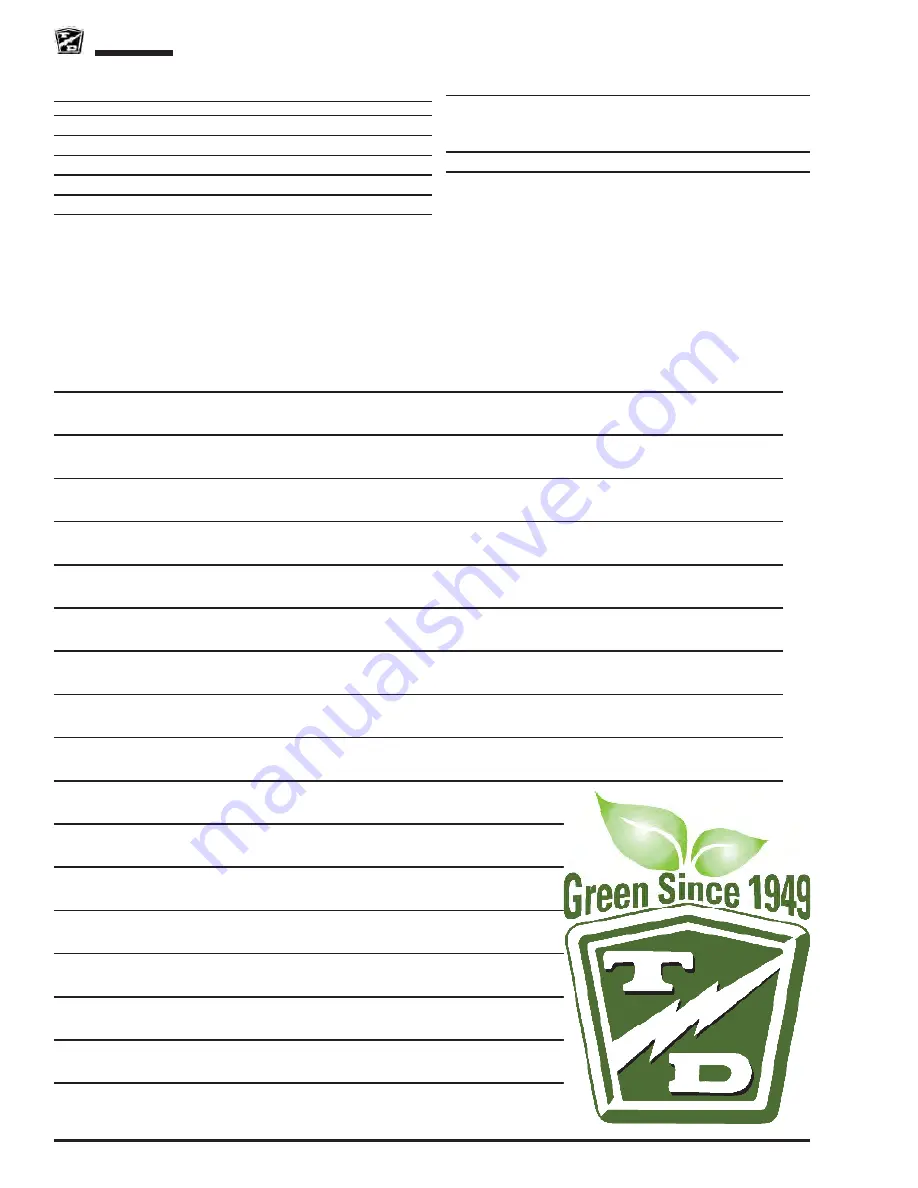
Brakes
Page 60
Bigfoot G-1500
MB-440-10
Notes
:
HARDWARE TORQUE
If hardware is not listed here, refer to standard torque
values in the appendix.
Description
Foot Pounds Newton Meters
Brake Body Bolts
11
14.9
SERVICE LIMITS
Description
Imperial Metric
Disc pad lining minimum thickness
00625 inch
1.58 mm
Front rotor minimum thickness
0.200 inch
5.08 mm
Rotor runout
0.005 inch
0.127 mm
Rear shoe lining minimum thickness
0.200 inch
5.08 mm
Rear drum maximum diameter
6.33 inch
160.8 mm
Содержание B5-440-GAS
Страница 6: ......
Страница 12: ...Page 12 MB 440 10 Introduction Bigfoot G 1500 Notes ...
Страница 20: ...PM Schedule Page 20 Bigfoot G 1500 MB 440 10 Notes ...
Страница 24: ...Lubrication Page 24 Bigfoot G 1500 MB 440 10 Notes ...
Страница 44: ...Engine Page 44 Bigfoot G 1500 MB 440 10 Notes ...
Страница 70: ...Tires Wheels Page 70 Bigfoot G 1500 MB 440 10 Notes ...
Страница 90: ...Replacement Parts Page 90 MB 440 10 Bigfoot G 1500 AXLE ASSEMBLY FRONT ...
Страница 94: ...Replacement Parts Page 94 MB 440 10 Bigfoot G 1500 BRAKES BRAKE LINES ...
Страница 98: ...Replacement Parts Page 98 MB 440 10 Bigfoot G 1500 DECALS ...
Страница 100: ...Replacement Parts Page 100 MB 440 10 Bigfoot G 1500 ELECTRICAL MISCELLANEOUS ...
Страница 110: ...Replacement Parts Page 110 MB 440 10 Bigfoot G 1500 STEERING LINKAGE ...
Страница 116: ...Replacement Parts Page 116 MB 440 10 Bigfoot G 1500 Notes ...