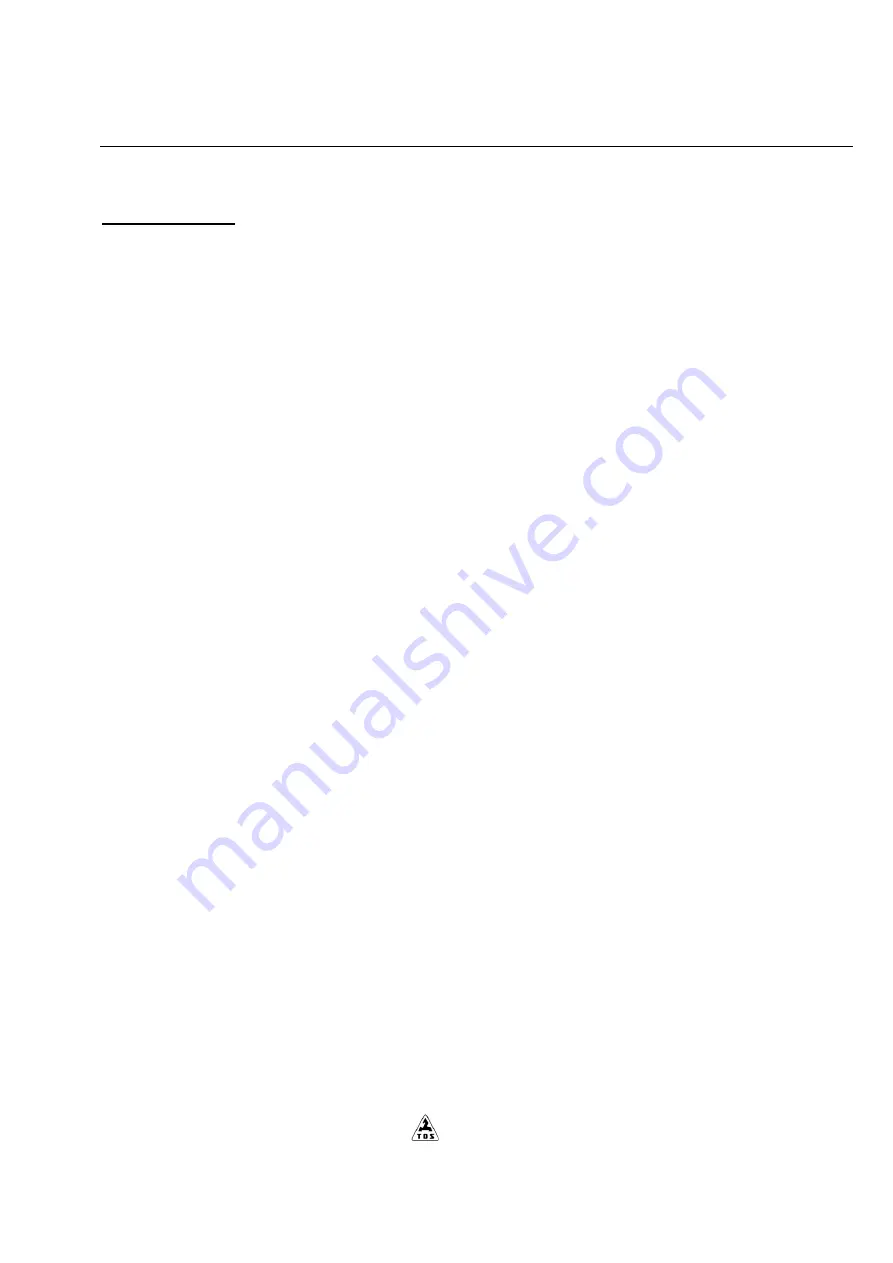
SUA 125 NUMERIC
34200003
TOS a.s. 02/2011
69
Main Electric Motor
Greasing in prescribed intervals in accordance with the lubrication chart.
Warning:
1. Before every fresh feeling the oil tank should be thoroughly cleaned and flushed with benzol or with special flushing oil.
It is recommended to clean the entire lathe well once a year and remove impurities, dust and traces of old oil which have
settled and dried on it.
2. For cleaning of the guiding surfaces, bearings and other functional parts it is recommended to use a special cleaning oil.
Kerosene or similar acidly seacting substances are not recommended.
3. When the lathe is beeing run in the increased attention must be paid to lubrication.
It is recommended for a new machine to change oil for the first time already after the first month.
A summary of the most important lubricating points is shown in the lubricating instructions.
4. Filling of the hydraulic set with oil should be done when the lathe is out of operation after the circulating flow of oil has
returned to the main oil tank. The oil level should be seen in the oil level indicator.
5. It is recommended to check the oil filter (min. once a month) with its eventual cleaning relative to the actual load of the
lathe.
5.2.12.
Cutting lubricant circuit.
Cooling of cutting process.
The cooling of cutting process is assured by means of electric pump type COA with one - stage centrifugal pump which is
connected with electric motor in one unit. The pump is submerged into tank of cutting liquid with volume 160 liters which
is a part of swarf pan.
The used liquid returns from the sieve to the tank. The pump start is realized by means of push button which is situated on
the operating board or can be carrved out by program.
The cutting liquid coolant is supplied by an flexibel hose to the body of saddle and by flexibel hose to the tool post. In this
tool post is distributed into four positions.
For orientation of cutting liquid flow serves the endpiece and the rotary closing valve serves for adjusting of delovered
liquid quantity.
ATTENTION:
when machining with cutting liquid (coolant) the protection guards against splash of coolant must be used.
Handle with cutting liquid acc. to instructions of manufacturer and keep the internal prescriptions for liquid replace, storing
and liquidation.
Recomended cutting liquid:
Blasocut UNI 2000 no. 870, manufacturer: Co. AG. Switzerland.
Содержание SUA 125 NUMERIC
Страница 27: ...SUA 125 NUMERIC 34200003 TOS a s 02 2011 27 Protection IP code IP 54 Interference elimination level 3...
Страница 39: ...SUA 125 NUMERIC 34200003 TOS a s 02 2011 39...
Страница 41: ...SUA 125 NUMERIC 34200003 TOS a s 02 2011 41...
Страница 43: ...SUA 125 NUMERIC 34200003 TOS a s 02 2011 43 5 2 3 Brake Fig 5 2 Fig 5 2 6...
Страница 46: ...SUA 125 NUMERIC 34200003 TOS a s 02 2011 46...
Страница 48: ...SUA 125 NUMERIC 34200003 TOS a s 02 2011 48 5 2 6 Work spindle Fig 5 4...
Страница 57: ...SUA 125 NUMERIC 34200003 TOS a s 02 2011 57...
Страница 63: ...SUA 125 NUMERIC 34200003 TOS a s 02 2011 63 Hydraulic chart...
Страница 64: ...SUA 125 NUMERIC 34200003 TOS a s 02 2011 64...
Страница 68: ...SUA 125 NUMERIC 34200003 TOS a s 02 2011 68 Fig 5 8...
Страница 70: ...SUA 125 NUMERIC 34200003 TOS a s 02 2011 70...
Страница 75: ...SUA 125 NUMERIC 34200003 TOS a s 02 2011 75...
Страница 93: ...SUA 125 NUMERIC 34200003 TOS a s 02 2011 93 Fig A transport locking...
Страница 95: ...SUA 125 NUMERIC 34200003 TOS a s 02 2011 95...
Страница 109: ...SUA 125 NUMERIC 34200003 TOS a s 02 2011 109 Fig B Working path length is 650 mm...
Страница 110: ...SUA 125 NUMERIC 34200003 TOS a s 02 2011 110 Longitudinal stops Fig C...