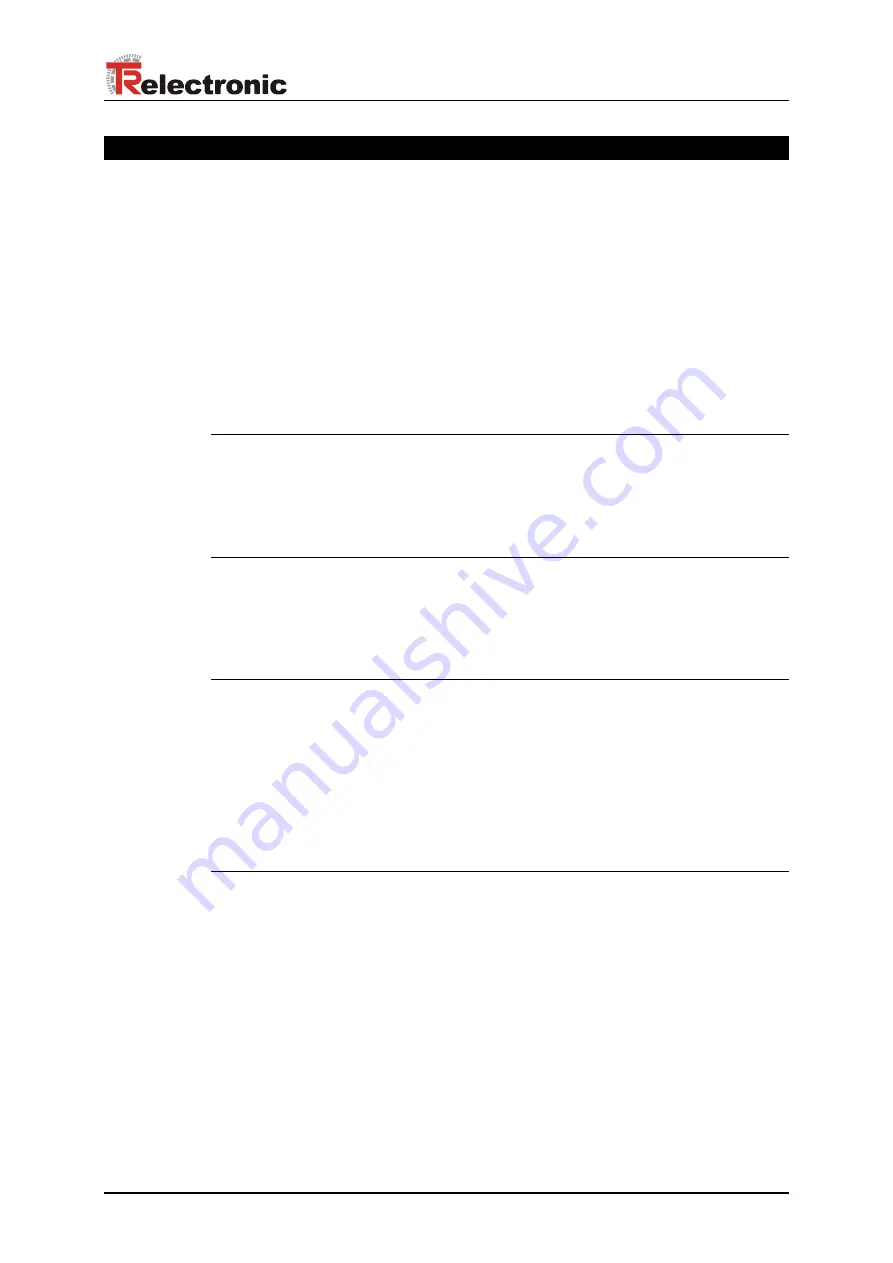
CAN DeviceNet information
Printed in the Federal Republic of Germany
©
TR-Electronic GmbH 1998, All Rights Reserved
03/09/2010
TR - ECE - BA - GB - 0014 - 03
Page 11 of 31
4 CAN DeviceNet information
DeviceNet
™
was developed by Rockwell Automation and the ODVA as an open field
bus standard, based on the CAN protocol and is standardized in the European
standard EN 50325. Specification and maintenance of the DeviceNet standard is
regulated by the ODVA. DeviceNet
™
, along with ControlNet and EtherNet/IP, belongs
to the family of CIP-based networks. The CIP (Common Industrial Protocol) forms a
common application layer for these 3 industrial networks. DeviceNet
™
, ControlNet and
Ethernet/IP are therefore well matched to one another and present the user with a
graduated communication system for the physical layer (Ethernet/IP), cell layer
(ControlNet) and field layer (DeviceNet
™
). DeviceNet
™
is an object-oriented bus
system and works according to the producer/consumer model.
DeviceNet
™
Protocol
The DeviceNet
™
protocol is an object-oriented protocol. It is typically used for networking
sensors and actuators with the superordinate automation devices (PLC, IPC).
DeviceNet
™
Data Link Layer
Layer 2 (Data Link Layer) is based on the Controller Area Network (CAN), which was
originally designed for use in motor vehicles.
DeviceNet
™
Network and Data Transport Layer
The link is set up with the Group 2 Unconnected Port. Selected CAN identifiers are
used for the link set-up. A link, once set up, can be used for transmitting explicit
messages or for setting up additional I/O links. As soon as an I/O link has been set up,
I/O data can be exchanged between the DeviceNet
™
users. The 11 bit identifier is
used exclusively for coding I/O data. The 8-byte wide CAN data field is fully available
for user data.
DeviceNet
™
Application Layer – CIP Protocol
The CIP (Common Industrial Protocol) forms the application layer for DeviceNet
™
.
The CIP defines the exchange of I/O data in realtime via I/O messages (I/O
messaging or implicit messaging), as well as the exchange of data required for
configuration, diagnosis and management via explicit messages (explicit messaging).
The communication between two devices always takes place according to a
connection-oriented communication model, either via a point-to-point or a multicast-V1
connection. This allows both master/slave and multi-master systems to be realized.
Data are known as objects and are logged in the object directory of each device.