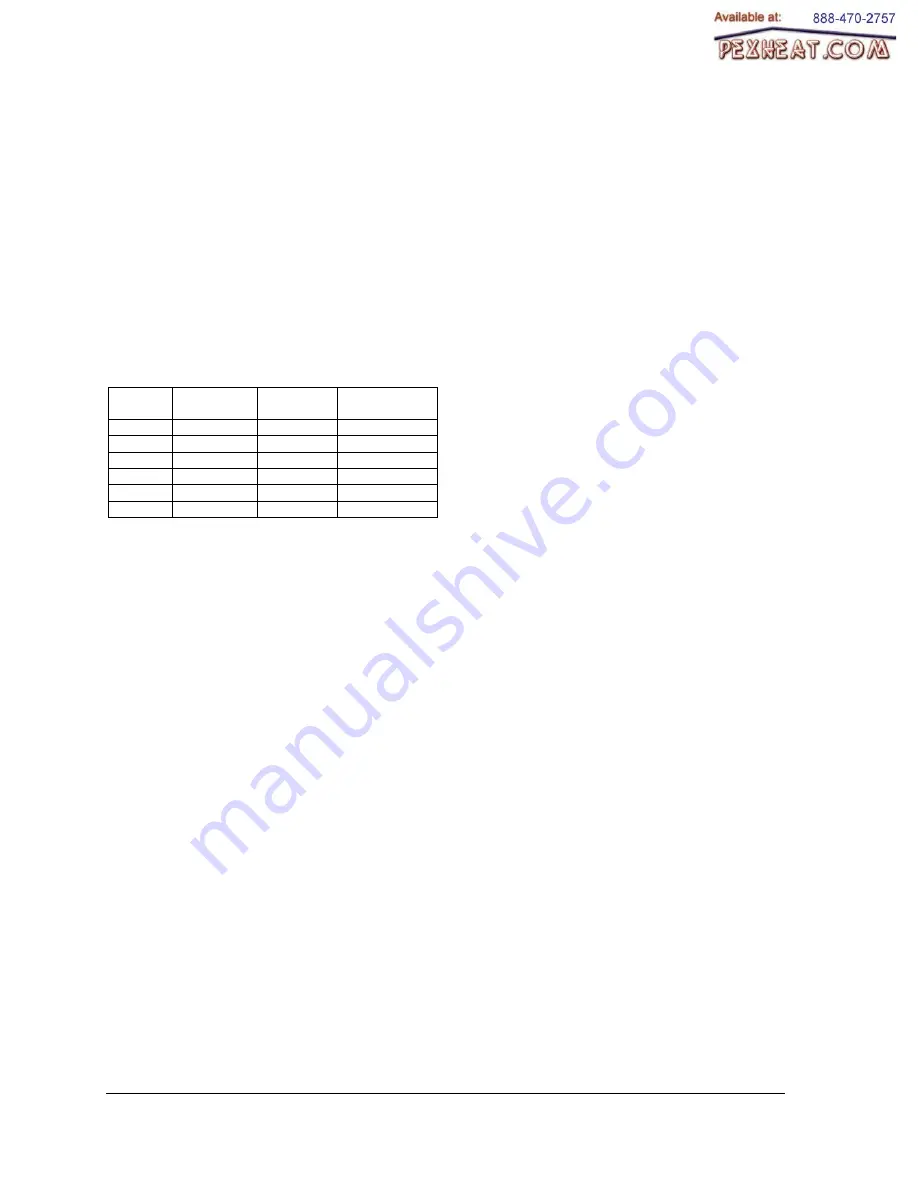
Electric boilers MINI BTH
Installation & Operating Manual (Revision: May 2015),
8
The main air eliminator must be installed near
the outlet of the boiler on the highest point of the
main supply piping. It is imperativel to insure that
all air possibly located in the boiler be eliminated
at all time.
3.4.6 Circulating pump
The pump shall be selected such as to be able
to supply adequate flow in relation to the heating
distribution system on which it will be connected
and the heating capacity of the boiler installed.
Table below will give you details on required
water flow for distribution systems having to
operate with a temperature differential of 10F
and 20F between their inlet and outlet
.
Model
Diff. 10°F
usgpm
Diff. 20°F
usgpm
Boiler press.
loss
3 kW
2.0
1.0
insignificant
4.5 kW
3.0
1.5
insignificant
6 kW
4.1
2.0
insignificant
7.5 kW
5.1
2.5
insignificant
9 kW
6.1
3.0
insignificant
12 kW
8.2
4.1
insignificant
Your heating wholesaler shall be able to
recommend the appropriate model for your
application.
The amperage drawn by the pump and other
120volts components must not exceed 15 amps.
3.4.7 Drain valve
Installed at the lowest point of the unit, it allows
the unit to be drained for the eventual
replacement of a defective component.
3.4.8 Strainer
This component could be required on old
heating distribution systems made of steel or
cast iron that could carry sediments and sludge.
If such sediments accumulate at the bottom of
the boiler it could be harmful to the heat transfer
of the elements and generate premature
failures.
3.5 ELECTRICAL CONNECTIONS
3.5.1 Main boiler supply
Boiler wiring and grounding must conform to the
National Electrical Code and to state or local
code
requirements.
The
latter
having
precedence.
The electrical supply can be done in two
different ways depending on the necessity of
supplying or not external accessories (such as a
pump) at 120Vac.
If the boiler electrical supply is on 208V, the
position of wire terminal on the transformer
connected to 240V will have to be changed to
208V.
Alternative #1: A 120VAC electrical supply is
required to serve external accessories
.
Electrical wiring must come from a 120/240
Vac/or 120/208Vac -
1ph “L1-N-L2-” circuit
protected by a properly sized breaker.
Alternative #2: No 120Vac electrical supply is
required to serve external accessories (pump
is supplied by a separate circuit)
Electrical wiring must come from a 240Vac or
208Vac- 1ph/
60hz “L1-L2” circuit protected by a
properly sized breaker.
Wire gage must be properly sized by a qualified
electrician in such a way as to meet the national
electrical code.
To do so, consult the boiler rating plate which
will indicate the amperage drawn by the boiler at
full capacity. Extra amperage will have to be
added if external electrical equipments are
connected to the boiler.
This value and the electrical code will be used to
determine the electric cable required together
with the appropriate breaker.
Many other factors must be taken into
consideration in the selection of the appropriate
electrical material such as the length and the
type of cable used, the environment where the
cable will be installed and the type of the over-
current protection used.
The main terminal block of the boiler is suitable
for #14 to #2 wires.
Supply cables can be made of Aluminum or
Copper and be rated for a minimum of 75
o
C
(165
o
F).
If aluminum cables are used, it shall be of an
adequate size (generally bigger) and particular
consideration will have to be respected such as
the use of DE-OX inhibitors in order to meet the
National electrical code.