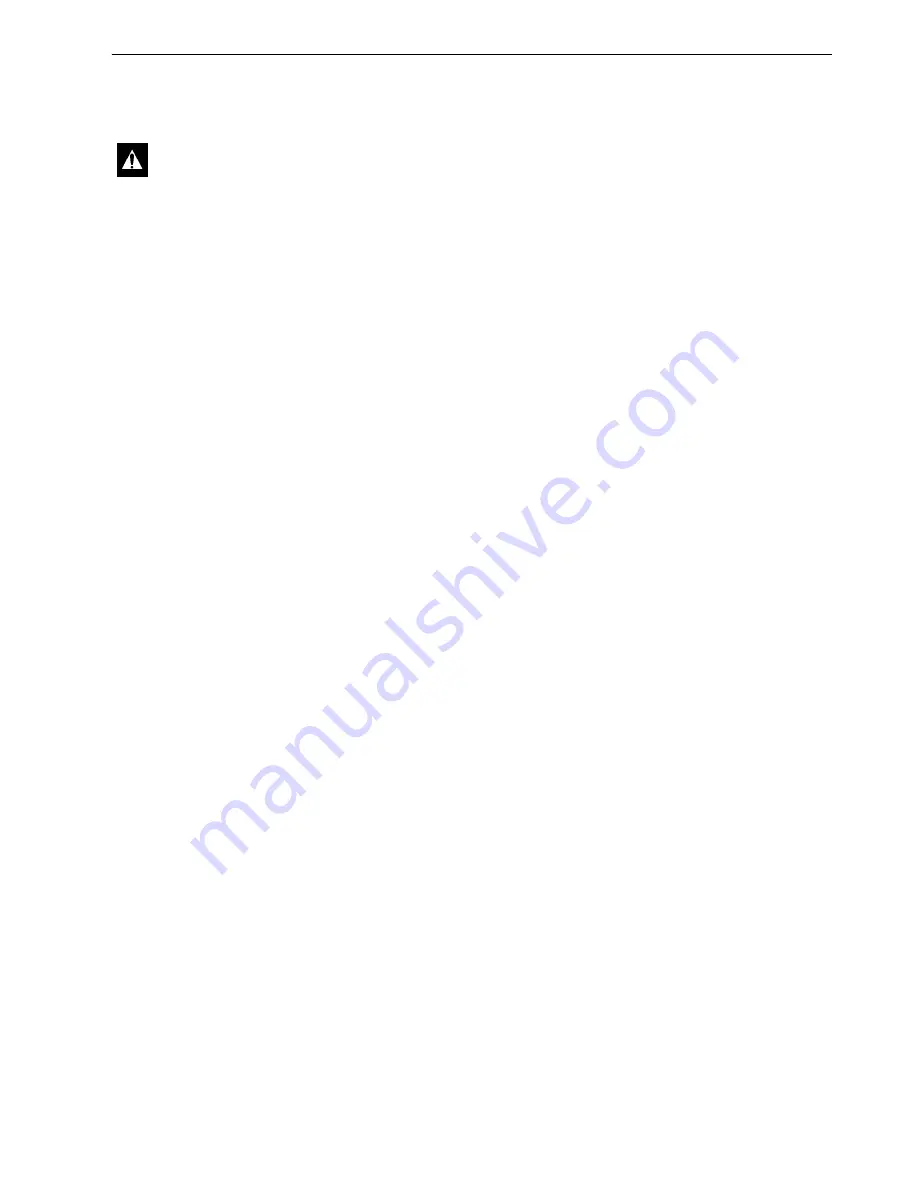
Refrigeration Maintenance
137
Recovering Refrigerant from
the System
When removing any refrigerant from a Thermo
King refrigeration system, use a recovery process
that prevents or absolutely minimizes the
refrigerant escaping to the atmosphere. Typical
service procedures that require removal of
refrigerant from the unit includes the following:
•
Reduce the refrigerant pressure to a safe
working level when maintenance must be
performed on high-pressure side components.
•
Empty the unit of refrigerant when an
unknown amount of charge is in the system
and a proper charge is required.
•
Empty the unit of contaminated refrigerant
when the system has become contaminated.
NOTE: Always refer to specific recovery
equipment Operator and Service Manuals.
Perform the following steps to recover vapor from
the system.
1. Turn unit off.
2. Install a gauge manifold set on the unit.
3. Attach the service line to the recovery
machine and properly purge the lines.
4. Set the recovery machine for vapor recovery.
5. Mid-seat the discharge service valve.
6. Turn on the recovery machine.
7. Open (back seat) both gauge manifold and
hand valves.
8. Continue to operate the recovery machine
until unit pressures drop to 0 kPa, 0 bar, 0 psig
pressure.
Evacuation and Cleanup of the
Refrigeration System
A thorough clean up is required whenever
contaminants have entered the system. This will
prevent damage to the compressor.
The purpose of evacuation is to remove moisture
and air from the refrigeration system after a
system has been opened to the atmosphere.
Evacuation must occur before recharging a system
with new refrigerant. The importance of thorough
evacuation and system preparation cannot be over
emphasized. Even infinitesimal quantities of air or
moisture in a system can cause severe problems.
The presence of moisture, oxygen, and heat can
create many forms of damage. They can create
corrosion, sludge, copper plating, oil breakdown,
carbon formation, and eventual compressor
failure.
Things that will contaminate a system are (in
order of importance):
Air:
With oxygen as a contaminant: Oxygen in the
air reacts with the oil. The oil begins to break
down and can eventually lead to carbonization in
the compressor and acid buildup. The longer this
breakdown process goes on, the darker the
compressor oil becomes until finally the color is
black indicating major system contamination.
Moisture:
Moisture in a system will cause metal
corrosion and metal plating. It can freeze in the
expansion valve and cause intermittent
operational problems. It reacts in the oil to begin
acid buildup.
Dirt, Dust, Metal Particles, other Foreign
Materials:
Particles of any kind left to float
through the system will cause severe damage to
all close tolerance items. Do not leave a system
open to the infiltration of dirt. If you must open a
system for any reason, seal off the open areas as
soon as possible and do not work in a dirty
environment.
Acid:
Air and moisture cause a chemical
breakdown of the oil and/or the refrigerant itself.
The acid will accelerate the deterioration of the
softer metals (i.e., copper) and cause metal plating
as the softer material begins to cover the inside of
the system. If this condition is not stopped, it can
result in the total destruction of your equipment.
CAUTION: Use only refrigerant recovery
equipment approved for and dedicated to
R-404A recovery.
Содержание 098916
Страница 2: ...MAGNUM TK 51122 4 MM Rev 6 02 06 Copyright 2004 Thermo King Corp Minneapolis MN USA Printed in USA...
Страница 5: ......
Страница 11: ...Table of Contents 10...
Страница 19: ...Service Guide 18...
Страница 28: ...Specifications 27 Figure 2 Physical Specifications AMA313...
Страница 41: ...Unit Description Features Options 40...
Страница 105: ...Operating Instructions 104...
Страница 155: ...Servicing The Unit 154...
Страница 187: ...Index 186...
Страница 189: ...Wiring and Schematic Diagrams Index 188...
Страница 190: ...189 Wiring Schematic...
Страница 191: ...190 Wiring Diagram Page 1 of 2...
Страница 192: ...191 Wiring Diagram Page 2 of 2...