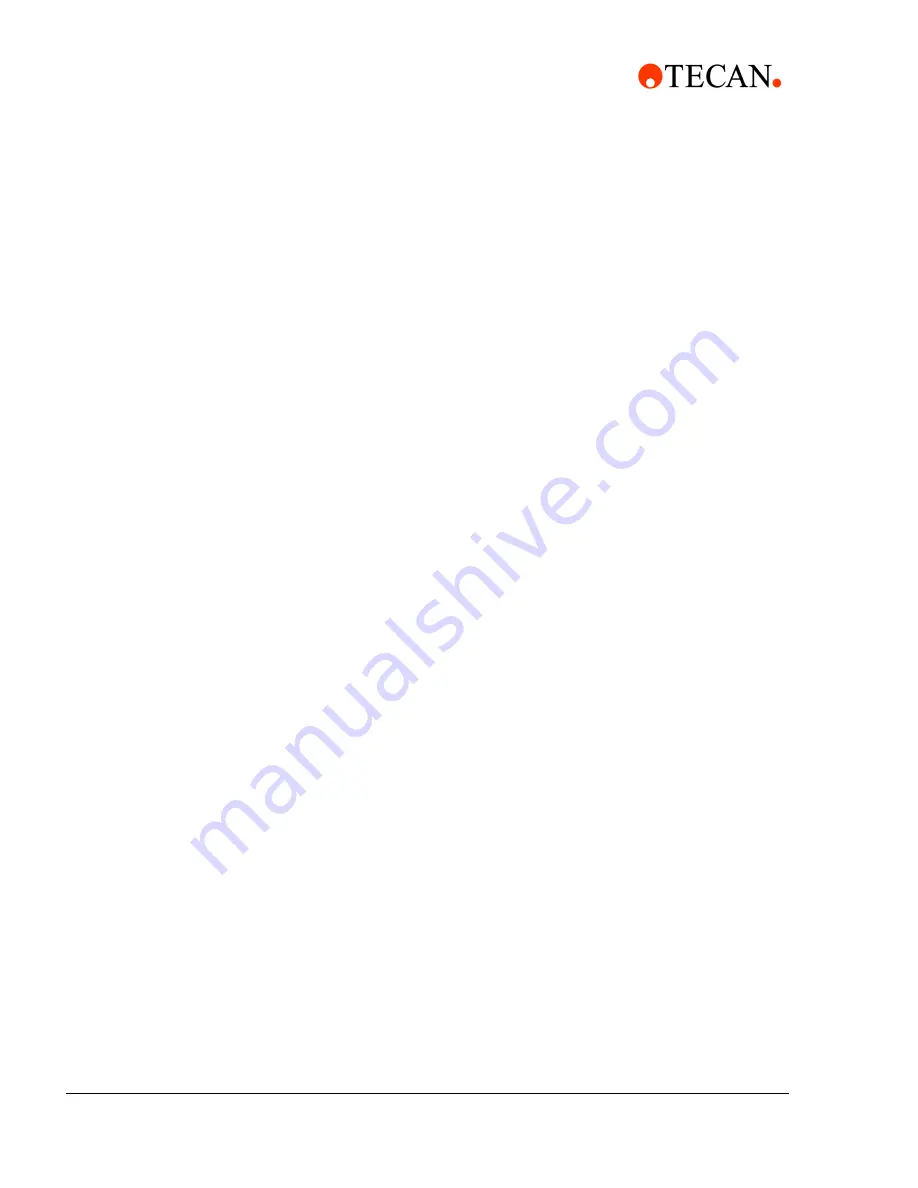
3 - 10
Cavro® XLP 6000 Modular Syringe Pump Operating Manual, 734237-C, en
3 - Software Communication
Communication Protocols
6
Click
OK
.
7
Select the
File
menu, and choose
Properties
. The Properties dialog box
appears.
8
Select the
Settings
tab, and enter or select these options:
–
Function, arrow, and Control keys act as:
•
Select “Terminal keys”
–
Emulation:
•
Select “Autodetect”
•
Enter “500” in Backscroll buffer lines
–
Click the
ASCII Setup
button. The ASCII Setup dialog box appears.
9
Enter or select these options:
–
Select “Send line ends with line feed”
–
Select “Echo typed characters locally”
–
Enter a Line delay of “0”
–
Enter a Character delay of “0”
–
Select “Wrap lines that exceed terminal width”
10
Click
OK
to close the ASCII Setup dialog box, then click
OK
to close the
Properties dialog box.
11
Set the pump address to 0 or the appropriate address.
12
The communication protocol is detected automatically.
13
Power on the pump and initialize it by typing /1ZR and pressing
Enter
.
To run the pump, see the commands listed in “Using the XLP 6000 Command
Set” in this chapter.
3.2.4
CAN Interface Communications
CAN (Controller Area Network) is a two-wire, serial communication bus. It
eliminates polling sequences that verify task completion. Using CAN, the pumps
asynchronously report to the master or host when they have finished the current
task.
Note: All Tecan XLP 6000 systems use CAN controller chips compatible with
Phillips Semiconductor CAN bus specification, version 2.0.
When using the CAN interface, termination resistors (120 ohm) are necessary at
both ends of the bus. The pump does not provide CAN termination resistors.
CAN Messages
CAN messages consist of
frames
. Each frame has an 11-bit Message Identifier
(MID) and a 4-bit length identifier. The bits:
Indicate to which device on the bus the message is directed
Identify the message type
Show the direction of the message (to or from the master device)