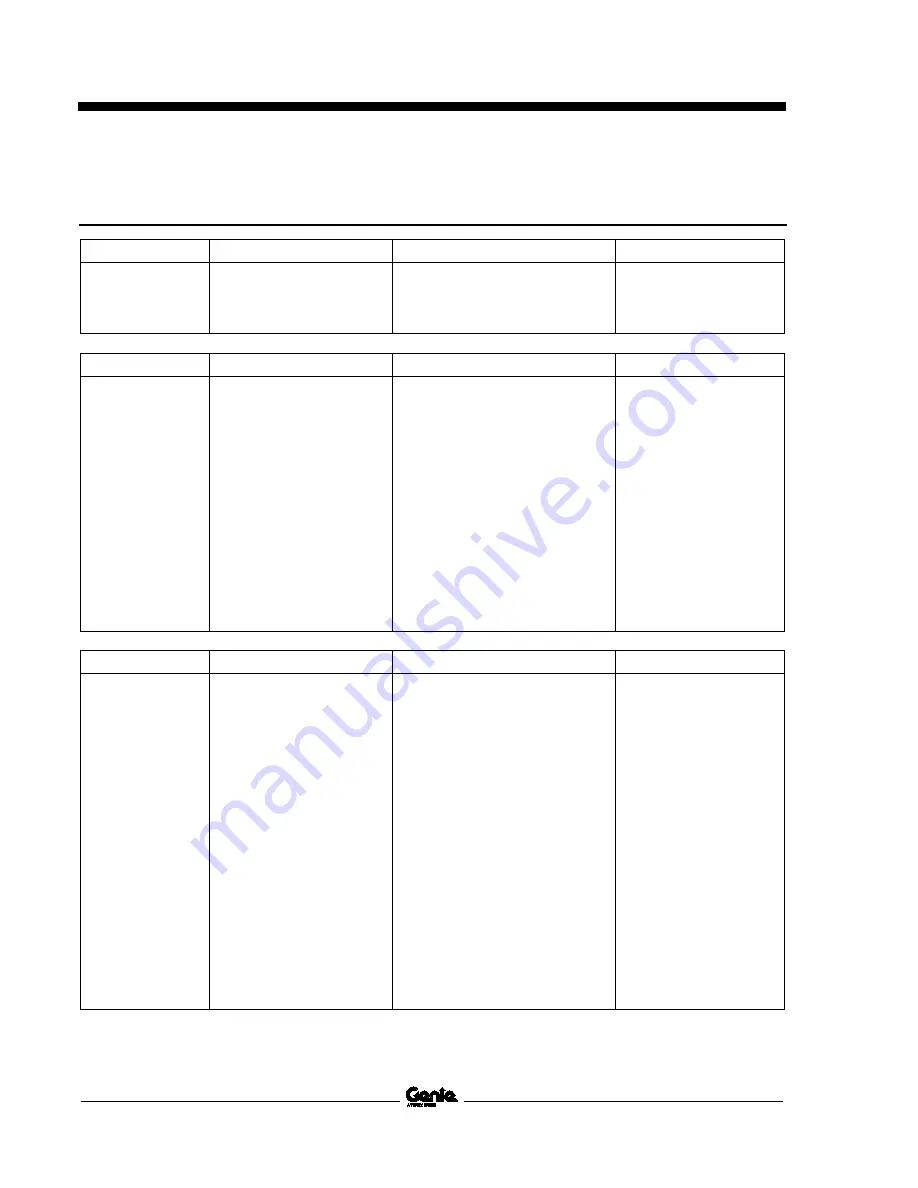
Service and Repair Manual
December 2019
Control System
20
S
®
-60 J
Part No. 1285305GT
1-6
Display Module Menus
Screen or Menu
Item
Selection
Default
Display Settings
Backlight
0 - 100%
Contrast
0 - 100%
Display Inversion
On / Off
Off
Screen or Menu
Item
Selection
Default
Model
Configuration
Model
S-40 / S-45 / S-60 / S-65 / S-60J /
S-80 / S-85
Select Model
Tires
Rough Terrain / High Float / Trax
Select Tires
(These are locked
unless factory
defaults are
restored)
Engine
Deutz 2.9L / Deutz Turbo 2.9L /
Deutz D2011 L03i / Deutz TD2011
L04i / Ford MSG425 EFI / GM 3.0L /
Kubota D1105 / Kubota D1803 /
Perkins 404D-22 / Perkins
404D-22T / Perkins 404F E22T /
Perkins 404F E22TA
Select Engine
(Platform
configuration is not
locked)
Platform
Standard Platform
4m / 13 ft. Platform
Select Platform
Region
ANSI/CSA / AUS / CE
Select Region
Screen or Menu
Item
Selection
Default
Options
Footswitch Timeout
10 sec / 2 min / 30 min
2 min
Note: Some options
may not be visible
with earlier software
revisions.
Drive Priority
On / Off
Off
Drive Cutout
On / Off
Off
Platform Level
On / Priority / Cutout
On
Generator
No Generator / Generator Installed No Generator
Contact Alarm
On / Off
On
Platform Recirculation
On / Off
Off
Units
US Customary / Metric
US Customary
Aircraft Proximity
On / Off
Off
Fuel Level Sensor
Not Installed / Installed
Not Installed
Glowplug Preglow Time
1 sec - 100 sec
12 sec
Lift Connect
Not Installed / Installed
Installed
Alarm Setting
Off / Travel / Motion
Off
Содержание S-60 J
Страница 65: ...December 2019 Service and Repair Manual Part No 1285305GT S 60 J 53 This page intentionally left blank ...
Страница 67: ...December 2019 Service and Repair Manual Manifolds Part No 1285305GT S 60 J 55 ...
Страница 69: ...December 2019 Service and Repair Manual Manifolds Part No 1285305GT S 60 J 57 ...
Страница 75: ...December 2019 Service and Repair Manual Part No 1285305GT S 60 J 63 This page intentionally left blank ...
Страница 77: ...December 2019 Service and Repair Manual Manifolds Part No 1285305GT S 60 J 65 ...
Страница 114: ...Service and Repair Manual December 2019 102 S 60 J Part No 1285305GT This page intentionally left blank ...
Страница 115: ...December 2019 Service and Repair Manual 103 Electrical Schematic Generator Options ...
Страница 116: ...Service and Repair Manual December 2019 104 S 60 J Part No 1285305GT Electrical Schematic Generator Options ...
Страница 117: ...December 2019 Service and Repair Manual Part No 1285305GT S 60 J 105 Electrical Schematic Positive Air Shutdown ...
Страница 118: ...Service and Repair Manual December 2019 106 Electrical Schematic Positive Air Shutdown ...
Страница 119: ...December 2019 Service and Repair Manual 107 Electrical Schematic Turntable Controller ...
Страница 120: ...Service and Repair Manual December 2019 108 S 60 J Part No 1285305GT Electrical Schematic Turntable Controller ...
Страница 121: ...December 2019 Service and Repair Manual Part No 1285305GT S 60 J 109 Electrical Schematic Platform Controller ...
Страница 122: ...Service and Repair Manual December 2019 110 Electrical Schematic Platform Controller ...
Страница 123: ...December 2019 Service and Repair Manual 111 Electrical Schematic Kubota D1803 ...
Страница 124: ...Service and Repair Manual December 2019 112 S 60 J Part No 1285305GT Electrical Schematic Kubota D1803 ...
Страница 125: ...December 2019 Service and Repair Manual Part No 1285305GT S 60 J 113 Electrical Schematic Kubota D1105 ...
Страница 126: ...Service and Repair Manual December 2019 114 Electrical Schematic Kubota D1105 ...
Страница 127: ...December 2019 Service and Repair Manual 115 Electrical Schematic Deutz D2011 ...
Страница 128: ...Service and Repair Manual December 2019 116 S 60 J Part No 1285305GT Electrical Schematic Deutz D2011 ...
Страница 129: ...December 2019 Service and Repair Manual Part No 1285305GT S 60 J 117 Hydraulic Schematic ...
Страница 131: ......