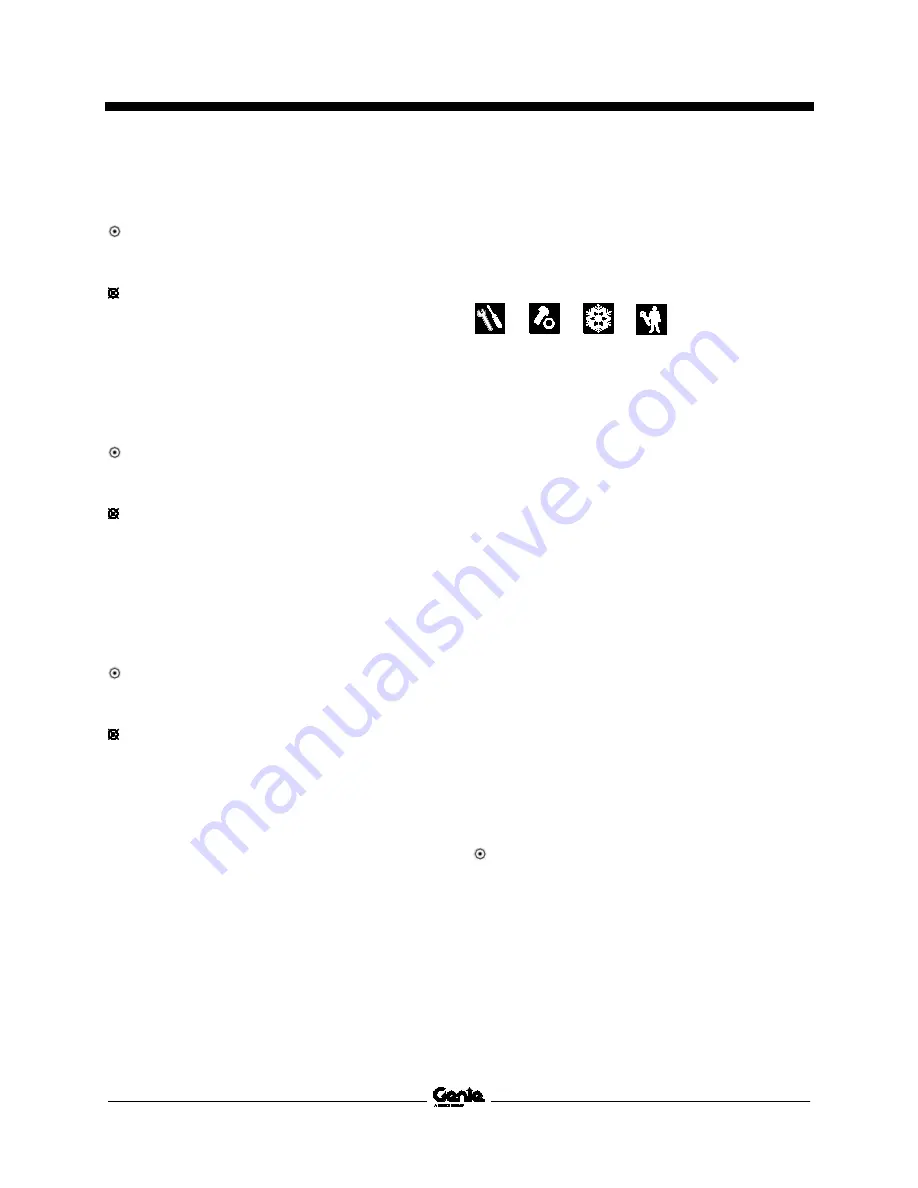
Maintenance Manual
March 2022
Programmed Maintenance Procedures
172
S
®
Booms • Z
®
Booms
Part No. 1268489GT
S-100, S-100HD, S-105, S-120, S-120HD and S-
125
Result: The gap is between 0.010 inch /
0,254 mm and 0.022 inch / 0,559 mm. The
backlash is within tolerance.
Result: The gap is less than 0.010 inch /
0,254 mm or more than 0.022 inch /
0,559 mm. The backlash needs to be
adjusted. Refer to Repair Procedure in the
appropriate Service and Repair Manual for
your machine,
How to Adjust the Turntable
Rotation Gear Backlash
.
SX-150 and SX-180
Result: The gap is between 0.016 inch /
0,406 mm and 0.024 inch / 0,62 mm. The
backlash is within tolerance.
Result: The gap is less than 0.016 inch /
0,406 mm or more than 0.024 inch / ,.62 mm.
The backlash needs to be adjusted. Refer to
Repair Procedure in the appropriate Service
and Repair Manual for your machine,
How to
Adjust the Turntable Rotation Gear Backlash
.
SX-105 XC, SX-125 XC, SX-135XC, Z-135/70 and
ZX-135/70
Result: The gap is between 0.013 inch /
0,33 mm and 0.023 inch / 0,58 mm. The
backlash is within tolerance.
Result: The gap is less than 0.013 inch /
0,33 mm or more than 0.023 inch / 0,58 mm.
The backlash needs to be adjusted. Refer to
Repair Procedure in the appropriate Service
and Repair Manual for your machine,
How to
Adjust the Turntable Rotation Gear Backlash
.
4 Repeat the procedure for the other turntable
rotation hub.
P2-8
Grease the Steer Axle Wheel
Bearings, All 2WD Models
(except S-60, S-65, Z-60 DC/FE
and Z-62)
Genie requires that this procedure be performed
every 2000 hours.
Perform this procedure more often if dusty
conditions exist.
Maintaining the steer axle wheel bearings is
essential for safe machine operation and service
life. Operating the machine with loose or worn
wheel bearings may cause an unsafe operating
condition and continued use may result in
component damage. Extremely wet or dirty
conditions or regular steam cleaning and pressure
washing of the machine may require that this
procedure be performed more often.
1 Loosen the wheel lug nuts. Do not remove
them.
2 Block the non-steer wheels, then center a
lifting jack under the steer axle.
3 Raise the machine 6 inches / 15 cm and place
blocks under the drive chassis for support.
4 Remove the lug nuts. Remove the tire and
wheel assembly.
5 Check for wheel bearing wear by attempting
to move the wheel hub side to side, then up
and down.
Result: There should be no side to side or up
and down movement.
Skip to step 10 if there is no movement.