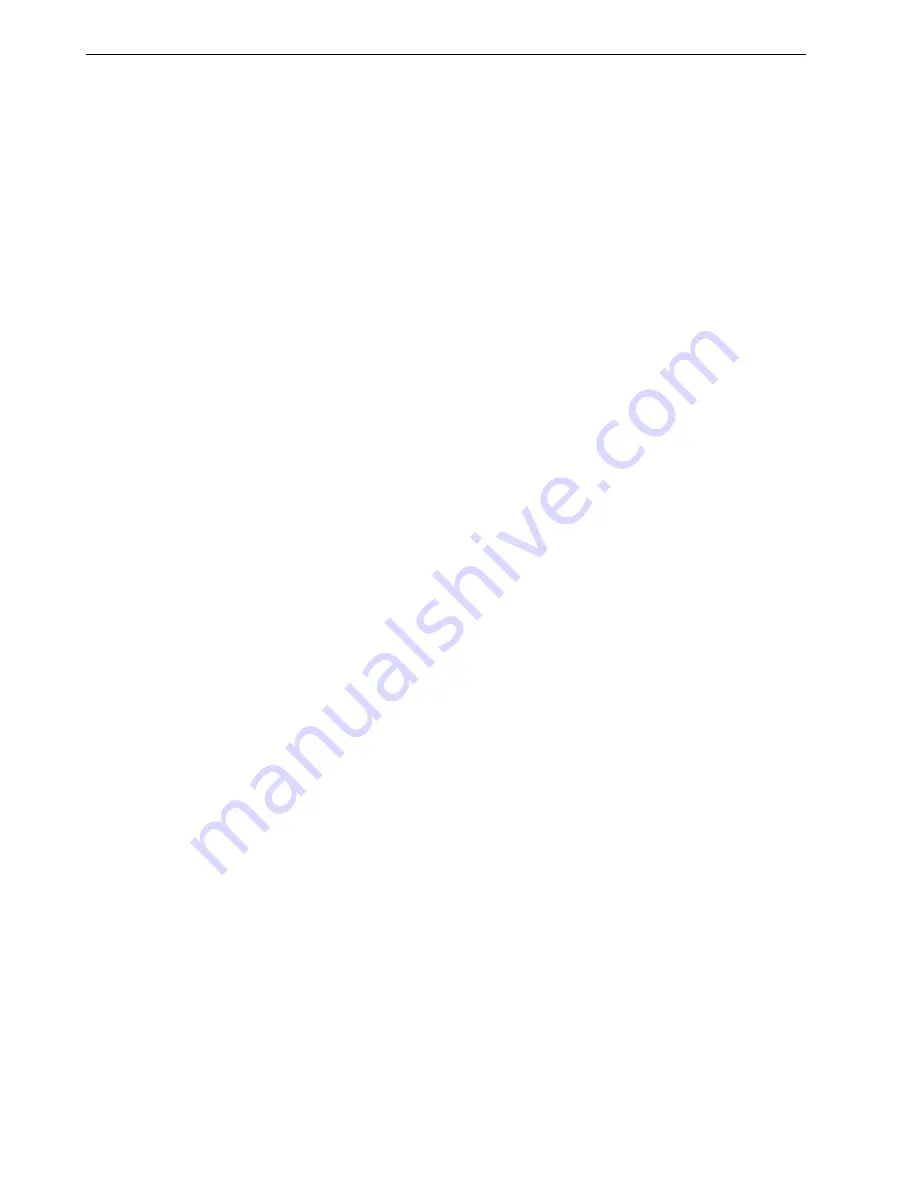
Refrigeration Service Procedures
126
valve. Control the liquid flow so the suction
pressure increases approximately 20 to 25 psig
(138 to 172 kPa).
9. Add refrigerant until the system has the
recommended refrigerant charge (see unit
serial number nameplate or the
“Specifications” chapter). Then close the
gauge manifold hand valve and the refrigerant
supply bottle hand valve.
Refrigerant Gauge Removal
NOTE: Low loss fittings must be used on hoses
when Schrader port fittings are encountered on
units.
1. With a low loss fitting on the discharge gauge
line, remove this line from the discharge
service port.
2. Backseat the suction service valve, and then
crack it open one turn.
3. Start the unit and use the Service Test mode to
run the unit in low speed cool. See the
appropriate Microprocessor Diagnostic
Manual for information about the Service Test
mode.
4. Open both service manifold hand valves.
5. Front seat the receiver tank outlet valve.
6. Run the unit until a 3 to 5 psig (21 to 35 kPa)
reading is obtained on the suction gauge, then
back seat the suction service valve.
7. Stop the unit.
8. Back seat the receiver tank outlet valve.
9. Remove all remaining hoses.
10. Install and tighten service port and valve stem
caps.
11. Unit is ready for a functional check out.
Refrigerant Leaks
Use a reliable leak detector (e.g., electronic
detector) to leak test the refrigeration system.
Inspect for signs of oil leakage which is the first
sign of a leak in the refrigeration system.
NOTE: It is normal for compressor shaft seals to
have a slightly oily film.
Refrigerant Charge
Testing the Refrigerant Charge with
an Empty Box (Controlled Check)
If the unit has an insufficient charge of refrigerant,
the evaporator will be “starved” and the box
temperature will rise even though the unit is
operating. The suction pressure will drop as the
refrigerant charge decreases. The charge may be
determined by inspection of the refrigerant
through the receiver tank sight glass with the
following conditions established:
1. Close the truck box doors.
2. Install a gauge manifold. On units equipped
with an ETV and a Premium HMI Control
Panel the pressures may be viewed on the
screen.
3. Run the unit on high speed cool until the air in
the box indicates 0 F (-18 C).
4. The discharge or head pressure gauge should
read 290 to 310 psig (1999 to 2137 kPa).
If the pressure is below this, it can be raised by
covering a portion of the condenser coil with a
piece of cardboard.
5. The suction pressure gauge should be
indicating 12 to 20 psig (83 to 138 kPa) gauge
pressure.
6. Under these conditions, the ball in the receiver
tank sight glass should be floating. If there is
no indication of refrigerant in the receiver tank
sight glass, the unit is low on refrigerant.
Testing the Refrigerant Charge with
a Loaded Box (Quick Check)
1. Install a gauge manifold (optional).
2. Run the unit on the Cool cycle.
3. Cover at least three quarters of the condenser
to drive any excess refrigerant from the
condenser into the receiver tank. Do not cover
the condenser for more than three minutes.
4. As the head pressure is rising, check the
receiver tank sight glass. The ball should be
floating. If there is no indication of refrigerant
Содержание T-1080S
Страница 102: ...Engine Maintenance 101 Figure 182 Fuel and Oil System Components ...
Страница 182: ...Index 181 Unit Options 23 W wiring 79 wiring diagrams index 182 ...
Страница 184: ...183 Schematic Diagram Page 1 of 2 RELEASED 06 Jul 2015 13 52 47 GMT 7 ...
Страница 185: ...184 Schematic Diagram Page 2 of 2 RELEASED 06 Jul 2015 13 52 47 GMT 7 ...
Страница 186: ...185 Wiring Diagram Page 1 of 5 ...
Страница 187: ...186 Wiring Diagram Page 2 of 5 RELEASED 06 Jul 2015 13 52 47 GMT ...
Страница 188: ...187 Wiring Diagram Page 3 of 5 ...
Страница 189: ...188 Wiring Diagram Page 4 of 5 RELEASED 06 Jul 2015 13 52 47 GMT ...
Страница 190: ...189 Wiring Diagram Page 5 of 5 ...