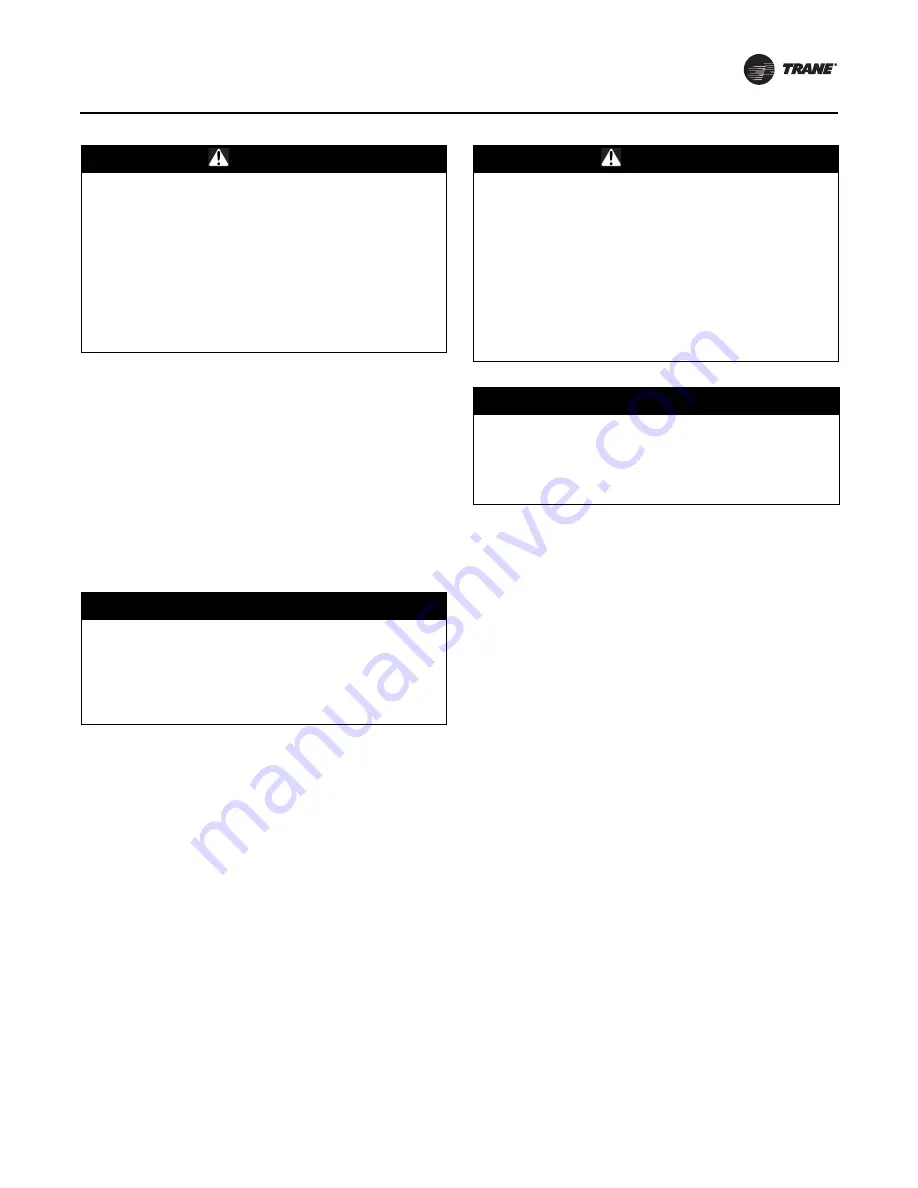
WARNING
Hazardous Pressures!
Failure to properly regulate pressure could result in a
violent explosion, which could result in death or serious
injury or equipment or property-only-damage. When
using dry nitrogen cylinders for pressurizing units for
leak testing, always provide a pressure regulator on the
cylinder to prevent excessively high unit pressures.
Never pressurize unit above the maximum
recommended unit test pressure as specified in
applicable unit literature. See maximum recommended
unit test pressure below.
Removal and Installation
PART-SVN234B-EN
27
Pressure Testing
•
Use industry-standard and EPA-accepted techniques
for testing.
•
Pressure tests must be performed by qualified
personnel.
•
Use tools especially designed for leak testing.
•
Do not exceed the high-side and low-side pressures
listed on the unit nameplate.
•
If no test pressure value is listed on the nameplate of
the unit, a pressure of no more than 150 psig is
acceptable.
NOTICE
Overpressure Damage!
Failure to follow these instructions could result in
compressor damage. Do not pressurize the low side of
the compressor by more than 5 bar (72 psig) higher
than the high side of the compressor within less than
two minutes.
•
The 182–361 nominal capacity compressor has an
internal check valve. When pressurizing the system, it
is important to never allow the low side pressure to
exceed the high side pressure by more than 5 bar
(72 psig). Greater pressure differential could result in
compressor damage. Also slowly raise the pressure
over a 2-minute time period to allow sufficient time for
internal pressures in the compressor to equalize.
•
Pressure decay testing can be used to check for gross
leaks but will not be able to detect the location of a leak.
•
After pressurizing the system use an R-410A leak
detection device to detect and locate leaks.
Vacuum Testing and Evacuation
•
Use the procedure as described in the unit
Installation,
Operation, and Maintenance
manual.
•
If no other information is available, use the following
information.
WARNING
Hazardous Voltage w/Capacitors!
Failure to disconnect power and discharge capacitors
before servicing could result in death or serious injury.
Disconnect all electric power, including remote
disconnects and discharge all motor start/run
capacitors before servicing. Follow proper lockout/
tagout procedures to ensure the power cannot be
inadvertently energized. Verify with an appropriate
voltmeter that all capacitors have discharged.
For additional information regarding the safe discharge
of capacitors, see PROD-SVB06*-EN.
NOTICE
Compressor Motor Damage!
Failure to follow instructions below could cause
compressor motor damage. Never use the compressor
as a vacuum pump. Never meg-ohm test or apply
power to the compressor while it is in a vacuum.
•
Ensure that there is no voltage being applied to the
compressor terminals.
•
Evacuate the unit to 500 microns.
•
Hold vacuum for 30 minutes.
•
Rapid pressure rise indicates a leak; locate and repair
the leak.
•
Slow pressure rise indicates one of two possibilities:
– A small leak, indicated by a continuous rise in
pressure.
– Moisture in the system, indicated by a slow rise in
pressure and leveling-out at a pressure equivalent
to the moisture level. If this occurs, break the
vacuum with dry nitrogen and repeat evacuation
process to 500 micron.
•
Once system is leak-tight, connect compressor repeat
the vacuum procedure, break vacuum with dry
nitrogen and evacuate to 500 microns. The vacuum
should be able to be maintained for four hours. Isolate
the vacuum pump so that the vacuum gauge only
reads the system pressure.
•
Vacuum must be measured in the refrigeration system
and not at the vacuum pump.