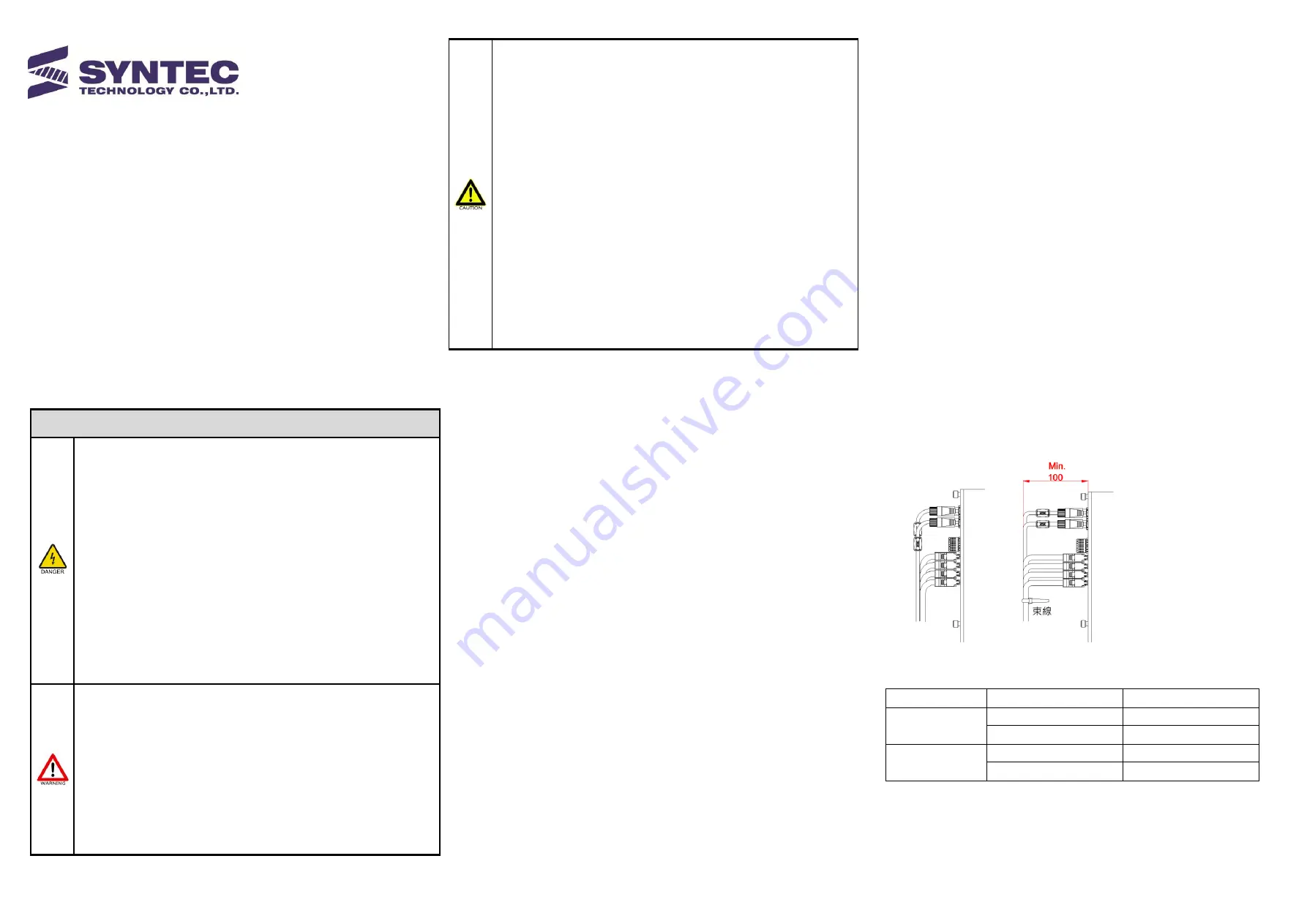
B01-NOT-DRIVER-03
Generation II Driver Notifications
Notifications
V1.2
Dear users, please go through the instructions in detail before the installation. Also,
please hand the manual to the actual operator of the machine and preserve it properly.
Drivers are precision electronic devices. For the safety of both operators and the
machine, please ensure all installations, tests and adjustments are operated by professional
personnel. For the description with “
DANGER
”, “
WARNING
” and “
CAUTION
” in the manual,
please read them in detail. If there are any concerns, please contact our branches in your
region. Our professionals are glad to be at your service. The following are the guidelines
you should comply with before finishing reading the complete manual:
The installing environment should be indoor and without water vapor, corrosive or
flammable gas.
Implement the wirings according to the wiring diagram.
The grounding must be strictly implemented and follow the current National Electrical
Code. (References: NFPA 70: National Electrical Code,2005 Ed.)
Do not modify the wirings while the device is powered up.
1.
Safety Precautions
2.
Installation Notifications:
The leakage current of an all-in-one driver is usually over 3.5 mA. In accordance with
EN 61800-5-1, fixed installation is required.
The direction of the installation must be in accordance with the regulations,
otherwise it will cause servo failures.
When installing the driver, the air intake and vent holes should not be sealed, and the
driver should not be tipped; otherwise it will cause malfunctions.
Do not install the driver near flammable materials.
Ensure every mounting hole is locked up when fixing the driver.
Ensure the installation surface can support the weight of the driver.
3.
Wiring and Other Notifications
When using a solenoid valve or other inductive loads, please apply an arc extinguisher
or an RC voltage dependent resistor to ensure the life of the contact points.
Advantages of the arc extinguisher:
1) Extend the life of electrical contacts.
2) Reduce the sparks from the contact points.
3) Prevent the inductive loads from interferences caused by back EMF.
4) Restrain the impulse voltage.
Do not connect other cables to extend the original length. It might cause signal errors
or malfunction.
Please crimp or weld the wire connections while doing the wirings.
If the servo line in use is not a standard Syntec cable, please verify all the terminals
are connected properly before power-on. Wrong wirings will lead to controller output
command errors and malfunction.
The +5V output capacity of the encoder is 500mA and is only for a single encoder. Do
not connect it with other loads or it might cause error due to the lack of driving force.
Do not use counterfeit terminal strips. Those terminal strips cannot provide overall
protection for the system. The quality is also not guaranteed and tend to cause
electrical control problems of the machine tools
Do not stake on top.
The six power lines, R, S, T and U, V, W, should not be close to other signal lines, and
should be at least 30 cm apart.
After cutting off the power, the capacitor of the driver still contains large amount of
charge. Do not touch the 6 power lines, R, S, T and U, V, W, until the power indicator
goes out.
If the encoder line should be longer, please use twisted-pair and signal cable with
isolated ground. Do not extend it over 20 meters. In case of extensions over 20
meters, please double the wire diameter of signal cables to reduce signal attenuation.
The driver is fragile. Please handle it with care.
Do not allow conductive foreign matter such as screws or metal chips, or combustible
foreign matter such as oil enter the driver.
Applicable motor types
:
Please refer to the catalogue.
It is suggested that M3 communication and encoder cables be hung loosely (Left
Figure). If bundling is needed (Right Figure), please leave at least 100mm between the
M3 wire connector and the bend to avoid poor contact of the connector.
(Hang loosely) (Tied up)
Please follow the wire diameter regulations. The suggested choice of wire diameter
varies with the motor wattage. Please refer to the table below
:
Type
Wattage
Wire Diameter
Axial
100W~850W
20AWG
850W~7.5kW
16AWG
Spindle
Below 7.5kW
12AWG
Above 11kW
10AWG
Please connect the ground wire to class-3 (under 100Ω). Poor grounding might cause
signal error, electric shock, or fire.
The grounding of the motor must be connected to one of the grounding terminals of
the frequency converter.
In accordance with EN 61800-5-1 (Section 4.3.5.5.2), since the normal contact current
Please pay extra attention to the instructions below while operating the product.
Install the driver according to the instructions in the manual or it might
cause damage to the equipment.
Do not operate the product in places exposed to water vapor, corrosive or
flammable gases. It might cause damage to the device, electric shocks,
fire or explosion.
Do not install the product at a temperature exceeding the specified range.
It might cause device damage or malfunctioning.
The driver series are designed to control the motors. Do not touch the
internal circuits or parts while the driver is powered up.
The internal circuit board of the driver contains CMOS ICs, which are
vulnerable to static electricity. Do not touch the circuit board with your
hands before taking any precautions.
The product has been certified by EN 61800-5-1/EN 61800-3. It is for use in
industrial environments.
Do not apply the product to machines that might lead to casualties, device
damage or system shut down.
Please cut off all the external device loads when powering up the driver for
the first time in case the built-in testing program starts running the motor
immediately after power input. It may be dangerous for the operators
around.
The driver is a precision instrument. Please prevent non-maintenance staff
or non-professional electronic control personnel from disassembling the
device.
Please apply the correct ground loop to prevent signal errors.
Please separate the communication cable of the driver from all the other
motor and power cables with individual wiring ducks to prevent the
controller from malfunction caused by large noise interference.
The driver adopts microcomputer design. Please install the driver in a safe
area and keep the area clean. Please keep iron shavings, wires, water,
corrosive gas and liquid from the driver to avoid malfunctioning.
Please reserve at least 50mm in width for ventilation and heat dissipation.
The grounding of the driver and machine tool system is necessary for leakage
protection and prevention of lightning strikes. Please ensure the driver and
the machine tool system are grounded properly before installing.
The power system of the driver should meet the rated voltage. If the
operating environment provides an unstable voltage source, please apply a
voltage stabilizer so that the driver can function properly.
Please turn off the power before plugging/unplugging the cables or
modifying the wirings to prevent electric shocks or damage to the driver.
Please make sure all the terminals are in the correct positions while wiring to
prevent the driver from damage caused by wiring mistakes.
Do not touch the terminals within 10 minutes after cutting off the power in
case that the residual voltage might cause electric shocks.
Unload the driver after the driver is powered off after 30 minutes.
To ensure communication quality, the length of USB extension cords in use
shall not exceed five meters. Besides, do not charge or supply power via the
USB port; otherwise, it may cause controller malfunction.