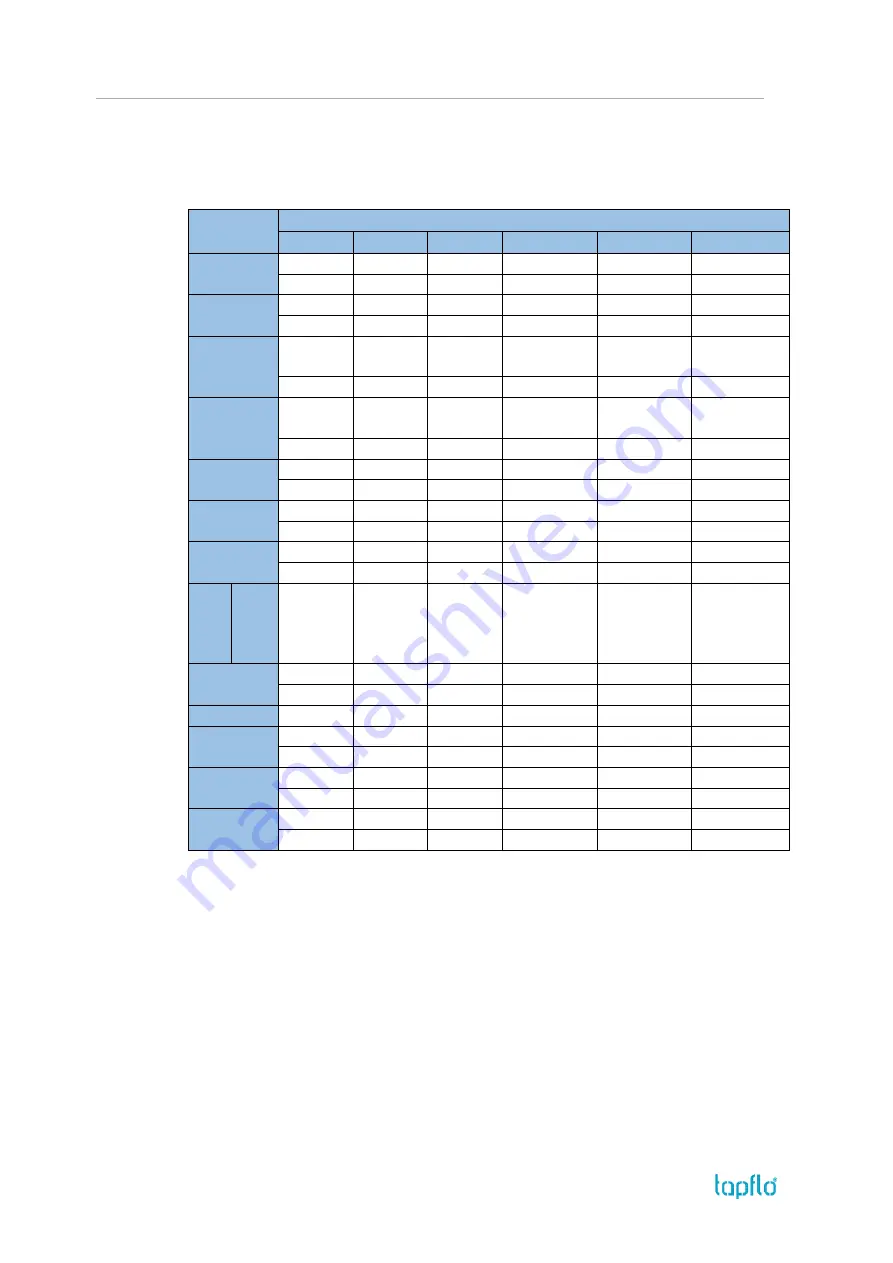
6. DATA
Tapflo sanitary pump series
43
6.3.
Dimensions
Dimensions in mm (where other is not indicated)
Dimensions in inch (where other is not indicated)
General dimensions only, ask us for detailed drawings. Changes reserved without notice.
Dimension
PUMP SIZE
T30
T80
T125
T225
T425
T825
A
169
295
320
404
468
750
6.7
11.6
12.6
15.9
18.4
29.5
B
153
303
328
412
476
760
6
11.9
12.9
16.2
18.7
29.9
D
313
393
458
647 / 792** 808 / 950**
1288 /
1495**
12.3
15.5
18
25.5 / 31.1
31.8 / 37.4
50.7 / 58.8
E
240
294
350
528 / 690** 664 / 775**
1034.5 /
1270**
9.4
11.6
13.8
20.6 / 27.2
26.1 / 30.5
40.7 / 50
G
34
10
10
10
10
20
1.3
0.4
0.4
0.4
0.4
0.8
H
30
30
30
30
30
60
1.2
1.2
1.2
1.2
1.2
2.4
I
48
74.5
82.5
86.5 / 70** 98.5 / 140** 206.5 / 165**
1.9
2.9
3.2
3.4 / 2.8
3.9 / 5.5
8.1 / 6.5
J
TC
1
DIN
2
SMS
3
RJT
4
25
DN20
25
¾"
25
DN25
25
1"
38
DN40
38
1 ½"
51
DN50
51
2”
70
DN65
63.5
3”
76.1
DN80
76.1
3 ½”
Ø
K
9
9
9
9
9
25x13
0.4
0.4
0.4
0.4
0.4
1x0.5
L
G 1/8”
G ¼”
G ¼”
G ½”
G ½”
G ½”
Ø
M*
50.5
50.5
50.5
64
91
98 / 119**
2.0
2.0
2.0
2.5
3.6
3.9 / 4.7
Ø
N*
22.6
22.6
35.6
48.6
66.8
72.9 / 100**
0.9
0.9
1.4
1.9
2.6
2.9 / 3.9
X
125
275
300
384
448
710
4.9
10.8
11.8
15.1
17.6
28
* = Dimensions for standard clamp connections only
** = Dimensions with flap valves and heavy duty valve cup version
1 = Clamp connections according to SMS3017 (T30 – T225) / ISO2037 (T425-T825)
2 = Threaded connections according to DIN 11851
3 = Threaded connections according to SMS 1145
4 = Threaded connections according to BS 4825-5
Содержание Sanitary Series
Страница 44: ...6 DATA Tapflo sanitary pump series 44 ...