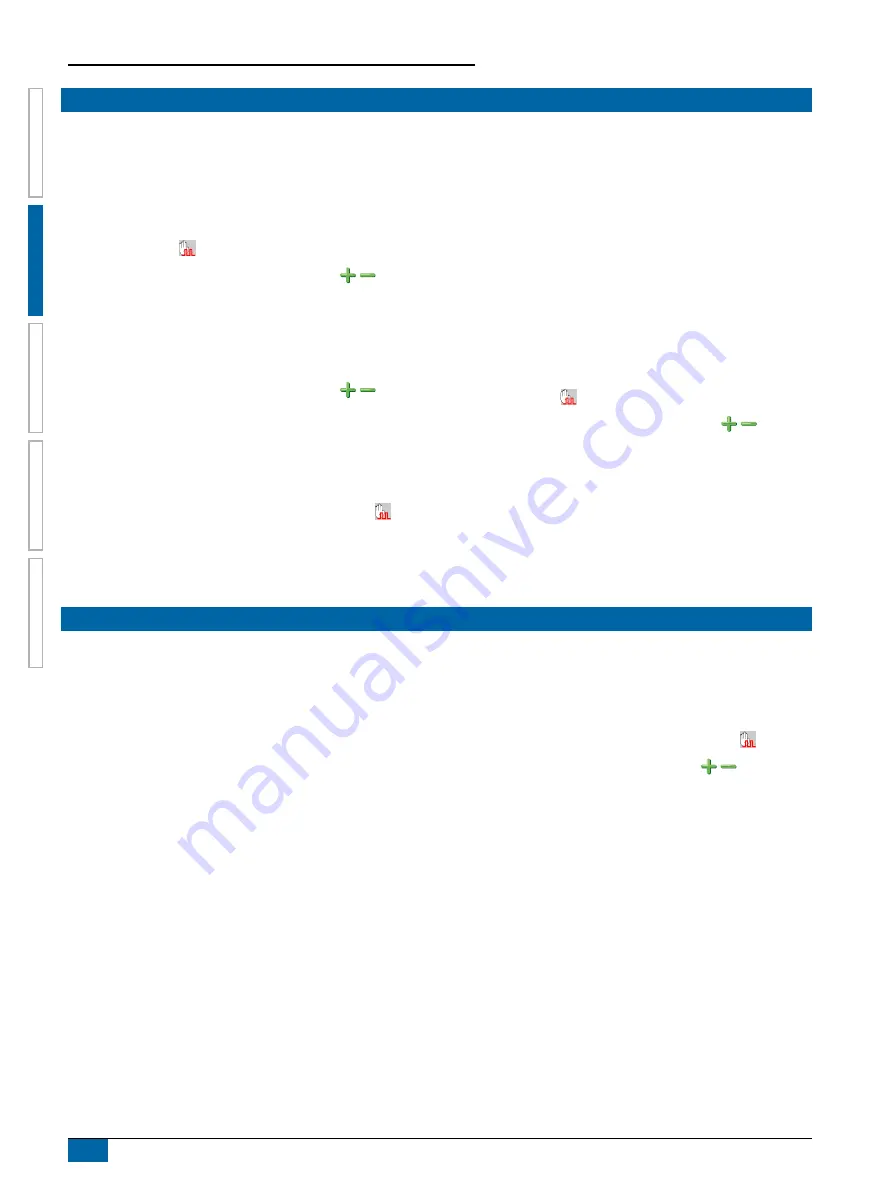
DynaJet
®
Flex 7140
OPER
ATION
MENU OPTIONS
INTR
ODUC
TION
APPENDIX
8
www.teejet.com
INITIAL ST
AR
TUP
NO. 5 PREFORM SYSTEM FUNCTIONAL TEST
The following is instructions for performing a functional test of the
system.
•
Ensure that current rate control system is operating normally
prior to attempting to use the DynaJet Flex.
1. On the Work screen, set DynaJet Flex operating mode to
Manual Mode .
2. Using the MANUAL ADJUSTMENT buttons , set
PWM duty cycle at 100%. This will make the system
operates as if DynaJet Flex was not present.
3.
Use this configuration to verify the rate control system is
operating normally.
4. Using the MANUAL ADJUSTMENT buttons , set
PWM duty cycle to 50%.
5.
Use this configuration to verify the rate control system is
operating normally.
•
Confirm boom section functionality.
1. Continue operating DynaJet Flex in Manual Mode with
PWM duty cycle set to 50%.
2. Switch the master switch ON (on rate controller or other
boom section control switches)
3. Using the switch box, turn ON each section verifying the
proper section turns blue on the DynaJet Flex Work screen.
4. Turn the master switch OFF. On the DynaJet Flex Work
screen, verify all sections are now grey.
•
Start pump and ensure no leaks.
•
Verify pressure on mechanical gauge matches the digital
pressure display within reason. If not, adjust maximum pressure
sensor value as previously described.
•
Confirm e-ChemSaver Solenoids is impulsing
•
Configure in PWM mode DynaJet Flex at duty cycle of 50%.
1. On the Work screen, set DynaJet Flex operating mode to
Manual Mode .
2. Using the MANUAL ADJUSTMENT buttons , set
PWM duty cycle to 50%.
3.
Use this configuration to verify each of the corresponding
e-ChemSaver Solenoids is impulsing.
This confirms the basic functionality of the DynaJet Flex system.
Further details for fine-calibrating the system are in “Calibrate the
DynaJet Flex System” section of this guide.
NO. 6 CALIBRATE THE RATE CONTROLLER REGULATION
The following procedure determines the most aggressive rate
controller regulation valve gain that will work over all pressure
ranges.
Before you begin:
•
Ensure product pump is providing flow greater than
the maximum demand of the system. Consult sprayer
manufacturer specifications.
• Understand that the most aggressive value will be found
by increasing valve gain until system oscillates and then
decreasing the setting until the system is stable at that value.
NOTE: Other rate controller specific settings may apply
based on your specific rate controller system
• The rate controller must be operating in automatic mode
during these tests.
• To attain the minimum and maximum operating pressures for
the specific nozzle in use under each test condition the user
must be able to either: adjust the target application rate, or
adjust the machine speed
Flow Impulses Tests
The following tests will confirm that impulse of flow through the
solenoids will not affect rate controller stability even when duty
cycle is below 50%.
1. Set DynaJet Flex operating mode to Manual Mode .
2. Using the MANUAL ADJUSTMENT buttons , set PWM
duty cycle as noted in each test.
3.
Preform tests as specified in the following sections, taking note
of the pressure levels during each test.
4. Set rate controller valve gain to the highest value that will work
with all three of the following tests. This will be the lowest gain
value found in the 3 tests. Once established, this value should
not need to be changed again.
If the system does not control acceptably with this gain value
at all manual duty cycle settings, then something is wrong
with the system that needs to be resolved before trying to
calibrate the DynaJet Flex System. For assistance, contact
TeeJet Technologies Customer Support or an authorised TeeJet
Technologies dealer if additional support is required.