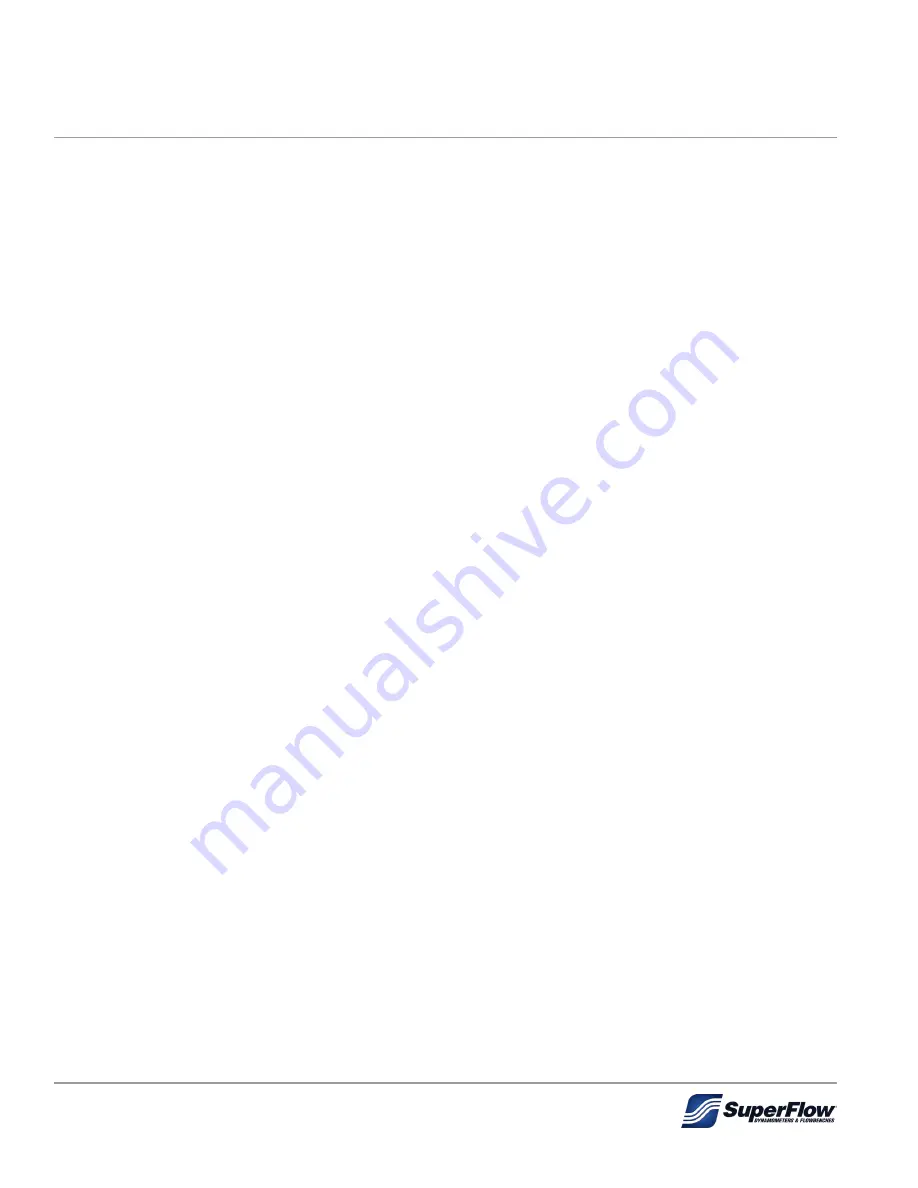
2
2.0 Safety Guidelines
Safety is the most important consideration when operating any machine. Operators and service personnel
should read this manual and become familiar with its content before attempting to operate this machine
or to perform service or maintenance to it. Familiarization with this manual will minimize the possibility of
accidents or injuries. Although the procedures covered in this manual have proven safe in use, SuperFlow
assumes no responsibility for personal injury or damage to equipment resulting from its applications. All
operators must be aware that there are several hazards present to anyone in the vicinity during operation.
Some of these hazards are:
• Hearing damage due to high noise levels
• Electrical shock
• Exposure to rotating parts
Always follow basic safety precautions when using this product to reduce risk of injury or damage to
equipment.
•
Only authorized personnel knowledgable of the operation of the flowbench should have access to
the equipment.
• Read and understand all instructions in the user guides.
• Keep the air ducts free of dust or dirt.
• Keep loose material away from the inlet and exhaust ducts.
• Always wear eye and hearing protection whenever operating.
• Use only the proper electrical sources. Ensure circuit breakers are easily accessible and have the
proper rating.
• Observe all warnings and instructions marked on the product.
•
Provide fire extinguishers that are rated for electrical and oils.
• Provide adequate lighting in the test area.
•
Refer all service questions to qualified personnel.
• Do not remove any safety guards while the machine is in operation, and be sure the safety guards
are correctly mounted before operating the device.
• Disconnect the external power switch before opening the rear panel of the device.
• Replace the power cable if it is damaged.
•
Do not store flammable materials in the vicinity of the flowbench.
• Follow all local construction codes.
These are general guidelines for working with any machine. It is often helpful to prepare a safety checklist
that is distributed to all personnel who enter the test cell. Proper safety is achieved through reinforcement
and discipline.