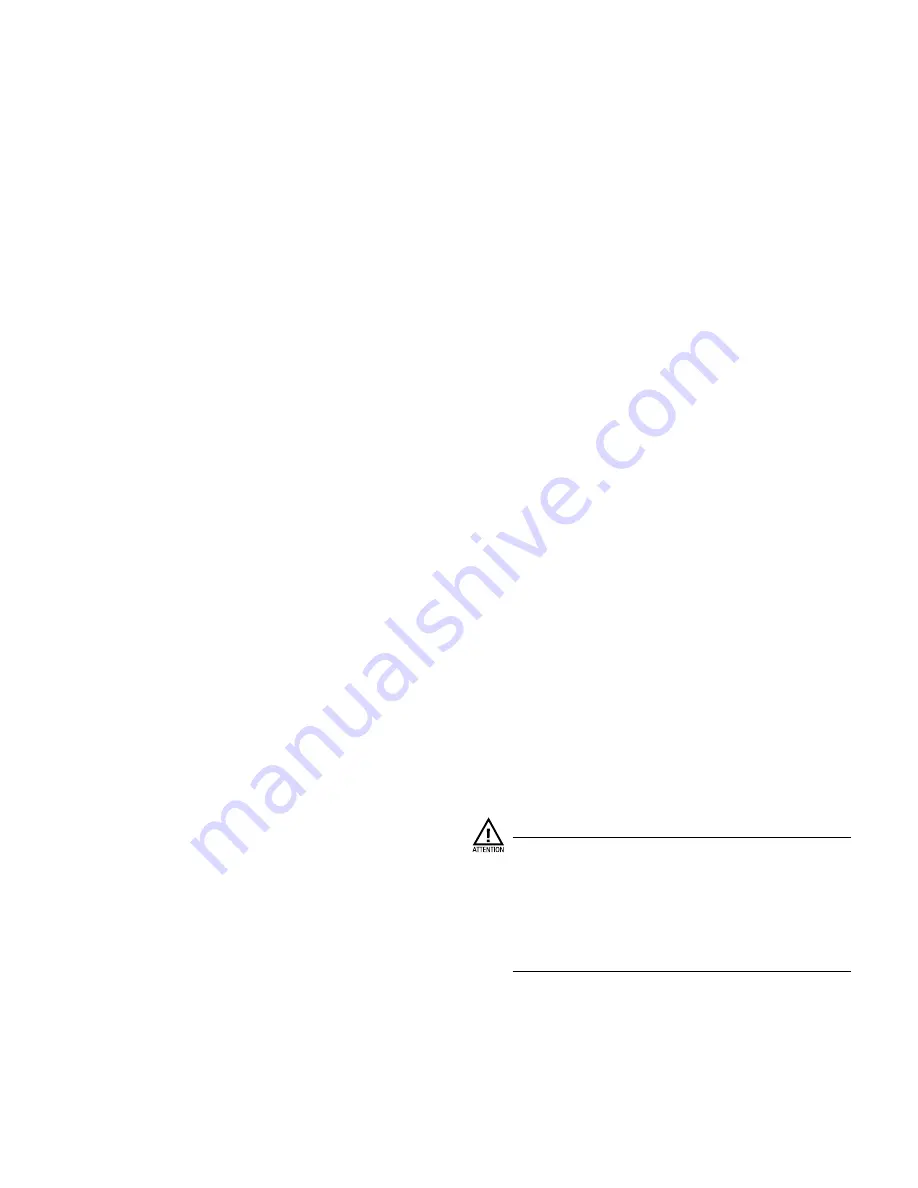
Teikoku USA | Chempump
Instruction Manual NC-Series 0220
7
2. Installation
2.1 Receipt Inspection
1. Avoid rough handling during loading, transportation and un-
loading.
2. Visually inspect the shipping container for evidence of dam-
age during shipment.
3. Check unit to see that suction, discharge, and any other con-
nections are covered.
4. Inspect the suction, discharge and any other connections gas-
ket seating surface to be certain that they are clean of foreign
matter and free from nicks, gouges, and scratches.
5. Check phase resistance and megger resistance to ground of
.
6. Check all nameplate data against shipping papers.
7. Caution should be observed during handling, so as not to
bend the circulation line.
2.1.1 Storage Note
In situations where a pump is to be stored for a period of time
prior to installation, and where the climate experiences wide
temperature changes and high humidity, the terminal box must
be sealed to prevent moisture from entering the motor winding
area.
2.2 Structural
The pump design and construction eliminates the need to align
the pump and motor. The pump should be supported using the
mountings provided and mounted so that its weight is properly
supported. Suction and discharge piping must be properly
supported and aligned so that no strain is placed on the pump
casing.
1. Remove burrs and sharp edges from flanges when making
up joints.
2. When connecting flanged joints, be sure inside diameters
match within 1/16" so as not to impose a strain on the pump
casing.
3. Use pipe hangers or supports at intervals as necessary.
2.2.1 Pump Location
Locate the pump as close as possible to the fluid supply with a
positive suction head. Installations with suction lift are possible
but not recommended.
Since standard pumps are not self-priming, provide for initial
priming and for maintaining a primed condition. Location of the
pump and arrangement of the system should be such that suf-
ficient NPSH (Net Positive Suction Head) is provided over vapor
pressure of the fluid at the pump inlet. NPSH requirements at the
design point are stated on the pump order copy. For additional
design points, refer to the corresponding performance curves
placed in the Appendix of this manual.
Note:
Experience has proven that most pump troubles result from
poor suction conditions including insufficient NPSH. The suction
line must have as few pressure drops as possible and available
NPSH MUST be greater than required NPSH.
Depending on job conditions, available NPSH can sometimes be
increased to meet the NPSH required by the pump for satisfac-
tory operation. NPSH can be tailored by changes in the piping,
in liquid supply level, and by several other methods. Refer to
2.2.2 Mounting and Alignment
Chempump combines a pump and motor in a single hermetically
sealed unit. No tedious coupling alignment is required because
the pump has no external coupling between pump and motor. All
models can be mounted in any position.
For mounting with suction and discharge on the side or in any
other position, modifications must be made to the standard
internal venting arrangement.
High temperature systems normally require expansion joints in the
piping to relieve the stresses in the pipe and the pump due to
expansion and contraction. The NC-Series, when mounted so that
the base can float with the pipe expansion (as opposed to rigidly
bolting the pump to a foundation) or using a spring mounted
foundation, eliminates the need for the expansion joints, which
can save considerable expense in the installation.
Bases are offered on all models. You merely have to set the pumps
on a foundation strong enough to support their weight. There is
no need to bolt down or grout in a Chempump
TM
. All NC-Series
models are provided with a specially made base designed to
mount on a standard ANSI baseplate to facilitate inspection and
repair.
Be sure that suction and discharge piping is properly aligned so
that no strain is placed on the pump casing by out-of-line piping.
2.2.3 Piping Data
Attention!
It is recommended to install a temporary cone-style strain-
er near the suction port to trap scale and other foreign
particles. Suction strainer to be sized and designed per
Teikoku recommendations. The screen can be installed for
24 hours of operation, but must be monitored closely so
the pump does not become starved for liquid because of a
clogged screen. Remove screen after 24 hours of running.
Observe the standards of the Hydraulic Institute when sizing and
making up suction and discharge piping. Follow these procedures:
1. Remove burrs and sharp edges when making up joints.
2. When using flanged joints, be sure inside diameters match
properly. When gasketing flanged joints, do not cut flow hole
smaller than flange opening.
3. Use pipe hangers or supports at necessary intervals.