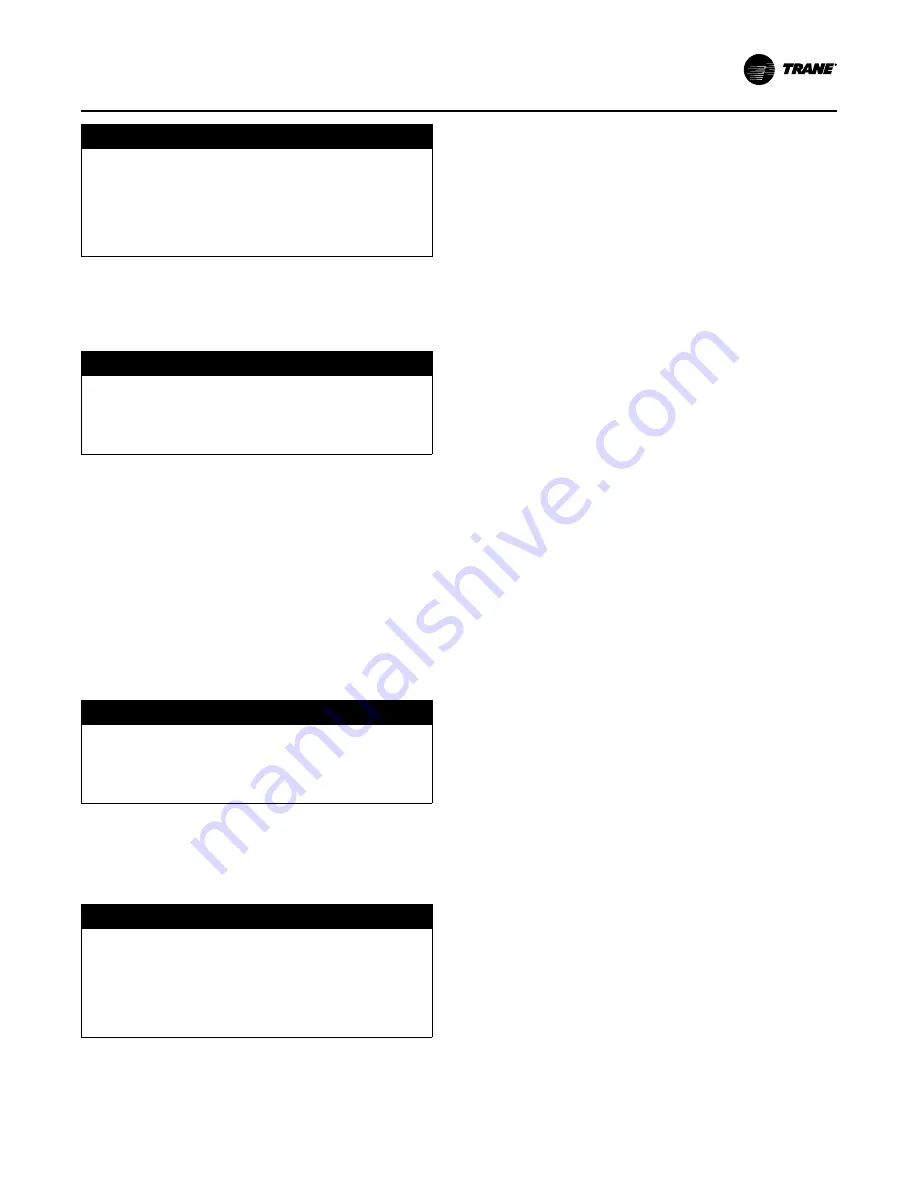
ARTC-SVX006A-EN
49
NOTICE
Equipment Damage!
Failure to remove moisture from system could cause
corrosion within the chiller/heater components, and
degrade performance.
Perform vacuum evacuation of system to remove
moisture.
4. When the compressor is not operating, the oil level
should be at least at the bottom of the sight glass, up to
two-thirds full. When the compressor is operating, the
oil level will normally be at the bottom of the sight glass,
or even below, but it must be visible.
NOTICE
Compressor Failure!
Failure to follow instructions below could result in
catastrophic compressor failure.
Do not operate with insufficient oil.
5. Low oil sight glass conditions could signify an
undercharged heat pump that lacks proper refrigerant
velocity to return oil to the compressor sump.
Eventually, dry compressor starts could occur causing
premature compressor failure. This may indicate that
some oil has been lost from a previous refrigerant leak
repair. The compressor data label indicates the correct
oil type and quantity with which it should be filled.
Note:
A flashlight may be required to see the oil churning in
the sump of the compressor. Adjusting the line of
sight may be necessary to visually inspect the oil in
the compressor sump during operation. At a
minimum, the oil must be seen churning in the
compressor sump. It should be clear.
NOTICE
Compressor Failure!
Failure to follow instructions below could result in
catastrophic compressor failure.
Do not operate with insufficient oil.
6. Check the glycol concentration using a refractometer.
7. Check the refrigeration pressures. For R410A
refrigerant, low pressure refrigeration gauge should
read 120 to 160 psi and high pressure refrigeration
gauge should read 300 to 450 psi.
NOTICE
Compressor Damage!
Failure to follow instructions below could result in
extensive compressor damage.
Verify that suction pressure is sufficient. Secure the
circuit or module offline until status can be examined
in detail.
Important:
Extended operation with suction pressures
below 80 psi is a clear sign of insufficient
refrigerant charge, refrigeration obstruction, or
valve closed. This can cause extensive
damage to a compressor.
8. Check the refrigeration liquid line sight glass for
persistent bubbles (“flashing”) .
Note:
Bubbles in the sight glass do not necessarily indicate
loss or lack of refrigerant charge. Bubbles
(commonly know as “flashing”) will occur whenever
the condenser fans cycle until the expansion valve
settles out the refrigerant flow. Occasional bubbles
also form when the condenser head pressure
control valve bypasses hot gas around the
condenser coil in low ambient operation. If the
refrigeration pressures are in the normal range, the
unit is most likely adequately charged. “Flashing”
could also indicate excessive superheat adjustment
of the thermal expansion valve.
Quarterly
The quarterly maintenance inspection is a comprehensive
event that examines all aspects of the heat pump to identify
early problems before they can damage a Heat Pump and
require major repair or refurbishment:
1. Inspect alarm log, refrigerant operating/static pressures
and temperature set points of each module
independently.
2. Inspect heat pump superheat and sub-cooling. System
superheat should be 10 °F to 12 °F (5 °C to 6 °C).
System sub-cooling should be 10+ °F (5 °C) depending
on the ambient conditions.
3.
Inspect the approach delta T - entering heat exchanger
water/glycol mixture temperature and leaving
refrigerant temperature.
4. Inspect strainers. Ensure bypass valve is properly
adjusted to a minimum of 25% open position.
5. Collect chilled water/glycol mixture sample for
professional analysis. Check for cleanliness. Drain and
refill with clean solution if excessive sludge or dirt is
present. Flush the heat pump prior to refilling.
6. Inspect water/glycol mixture levels. Add glycol as
required.
7. If equipped, inspect crankcase heaters for proper
operation.
8. Inspect the water piping for signs of leaks at joints and
fittings.
9. Inspect refrigerant piping circuit for signs of oil or
refrigerant leakage. Conduct “sniffer test” to find
refrigerant leaks. Inspect all pressure switch bellows.
10. Tighten all refrigeration piping connections (e.g.
rotalocks , Schrader valves, caps, and ball valves).
11. Install a manifold and gauge set to observe heat
pump’s refrigeration operating pressures.
Содержание Arctic Thermafit AXM
Страница 69: ...ARTC SVX006A EN 69 Notes...
Страница 70: ...70 ARTC SVX006A EN Notes...
Страница 71: ...ARTC SVX006A EN 71 Notes...