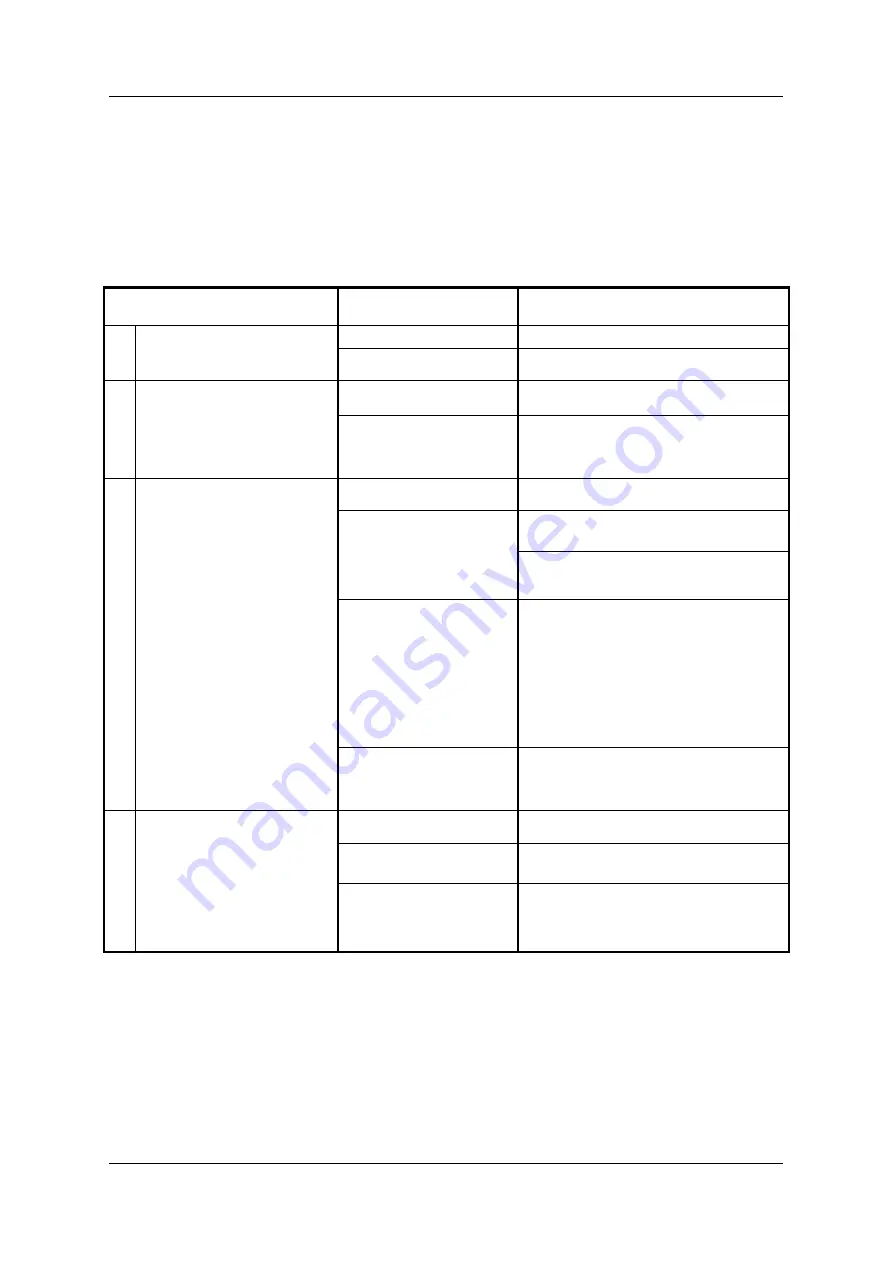
TORAY MBR
Instruction Manual
06-G-MB2-NHPAF-220801
61 of 63
X.
TROUBLESHOOTING
Most of the troubles in the operation of “NHPA Series” are related to poor membrane
scouring aeration, chemical cleaning delay, and inappropriate pretreatment. The following
table lists some performance losses, their causes, and possible countermeasures.
Table X-1 Troubleshooting
Problem
Cause
Action
1
The air diffusion flow is below
the required level.
The blower is broken.
Stop the filtration and inspect the blower.
The air diffusers are
clogged.
Clean the air diffusers.
2
The air diffusion is uneven in
the module or between
modules.
The air diffusers are
clogged.
Clean the air diffusers.
The bottom of the element
block is stuck with debris.
Check the pretreatment system.
Inspect the module.
Correct operation and maintenance work
of the pretreatment system.
3
The filtrate water flow rate has
decreased, or the
trans-membrane pressure has
increased.
Membrane clogging has
got severe.
Conduct chemical cleaning.
Sludge is accumulated on
the membrane surface
because of uneven air
diffusion
Inspect the blower and clean the air
diffusers to improve air diffusion.
Conduct chemical cleaning.
Remove sludge cake by external
cleaning.
Abnormal properties of
sludge have worsened its
filterability.
Improve sludge properties.
・
Adjust the excess sludge discharge
rate.
・
Prevent entry of abnormal
components, such as oils.
・
Adjust the BOD load and oxygen
supply.
・
Adjust the raw water quality (add
nitrogen, phosphorous, etc.)
Air is accumulated inside
filtrate piping.
Prime the filtrate piping with water.
Install air removal equipment such as
vacuum pump.
Relocate filtrate piping.
4
The concentration of
suspended solids in the filtrate
water has increased.
Element and/or tube has
been broken.
Seal the element and manifold nozzle
*1
.
Replace the cassette.
Leakage has occurred in
the filtrate water piping.
Inspect the faulty part
*2
and correct the
fault.
Germs are generated on
the membrane or the filtrate
line.
To clean the filtrate water piping, inject a
sodium hypochlorite solution with an
effective chlorine concentration of 100 to
200 mg/L.
*1: Even if a cause is found in the tube, there is still the possibility of contamination inside the element. Thus,
seal the element and manifold nozzle.
*2: To check the piping joints and welds for leakage with a pressure being applied, be careful not to apply
pressure to the membrane modules.