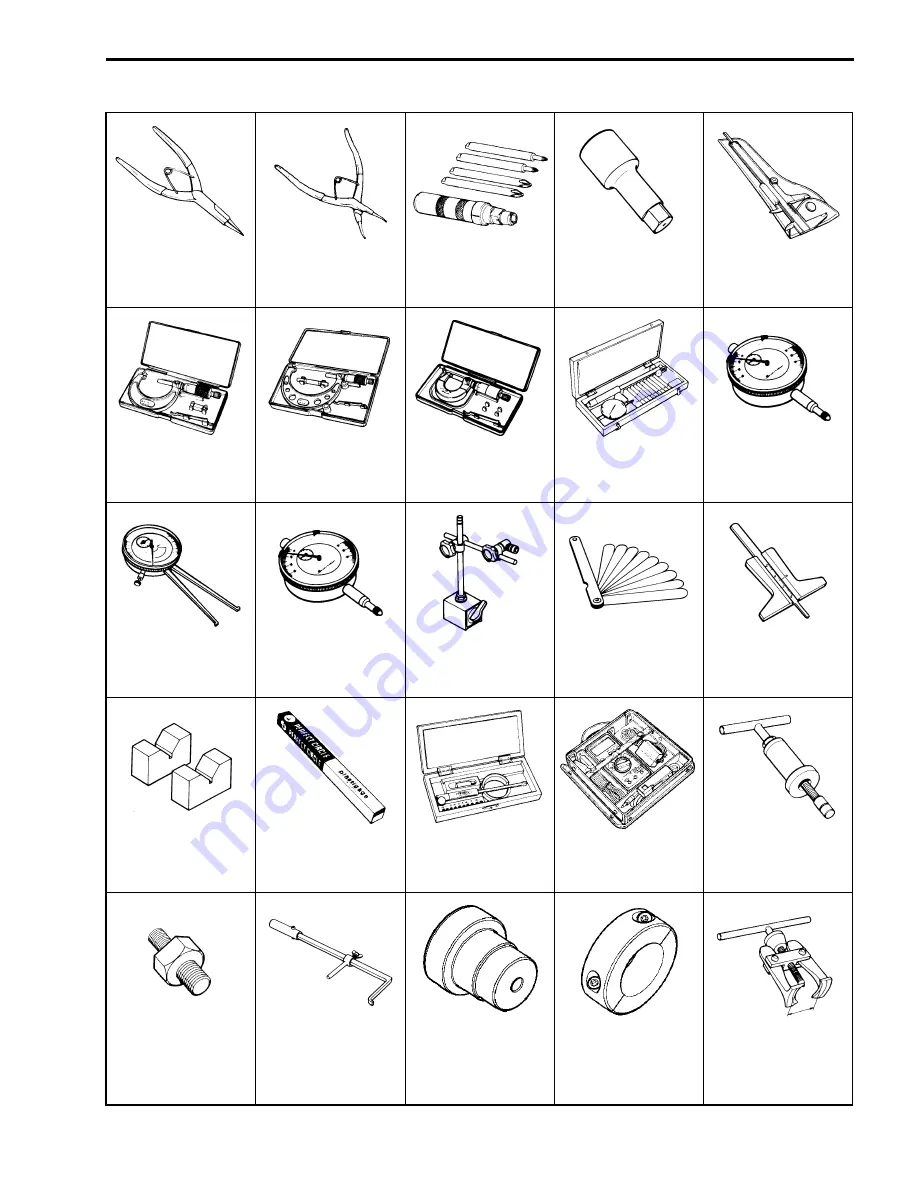
SERVICING INFORMATION 11-29
SPECIAL TOOLS
09900-06107
Snap ring pliers
09900-06108
Snap ring pliers
09900-09004
Impact driver set
09900-18710
Hexagon socket
12 mm
09900-20102
Vernier calipers
09900-20202
Micrometer
(25 – 50 mm)
09900-20204
Micrometer
(75 – 100 mm)
09900-20205
Micrometer
(0 – 25 mm)
09900-20508
Cylinder gauge set
09900-20602
Dial gauge
(1/1000 mm, 1 mm)
09900-20605
Dial gauge
09900-20607
Dial gauge
(1/100 mm, 10 mm)
09900-20701
Magnetic stand
09900-20803
09900-20806
Thickness gauge
09900-20805
Tire depth gauge
09900-21304
V-block (100 mm)
09900-22301
09900-22302
Plastigauge
09900-22401
Small bore gauge
(10 – 18 mm)
09900-25008
Multi circuit tester
set
09910-32812
Crankshaft installer
09910-32850
Crankshaft installer
attachment
09913-50121
Oil seal remover
09913-60210
09913-60230
Journal bearing
remover/installer
09913-60241
Journal bearing
holder
09913-60912 or
09913-61110 or
09913-61510
Bearing puller
Содержание AN650 2002
Страница 1: ......
Страница 47: ...PERIODIC MAINTENANCE 2 29 ...
Страница 124: ...ENGINE 3 73 POSITION OF CAMSHAFTS AND SPROCKETS 15 1 1 2 2 3 3 ...
Страница 137: ...CVT 5 3 Remove the CVT mounting bolts Remove the CVT assembly ...
Страница 177: ...6 16 FI SYSTEM CVT SYSTEM E Serial communication G Speed signal Speed sensor H Engine rpm Crankshaft position sensor ...
Страница 425: ...SERVICING INFORMATION 11 21 FUEL TANK MOUNTING ...
Страница 426: ...11 22 SERVICING INFORMATION FUEL TANK MOUNTING Only for E 28 ...
Страница 427: ...SERVICING INFORMATION 11 23 FUEL TANK HOSE ROUTING Clamp Orange Black Gray Black 5 8 mm 5 8 mm 5 mm TPC valve TPC valve ...
Страница 462: ...Prepared by July 2002 Part No 99500 36110 01E Printed in Japan 464 ...
Страница 463: ......