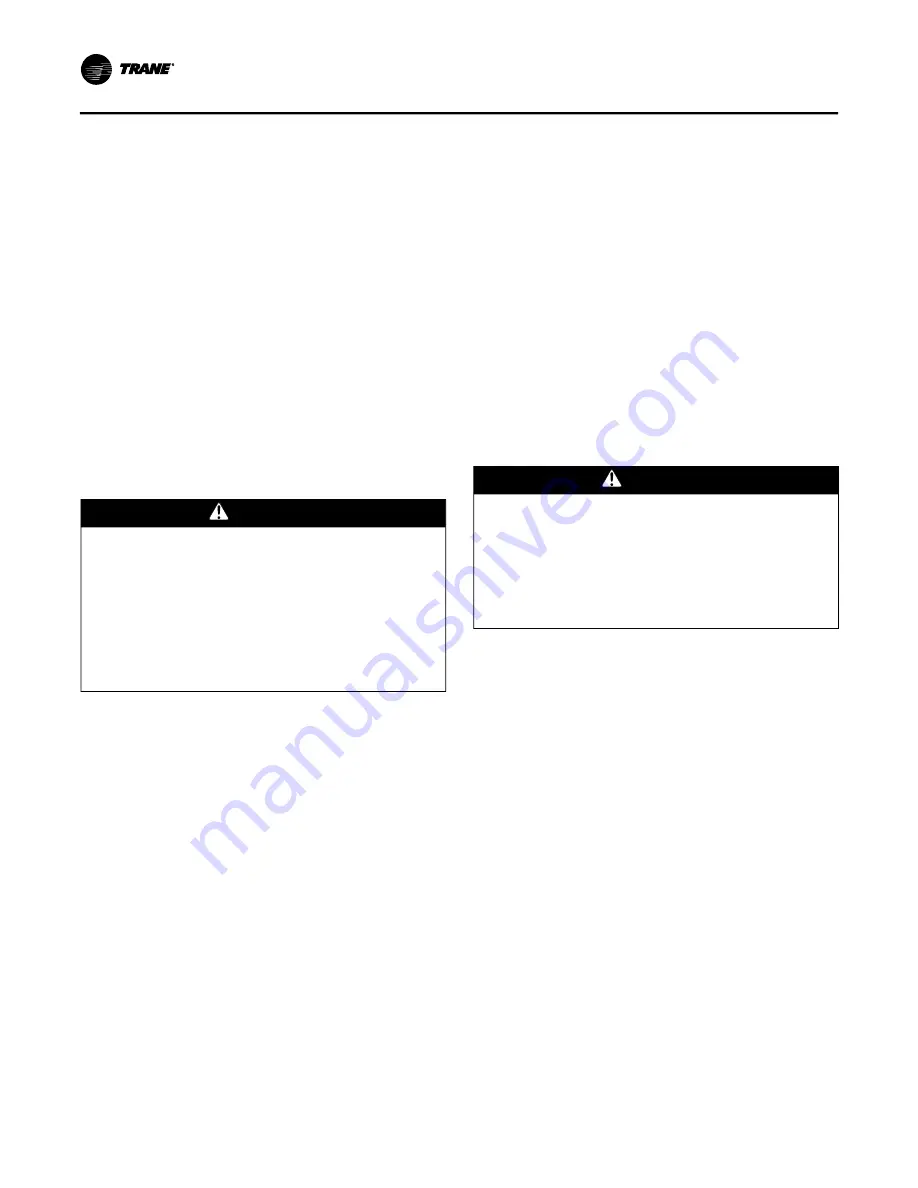
System Start-up
78
RT-SVX35H-EN
4. Open the Human Interface access door, located in the
unit control panel, and press the SERVICE MODE key to
display the first service screen. Refer to the latest
edition of RT-SVP04*-EN (VAV), RT-SVP05*-EN (CV) for
the SERVICE TEST screens and programming
instructions.
5. Use
to program the following system
components for operation by scrolling through the
displays;
•
Supply Fan
•
Variable Frequency Drive (100% Output, if
applicable)
•
RTM Occ/Unocc Output (Unoccupied)
6. Once the configuration for the components is
complete, press the NEXT key until the LCD displays
the “Start test in __Sec.” screen. Press the + key to
designate the delay before the test is to start. This
service test will begin after the TEST START key is
pressed and the delay designated in this step has
elapsed. Press the ENTER key to confirm this choice.
7. Press the TEST START key to start the test. Remember
that the delay designated in the previous step must
elapse before the fan will begin to operate.
8. With the VFD at 100% and the supply fan operating at
full airflow capability, measure the amperage at the
supply fan contactor 1K16 & 1K15. If the amperage
exceeds the motor nameplate value, the static
pressure is less than design and the airflow is too high.
If the amperage is below the motor nameplate value,
static pressure may be too high and cfm may be too
low. To determine the actual cfm (± 5%);
a. Measure the actual fan rpm
b. Calculate the Theoretical bhp
Actual Motor Amps X Motor hp
Motor Nameplate Amps
c. Plot this data onto the appropriate Fan Performance
Curve in
. Where
the two points intersect, read straight down to the
cfm line.
Use this data to assist in calculating a new fan drive if the
cfm is not at design specifications. An alternate method
with less accuracy is to measure the static pressure drop
across the evaporator coil. This can be accomplished by;
a. Drilling a small hole through the unit casing on each
side of the coil. Coil damage can occur if care is not
taken when drilling holes in this area.
b. Measure the difference between the pressures at
both locations.
c. Plot this value onto the appropriate pressure drop
. Use the data in
Table 22, p. 101
- (Component Static Pressure
Drops) to assist in calculating a new fan drive if the
cfm is not at design specifications.
d. Plug the holes after the proper cfm has been
established.
9. Press the STOP key at the Human Interface Module in
the unit control panel to stop the fan operation.
Exhaust Airflow Measurement (Optional
with all Units)
.
1. Close the disconnect switch or circuit protector switch
that provides the supply power to the unit's terminal
block 1TB1 or the unit mounted disconnect switch
1S14.
2. Turn the 115 volt control circuit switch 1S1 and the 24
volt control circuit switch 1S70 to the "On" position.
3. Open the Human Interface access door, located in the
unit control panel, and press the SERVICE MODE key to
display the first service screen. Refer to the latest
edition of RT-SVP04*-EN (VAV) or RT-SVN05*-EN (CV)
for the SERVICE TEST screens and programming
instructions.
4. Use
to program the following system
components for operation by scrolling through the
displays;
•
Exhaust Fan
•
Exhaust Dampers (100% Open, if applicable)
•
Fresh Air dampers (100% Open)
•
Variable Frequency Drive (100%, if applicable)
•
RTM Occ/Unocc Output (Default)
5. Once the configuration for the components is
complete, press the NEXT key until the LCD displays
the “Start test in __Sec.” screen. Press the + key to
designate the delay before the test is to start. This
service test will begin after the TEST START key is
pressed and the delay designated in this step has
elapsed. Press the ENTER key to confirm this choice.
WARNING
Rotating Components!
During installation, testing, servicing and
troubleshooting of this product it may be necessary to
work with live and exposed rotating components. Have
a qualified or licensed service individual who has been
properly trained in handling exposed rotating
components, perform these tasks. Failure to follow all
safety precautions could result in rotating components
cutting and slashing technician which could result in
death or serious injury.
WARNING
Hazardous Voltage!
HIGH VOLTAGE IS PRESENT AT TERMINAL BLOCK 1TB1
OR UNIT DISCONNECT SWITCH 1S14. Disconnect all
electric power, including remote disconnects before
servicing. Follow proper lockout/tagout procedures to
ensure the power can not be inadvertently energized.
Failure to disconnect power before servicing could
result in death or serious injury.
Содержание IntelliPak WEHE Series
Страница 15: ...General Information RT SVX35H EN 15 Figure 1 Unit component layout and ship with locations...
Страница 17: ...Installation RT SVX35H EN 17 Figure 2 Typical control module location...
Страница 29: ...Installation RT SVX35H EN 29 Figure 10 Unit rigging Figure 11 Typical unit base roof curb cross section...
Страница 44: ...Installation 44 RT SVX35H EN Figure 27 Typical field power wiring for W_HE casings 2 through 6...
Страница 56: ...Installation 56 RT SVX35H EN Figure 32 Wiring notes for CV controls...
Страница 60: ...Installation 60 RT SVX35H EN Figure 35 Wiring notes VAV...
Страница 68: ...System Start up 68 RT SVX35H EN Figure 38 Typical fenwall ignition control system...
Страница 69: ...System Start up RT SVX35H EN 69 Figure 39 Typical Fenwall ignition control system...
Страница 70: ...System Start up 70 RT SVX35H EN Figure 40 Typical modulating gas heat schematic connections diagram...
Страница 101: ...Service Maintenance 100 RT SVX35H EN Figure 55 Unit internal fuse replacement data for air cooled units...
Страница 108: ...Service Maintenance RT SVX35H EN 107 Figure 59 Typical wiring schematic for air handler with DX coil casing 2 9...