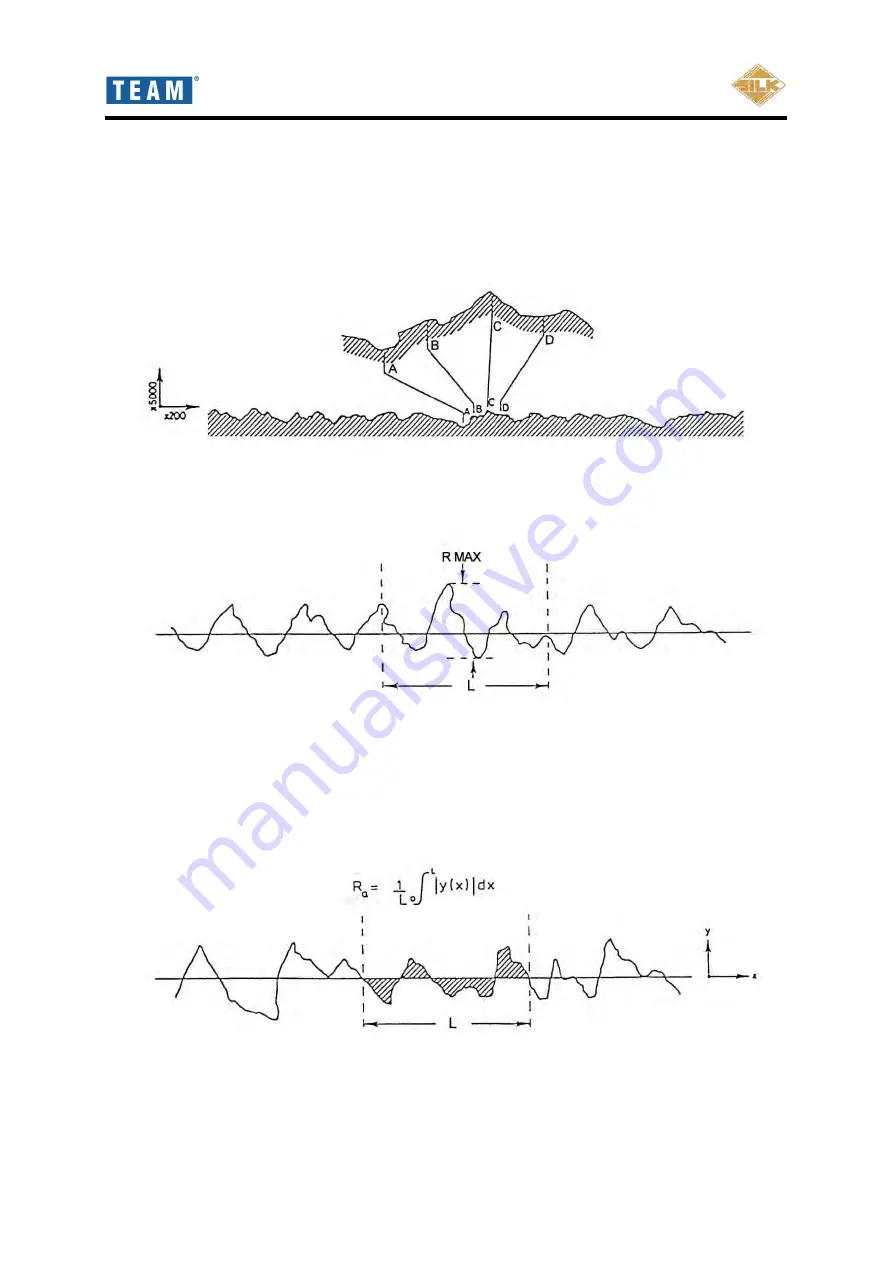
AX08 Flange Facing and Grooving Machine
59
APPENDIX B
SURFACE METROLOGY
First profile graphs of roughness texture were produced over fifty years ago by a German Engineer,
Gustav Schmalz. His graphs allowed differential magnification of vertical and horizontal axes so that a
visual assessment of surface could be made.
These profile graphs did not provide the direct indications of magnitude required by workshops. Of the
usual ways of measuring a wave from the deepest individual roughness depth of surface (R Max) was
too dependent on extremes e.g. dirt or scratches.
Conventional statistical terms like RMS present instrumental difficulties: The compromise is to use Ra
previously known as C.L.A. (Centre Line Average) which can be determined on a purely geometrical
basis and easily measured on an electrical instrument.
Ra
This is the arithmetic mean of the departure of the profile of the surface from the mean line.
Содержание SILK AX08
Страница 43: ...AX08 Flange Facing and Grooving Machine 42 Figure 21 AX08 Machine Main Assembly ...
Страница 45: ...AX08 Flange Facing and Grooving Machine 44 Figure 22 AX08 Machine Main Assembly ...
Страница 46: ...AX08 Flange Facing and Grooving Machine 45 8 2 SADDLE ASSEMBLY Figure 23 AX08 Saddle Assembly ...
Страница 49: ...AX08 Flange Facing and Grooving Machine 48 Figure 24 AX08 Saddle Assembly Exploded View ...
Страница 50: ...AX08 Flange Facing and Grooving Machine 49 8 3 BASE CLAMPING ASSEMBLY Figure 25 Base clamping assembly ...
Страница 56: ...AX08 Flange Facing and Grooving Machine 55 Figure 30 Toolpost Assembly ...
Страница 58: ...AX08 Flange Facing and Grooving Machine 57 TYPES OF TOOL BIT FOR GENERAL PURPOSE AND FINE FINISH ...
Страница 59: ...AX08 Flange Facing and Grooving Machine 58 TOOLS FOR V GROOVE PLUNGE MACHINING ...
Страница 63: ...AX08 Flange Facing and Grooving Machine 62 APPENDIX C V GROOVE MEASUREMENT ...
Страница 64: ...AX08 Flange Facing and Grooving Machine 63 ...
Страница 65: ...AX08 Flange Facing and Grooving Machine 64 APPENDIX D AIR MOTOR MANUFACTURERS INFORMATION ...
Страница 66: ...AX08 Flange Facing and Grooving Machine 65 APPENDIX E DECLARATION OF CONFORMITY ...