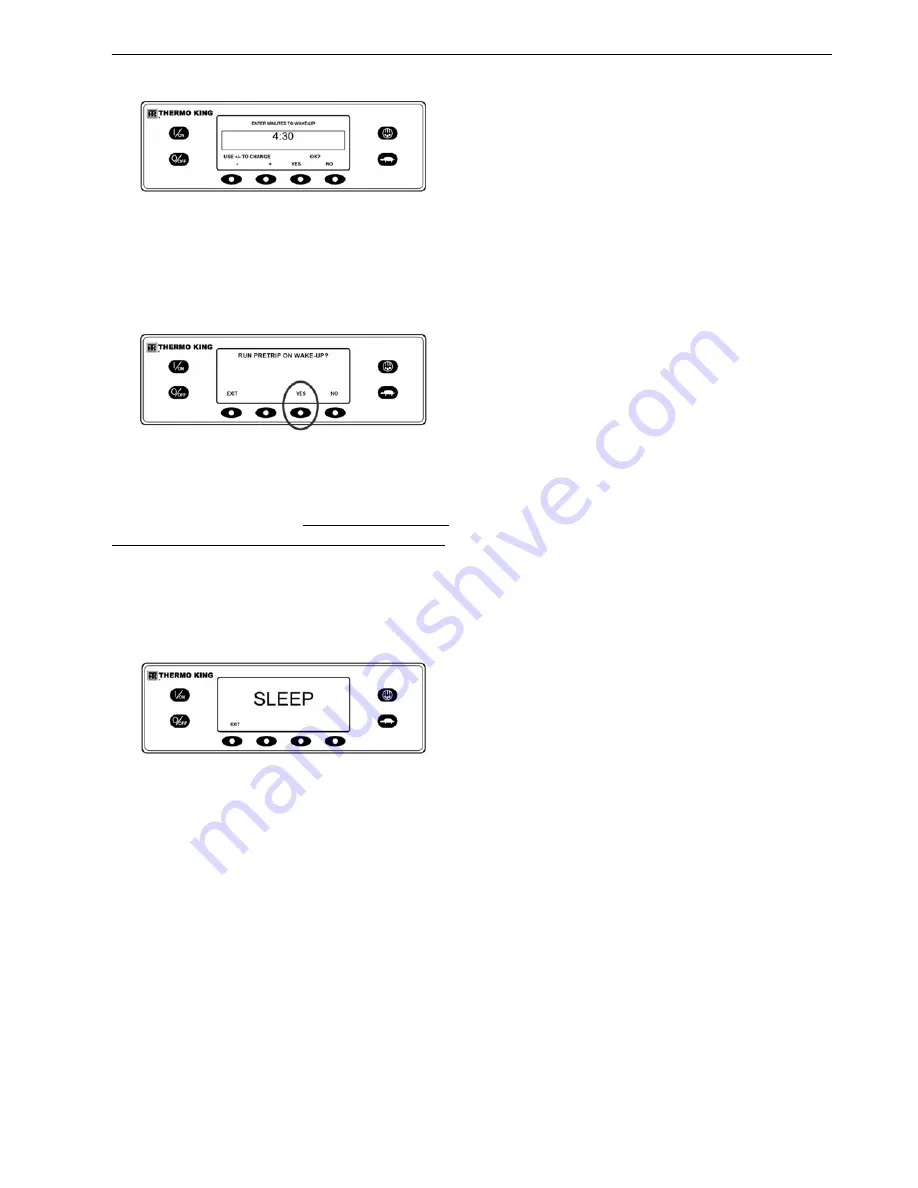
Operating Instructions for Premium HMI Control Panel
67
Figure 125: Confirm Minute
The display will now prompt for a Pretrip Test on
Wake-up. Press the YES key to perform a Pretrip
Test on Wake-up. If the No key is pressed the unit
will resume normal operation on Wake-up.
Figure 126: Press Yes Key for Pretrip Test
The display will show SLEEP and the unit will
start and stop as required to keep the engine warm
and/or the battery charged. Sleep mode does not
consider setpoint or maintain cargo temperatures.
NOTE: The unit may start when sleep is enabled
to bring battery charge level and engine
temperature up to minimum level. It will shut
down and then maintain minimum levels.
Figure 127: Sleep Mode
The unit will restart at the programmed time (in
this example 4:30 am) and perform a Pretrip Test
(if selected). After the Pretrip Test is complete the
test results will be displayed and the unit will
resume normal operation and control to setpoint.
To exit Sleep Mode before the selected Wake-up
time press the EXIT key or turn the unit off and
back on. The unit will resume normal operation
and control to setpoint.
Pretrip
A Pretrip Test verifies unit operation. This display
allows a Pretrip Test to be selected and initiated
by the operator. If the Pretrip Test is entered with
the unit shut down a Full Pretrip Test with device
amp checks will be performed. If the Pretrip Test
is entered with the unit running in either diesel or
electric mode a Running Pretrip Test is
performed, but the device amps checks are not
performed. Test results are reported as PASS,
CHECK or FAIL when the Pretrip Test is
completed. If an alarm occurs during a Pretrip
Test the alarm code will be displayed as Pretrip
Alarm XX, where XX is the alarm code.
Pretrip Test Conditions
•
Current unit settings are saved and restored at
the end of the Pretrip Test or if the unit is
turned off and back on.
•
Pretrip Test can be run in either Diesel or
Electric Mode.
•
The unit will auto switch from Diesel Mode to
Electric Mode or from Electric Mode to Diesel
Mode during a Pretrip Test if these features
are enabled and the auto switch conditions
occur.
Conditions where Pretrip Tests are not
allowed
•
If any shutdown alarms are present. Pretrip
tests are allowed with some Check and Log
alarms.
•
If the unit is in Sleep Mode.
•
If the unit is in Service Test Mode, Interface
Board Test Mode or Evacuation Mode.
Pretrip Test Sequence
Pretrip tests proceed in the order shown below. A
Full Pretrip Test includes all tests. A Running
Pretrip Test is started with the engine or motor
running and does not include the Amp Checks or
Engine Start Check.
•
Amp Checks - Each electrical control
component is energized and the current drawn
is confirmed as within specification.
•
Engine Start - The Engine will start
automatically.
•
Defrost - If the coil temperature is below 45 F
(7 C), a defrost cycle is initiated.
Содержание T-1080S
Страница 102: ...Engine Maintenance 101 Figure 182 Fuel and Oil System Components ...
Страница 182: ...Index 181 Unit Options 23 W wiring 79 wiring diagrams index 182 ...
Страница 184: ...183 Schematic Diagram Page 1 of 2 RELEASED 06 Jul 2015 13 52 47 GMT 7 ...
Страница 185: ...184 Schematic Diagram Page 2 of 2 RELEASED 06 Jul 2015 13 52 47 GMT 7 ...
Страница 186: ...185 Wiring Diagram Page 1 of 5 ...
Страница 187: ...186 Wiring Diagram Page 2 of 5 RELEASED 06 Jul 2015 13 52 47 GMT ...
Страница 188: ...187 Wiring Diagram Page 3 of 5 ...
Страница 189: ...188 Wiring Diagram Page 4 of 5 RELEASED 06 Jul 2015 13 52 47 GMT ...
Страница 190: ...189 Wiring Diagram Page 5 of 5 ...