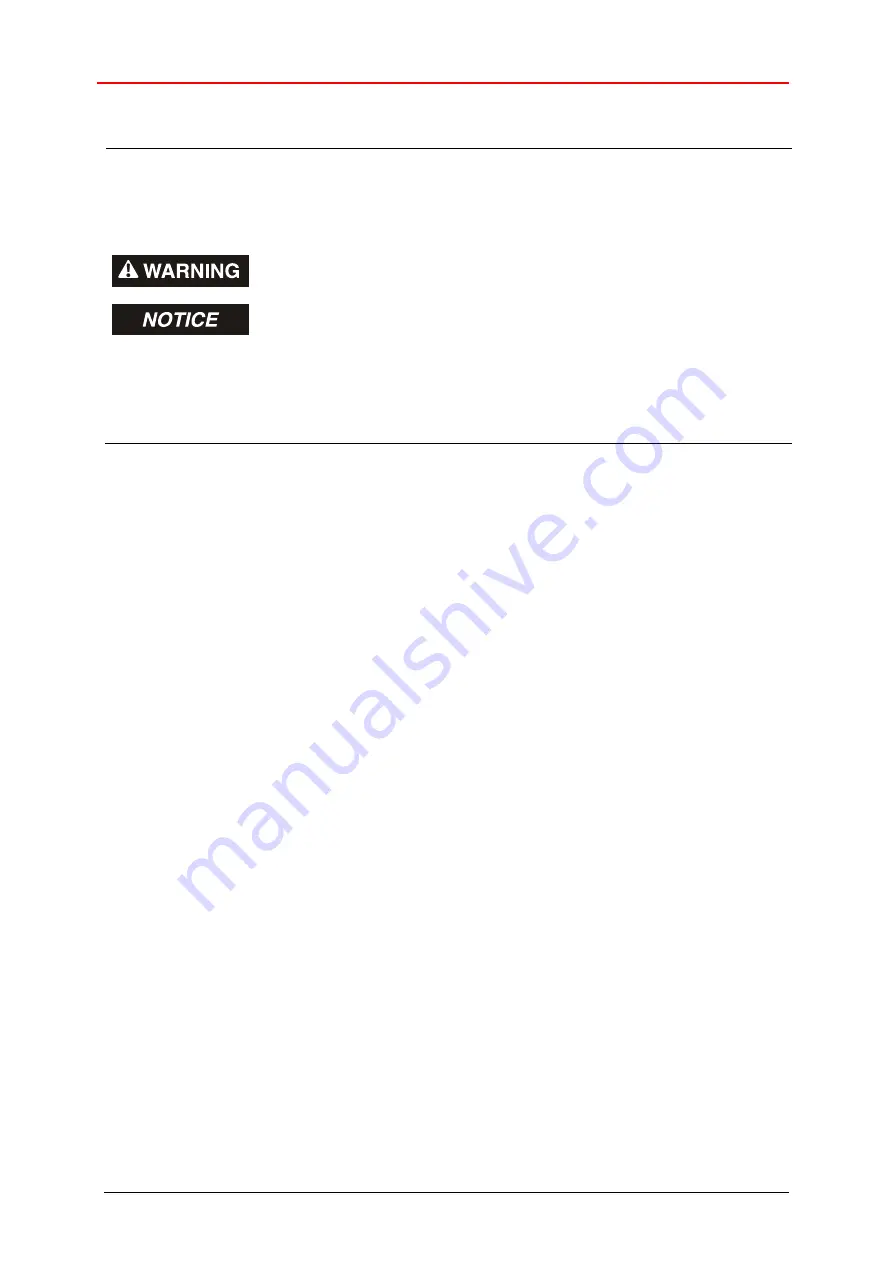
TR Safety – Preset Adjustment Function
TR-Electronic GmbH 2020, All Rights Reserved
Printed in the Federal Republic of Germany
Page 74 of 91
TR-ECE-BA-GB-0163 v03
10/07/2020
10 TR Safety – Preset Adjustment Function
Risk of death, serious physical injury and/or damage to property if the
drive system starts uncontrolled while executing the Preset Adjustment
function!
The relevant drive systems must be locked to prevent automatic
start-up
Use the Originator to protect the preset adjustment function from being
triggered by taking additional safety measures, such as key-operated
switches, passwords, etc.
You must follow the operational sequence described below and the
Originator must evaluate the status bits to verify whether the preset
adjustment function has been executed successfully or unsuccessfully
Ensure the settings are made for the correct axis
Verify the new position on the relevant axis after executing the preset
function
The preset adjustment function is used to set the currently output actual position value to any actual
position value within the scaled measuring range. This allows setting the displayed position to a
machine reference position electronically.
10.1 Procedure
Requirement: The measuring system is in Cyclical Data Exchange mode.
Set the
Preset
register in the source data of the safety-related submodule to the desired preset
value.
Set the control bits
Preset Preparation
and
Preset Request
to 0.
Set the
Preset Preparation
control bit to 1. In response, the
Safe State
status bit is set to
0, whereupon the Originator must transfer the system to the safe state. The output actual position
value is no longer safe!
A rising edge of the
Preset Request
control bit applies the preset value. Receipt of the preset
value is acknowledged by setting (= 1) the
Preset Active
status bit. Once execution of the
preset function has been completed, the
Preset Active
status bit is reset to 0.
After receipt of the preset value, the measuring system checks whether all prerequisites for
execution of the preset adjustment function are fulfilled. If yes, the preset value is written as the
new actual position value. If no, execution is rejected and an error message is output by setting
the
Preset Error
status bit.
After successful execution of the preset adjustment function, the measuring system sets the
Preset OK
status bit to 1, thus signaling to the Originator that execution of the preset
adjustment function has been completed.
Reset the
Preset Request
control bit to 0.
Reset the
Preset Preparation
control bit to 0. In response, the
Safe State
status bit is set
to 1 again.
Finally, the Originator must verify that the new position corresponds to the new target position.