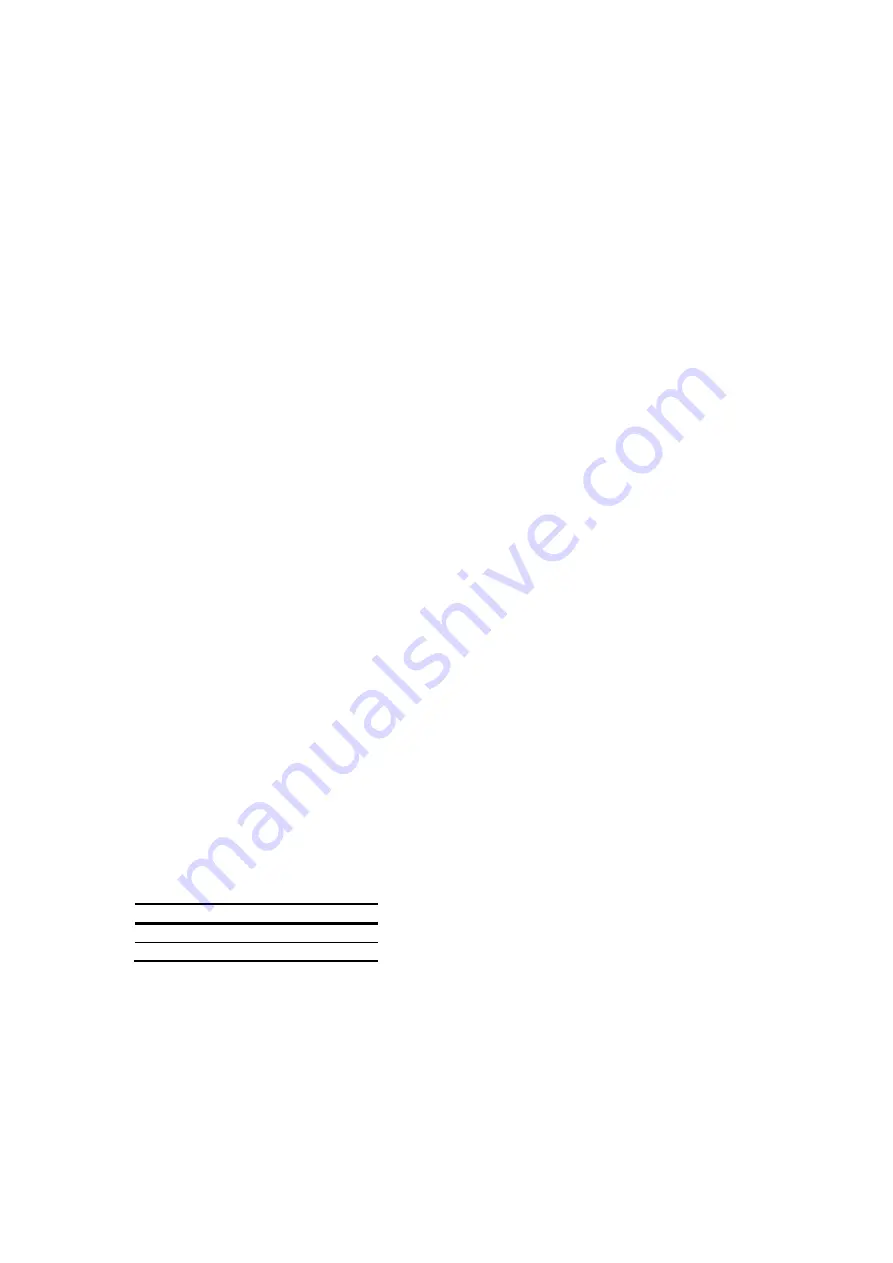
TM 9-1829A, April 1944
42/100
2021-07-07
e.
Install hair spring:
Turn speed cup counterclockwise to the stop and hold in this position during hair spring
assembly. Start hair spring on staff in proper position (so that spiral goes out from the center of the hair spring
counterclockwise, and with chamfered side of collet down). Make sure that hair spring, without any tension
on it, is in such a position that, when pressed down onto the staff, the outer end of the spring will just slip into
the lanced ear in the hair spring regulator, so as not to extend more than
1
/
8
inch or less than
1
/
16
, inch through
this ear. Carefully push hair spring down on the staff, using female punch (T-29 Det 2) until the coils of the
hair spring are level with the lanced ear in the regulator. Insert the end of the hair spring into the lanced ear.
Insert hair spring pin and tighten with pliers.
Caution: The tension of the hair spring should be such that it
brings the speed cup just back, against the stop, with the hair spring regulator at the lower edge of the jewel
bracket.
This provides full adjustment range. Straighten out the hair spring in flat plane, space coils evenly
with no coils touching each other or the regulator, in either the unwound (zero) or completely wound (top)
position.
f.
Install odometer assemblies:
Insert reset shaft into frame. Place trip odometer reset spring and drive gear
on shaft. Insert trip odometer into frame, making sure to place spacer feet in slot. Insert trip odometer thrust
washer into shaft inner groove next to frame (inside). Test reset operation. Place total odometer drive gear on
end of odometer shaft. Insert total odometer in upper set of holders, placing odometer roll legs in the slotted
retainer. Insert total odometer thrust washer in groove on shaft next to frame (inside). Check to ensure that
slight end play exists in odometer shaft. It is possible that frame ends may be bent together. There are two
types of frames -one with odometer shaft holes, the other with slots. The latter requires a wire odometer
holding clip. Check for free turning (par. 4b).
g.
Install dial and pointer:
Assemble dial to front jewel bracket with two screws and lock washers. Assemble
pointer to staff with fingers. Tighten on by turning counterclockwise until the pointer indicates zero with the
speed cup against the stop, pressing slightly downward. Check hair spring tension. If pointer returns too
sharply to zero, or too slowly, adjust hair spring with regulator. This tension should result in a float zero
setting (no bank) when pointer is released from 7 miles per hour and permitted to drop to zero.
Note: The
speedometer should now be calibrated before completing assembly (par. 27).
h.
Install case, bezel, etc:
To provide better weatherizing, paint inside of case around the hub hole with cement,
type B, joint and thread compound. Place mechanism in case, and assemble gasket and backing plate with
screws. Place reset washer (or washers) and spring on reset shaft and attach knob. (On flexible-reset type, if
the original reset ferrule has been removed, use a new one. With flexible conduit straight, pull reset shaft out
as far as it will come. Slip reset ferrule over conduit with end of threaded section 1 inch from the end of the
reset shaft. This brings the end of the ferrule midway between the two shoulders on the reset stem tip. Crimp
the ferrule onto the conduit with a blunt chisel and hammer.) Assemble gaskets, retainer, glass, and retainer
to case in order shown in figure 44. Roll bezel with special fixture (T-178730) and arbor press (figs. 74 and
75).
27. Calibration
a.
Place the speedometer on the calibrating machine and hold at the proper operating panel slope (standard
Quartermaster’s Corps Ordnance-30 degrees). Run master head at 60 miles per hour. The repaired
speedometer with a new (or recharged) magnet will overread considerably. Demagnetize carefully until unit
reads about 65 miles per hour (that is, approximately
1
/
4
inch beyond 60). Use special tool (846294) for
demagnetizing (refer to par. 9 e). Then check speed at 10 and 30 miles per hour. The master speedometer
service calibration limits are:
10 mph
30 mph
60 mph
+1
+2
+3
-1
-0
-0
The repaired speedometer should read proportionately high at 10 and 30 miles per hour, if hair spring
adjustment is correct. If not, move hair spring regulator up until desired proportionate calibration is reached.
Then carefully demagnetize further (at 60 miles per hour on master head) until the repaired unit reads within
limits. Caution: Do this demagnetizing very carefully, as it is extremely difficult to recharge magnets that
have been knocked down too far (par. 9 b). For further instructions refer to chapter 13.