control panel.
Note: Any electrical entrance holes drilled into the base of
the unit when a thru-the-base option is not used, is the re-
sponsibility of the installing contractor to prevent water from
leaking into the building.
3. Provide proper grounding for the unit in accordance with
local and national codes.
Thru-the-Base Electrical
(Optional Accessory)
Liquid-tite conduit couplings are secured to the base of the
unit for both power and control wiring. Liquid-tite conduit
must be field installed between the couplings and the unit
control box to prevent water leaks into the building.
If the unit is set on the roofcurb and temporary
auxiliary heat is provided in the building, it is
recommended that the electrical and control wiring
conduit opening in the control box be temporarily
sealed to provide a vapor barrier.
Содержание Voyager RT-SVX17C-EN
Страница 8: ...8 Figure 1 Unit Dimensions for TC_ TE_ and YC_330 360 and 420 MBH Units Low Heat ...
Страница 9: ...9 Figure 1 continued Unit Dimensions for YC_330 360 and 420 MBH Units High Heat ...
Страница 10: ...10 Figure 1 continued Unit Dimensions for TC_ TE_ and YC_480 and 600 MBH Units Low High Heat ...
Страница 24: ...24 Figure 10 Typical FieldWiring Requirements for CV Control Options ...
Страница 78: ......
Страница 79: ......
Страница 80: ......