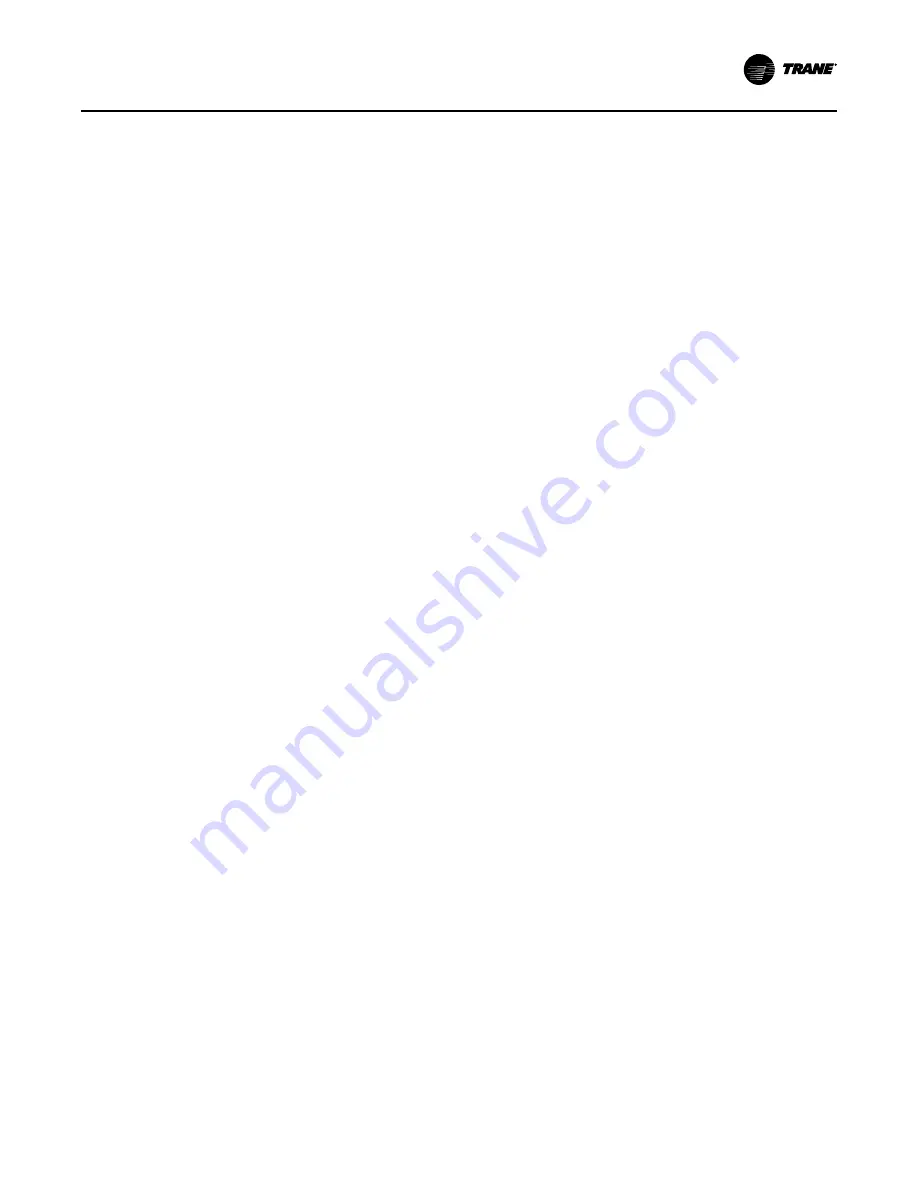
CVHH-SVX001G-EN
81
Oil supply to both the thrust bearing and journal
bearings is cooled when the oil tank temperature
reaches 140°F (60.0°C). The supply oil and liquid
refrigerant are pumped to a brazed plate heat
exchanger. The unit controller monitors oil tank
temperature and opens a solenoid valve to allow liquid
refrigerant to flow into the heat exchanger.
Motor Cooling System
Compressor motors are cooled with liquid refrigerant
(refer to the figure in
). The refrigerant pump is located on the
front of the oil tank (motor inside the oil tank). The
refrigerant pump inlet is connected to the well at the
bottom of the condenser. The well design ensures
preferential supply of liquid refrigerant to the
refrigerant pump before refrigerant is supplied to the
economizer. Refrigerant is delivered to the motor via
the pump. An in-line filter is installed (replace the in-
line filter only with major service). Motor refrigerant
drain lines are routed to the condenser.
Tracer AdaptiView Display
Information is tailored to operators, service
technicians, and owners.
When operating a chiller, there is specific information
you need on a day-to-day basis—setpoints, limits,
diagnostic information, and reports.
Day-to-day operational information is presented at the
display. Logically organized groups of information—
chiller modes of operation, active diagnostics, settings,
and reports put information conveniently at your
fingertips. For more information, refer to
Tracer
AdaptiView Display for Water-Cooled CenTraVac
Chillers Operations Guide
(CTV-SVU01*-EN).
RuptureGuard
Operation
The rupture disk monitors the pressure inside the
chiller. If the pressure exceeds the disk’s burst setting,
the disk ruptures, allowing the chiller pressure to enter
the valve holder compartment upstream of the relief
valve. If the pressure is above the pressure setting of
the relief valve, the valve will open, allowing only the
amount of refrigerant to escape to keep the pressure
within safe operating limits.
The excess flow valve maintains the downstream side
of the rupture disk at atmospheric pressure to assure
proper operating conditions for the disk. When the disk
bursts, the rapid pressure increase causes the excess
flow valve to seal and the valve holder area becomes
pressurized.
A disk rupture will be indicated by a pressure reading
on the gauge and the pressure switch contacts will
close. The pressure switch is an optional accessory and
does not wire to the control panel. The pressure switch
can be connected to a customer-supplied building
automation system (BAS).
EarthWise Purge
General Information
Centrifugal chillers that use low-pressure refrigerants,
such as R-1233zd, operate with areas of the chiller at
less than atmospheric pressure. Non-condensables in
the air, such as water and nitrogen vapor, may leak into
these low-pressure areas and accumulate in the
condenser. If these non-condensables are not
removed, the condenser loses its ability to condense
refrigerant efficiently and the pressure of the
condenser increases. Increased condenser pressure
lowers the chiller’s efficiency and capacity.
A purge system is required on low-pressure centrifugal
chillers. It is a device that is externally mounted on the
chiller. Its purpose is to remove non-condensable
materials that have leaked into the machine.
N
No
otte
e:: For convenience, the term “air” is often used in
describing non-condensables removed by the
purge system, although any other non-
condensable materials that may exist in the
chiller are also removed by the purge system.
How a Purge System Works
From a functional standpoint, the purge system can be
divided into subsystems of components. This section
identifies and describes the function of these
subsystems.
Refrigeration Circuit Subsystem
The purge evaporator of the refrigeration circuit is
located in the purge tank. The purge tank is connected
to the chiller condenser by supply and return lines
through which chiller refrigerant can freely flow.
The purge evaporator coil presents a cold condensing
surface to the chiller refrigerant entering the purge
tank. When the purge refrigeration system is running,
refrigerant from the chiller condenser is attracted to the
cold surface of the purge evaporator. When the
gaseous refrigerant contacts the surface of the purge
evaporator coil, it condenses into a liquid, leaving a
partial vacuum behind. More refrigerant vapor from the
chiller condenser migrates to the purge tank to fill the
vacuum.
The liquid refrigerant that has condensed in the purge
tank returns to the chiller condenser through the liquid
return line. The return line includes a filter-drier and a
moisture-indicating sight glass.
The condensing unit is air-cooled and is operable
whether the chiller is running or not. No additional
cooling source is required.
Содержание CVHH CenTraVac
Страница 126: ...126 CVHH SVX001G EN N No ot te es s ...
Страница 127: ...CVHH SVX001G EN 127 N No ot te es s ...